Atmospheric Pressure Chemical Vapor Deposition (APCVD) is a synthesis method used to deposit thin films or coatings on substrates by exposing them to volatile precursors at atmospheric pressure. These precursors react or decompose on the substrate surface, forming a solid deposit. APCVD is known for its simplicity, cost-effectiveness, and high deposition rates, making it suitable for applications in electronics, cutting tools, and energy industries. It is particularly useful for depositing oxides, semiconductors, and other materials like polysilicon and silicon dioxide. The process operates at normal atmospheric pressure, which distinguishes it from other CVD methods that require vacuum conditions.
Key Points Explained:
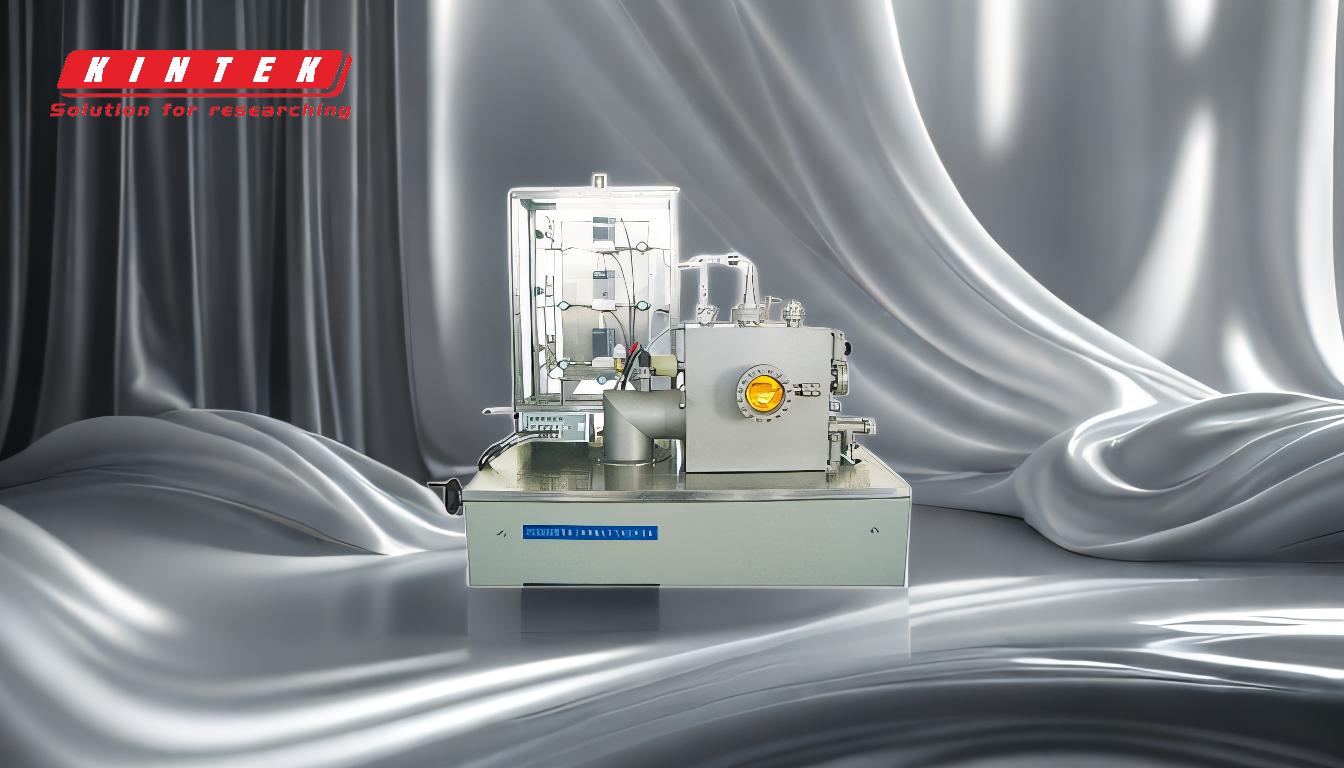
-
Definition and Process Overview:
- APCVD is a chemical vapor deposition (CVD) technique that operates at atmospheric pressure (1 atm).
- It involves exposing a substrate to volatile precursors that react or decompose on the surface to form a thin film or coating.
- The process is characterized by its simplicity and ability to operate without the need for vacuum systems.
-
Key Characteristics:
- Atmospheric Pressure Operation: Unlike other CVD methods, APCVD does not require vacuum conditions, reducing equipment complexity and cost.
- High Deposition Rates: The process is known for its efficiency in producing thick films quickly.
- Cost-Effectiveness: The absence of vacuum systems and simpler equipment make APCVD a low-cost option for thin-film deposition.
- Material Versatility: APCVD can deposit a wide range of materials, including oxides, semiconductors, and ceramics.
-
Applications:
- Electronics: APCVD is used to deposit thin films on semiconductors, which are essential for manufacturing integrated circuits and other electronic components.
- Cutting Tools: The technique is employed to coat cutting tools with wear-resistant and corrosion-resistant layers, enhancing their durability.
- Energy: APCVD is used in the production of thin-film solar cells, where photovoltaic materials are deposited on substrates to create efficient solar panels.
- Industrial Coatings: It is also used to coat turbine blades and other industrial components to improve their performance and lifespan.
-
Materials Produced:
- Polysilicon: Used in semiconductor manufacturing.
- Silicon Dioxide (SiO₂): A key material in electronics for insulating layers.
- Phosphosilicate Glass: Used in passivation layers and as a dielectric material.
- Oxides and Ceramics: For applications requiring high thermal and chemical stability.
-
Advantages:
- Simplicity: The process is straightforward and does not require complex vacuum systems.
- Scalability: APCVD is suitable for large-scale production due to its high deposition rates.
- Performance: Films produced by APCVD are known for their long service life and excellent performance in various applications.
-
Limitations:
- Precursor Control: Operating at atmospheric pressure can make it challenging to control precursor concentrations precisely.
- Film Uniformity: Achieving uniform film thickness across large substrates can be more difficult compared to low-pressure CVD methods.
- Contamination Risk: The open nature of the process may increase the risk of contamination from ambient gases.
-
Comparison with Other CVD Methods:
- Low-Pressure CVD (LPCVD): Operates under vacuum, offering better control over film quality and uniformity but at higher costs.
- Plasma-Enhanced CVD (PECVD): Uses plasma to enhance chemical reactions, allowing deposition at lower temperatures but requiring more complex equipment.
- APCVD: Balances cost, simplicity, and efficiency, making it ideal for applications where high deposition rates and cost-effectiveness are prioritized over ultra-high precision.
-
Future Prospects:
- APCVD continues to evolve with ongoing research aimed at improving precursor delivery, reaction control, and film quality.
- Its applications are expanding into emerging fields such as nanotechnology, where precise material deposition is critical for developing advanced devices and structures.
In summary, Atmospheric Pressure Chemical Vapor Deposition (APCVD) is a versatile and cost-effective method for depositing thin films and coatings at atmospheric pressure. Its simplicity, high deposition rates, and material versatility make it a valuable tool in industries ranging from electronics to energy. While it has some limitations, ongoing advancements are likely to enhance its capabilities and broaden its applications.
Summary Table:
Aspect | Details |
---|---|
Definition | A CVD technique operating at atmospheric pressure (1 atm). |
Key Characteristics | - No vacuum required |
- High deposition rates
- Cost-effective
- Material versatility | | Applications | Electronics, cutting tools, energy (solar cells), industrial coatings. | | Materials Produced | Polysilicon, silicon dioxide, phosphosilicate glass, oxides, ceramics. | | Advantages | Simplicity, scalability, high performance. | | Limitations | Precursor control, film uniformity, contamination risk. | | Comparison with CVD | Balances cost, simplicity, and efficiency vs. LPCVD and PECVD. | | Future Prospects | Expanding into nanotechnology and improving film quality. |
Discover how APCVD can enhance your production processes—contact us today for expert guidance!