Chemical Vapor Deposition (CVD) is a sophisticated materials processing technology used to deposit thin films or coatings on a substrate through chemical reactions involving gas-phase precursors. The process occurs in a controlled environment, typically a vacuum chamber, where precursor gases are introduced, and chemical reactions are induced by heat, plasma, or other energy sources. These reactions result in the formation of a solid material that adheres to the substrate, creating a uniform and high-quality layer. CVD is widely used in industries such as semiconductors, optics, and coatings due to its ability to produce precise, durable, and high-performance materials. The process can be tailored using various methods, such as atmospheric pressure CVD, plasma-assisted CVD, or laser-assisted CVD, depending on the desired outcome.
Key Points Explained:
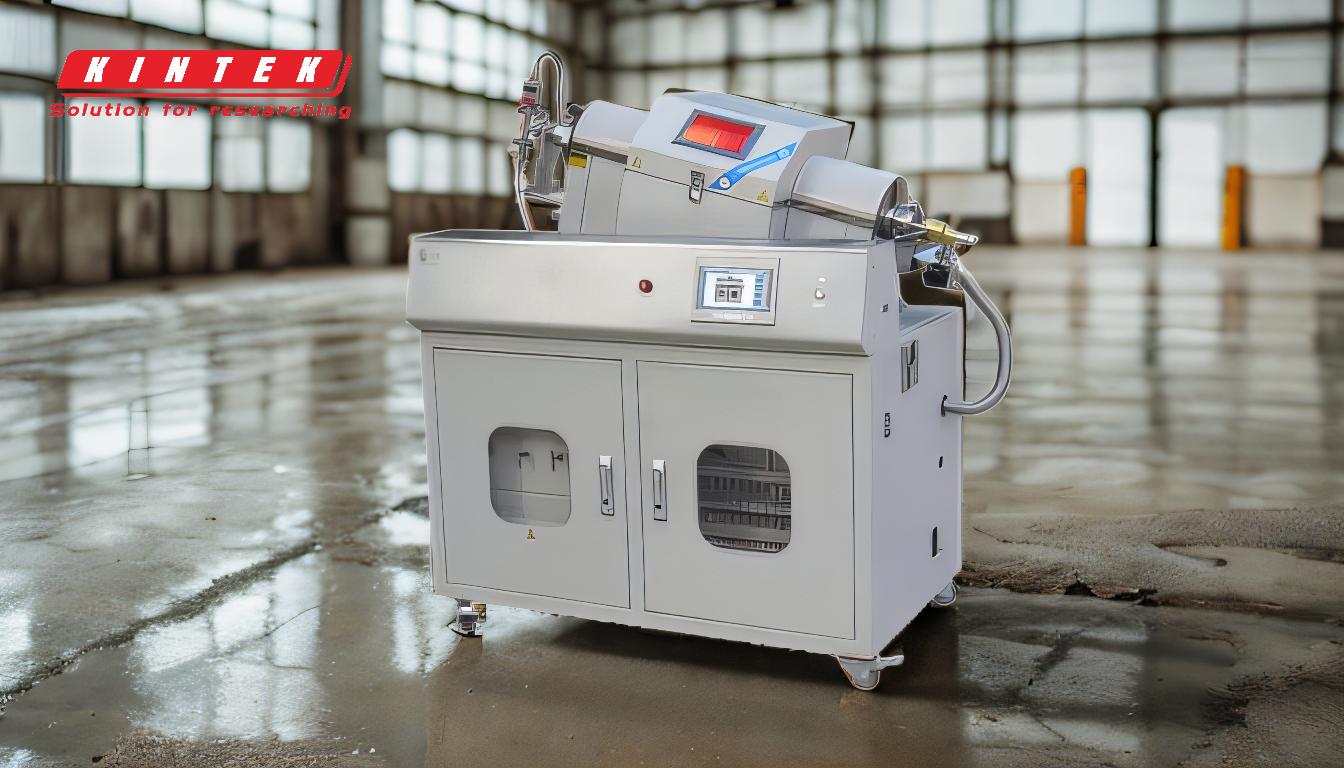
-
Definition and Purpose of CVD:
- CVD is a process used to create thin films or coatings on a substrate by inducing chemical reactions between gas-phase precursors.
- The primary purpose is to produce high-quality, high-performance materials with precise control over thickness, composition, and properties.
-
Basic Principle of CVD:
- Gaseous precursors are introduced into a reaction chamber under controlled conditions of temperature, pressure, and flow rate.
- These precursors undergo chemical reactions, such as decomposition or composition, on the surface of a heated substrate.
- The reactions result in the formation of a solid material that adheres to the substrate, forming a thin film.
-
Key Components of the CVD Process:
- Precursor Gases: Volatile compounds that provide the necessary chemical elements for the reaction.
- Reaction Chamber: A controlled environment, often a vacuum chamber, where the chemical reactions take place.
- Substrate: The material onto which the thin film is deposited. It is typically heated to facilitate the reaction.
- Energy Source: Heat, plasma, or laser energy is used to activate the chemical reactions.
-
Types of CVD Processes:
- Atmospheric Pressure CVD (APCVD): Conducted at atmospheric pressure, suitable for large-scale production.
- Plasma-Assisted CVD (PACVD): Uses plasma to enhance the chemical reactions, enabling lower temperatures and faster deposition rates.
- Laser-Assisted CVD (LACVD): Utilizes laser energy to precisely control the deposition process, ideal for localized coatings.
- Metal-Organic CVD (MOCVD): Employs metal-organic compounds as precursors, commonly used in semiconductor manufacturing.
-
Steps in the CVD Process:
- Introduction of Precursors: Gaseous precursors are introduced into the reaction chamber.
- Activation of Reactions: Heat, plasma, or other energy sources activate the chemical reactions.
- Deposition: The reaction products form a solid layer on the substrate.
- Removal of By-products: Volatile by-products are removed from the chamber via gas flow.
-
Advantages of CVD:
- High-Quality Films: Produces uniform, dense, and high-purity coatings.
- Versatility: Can deposit a wide range of materials, including metals, ceramics, and polymers.
- Precision: Allows precise control over film thickness and composition.
- Scalability: Suitable for both small-scale and industrial applications.
-
Applications of CVD:
- Semiconductors: Used to deposit thin films for integrated circuits and electronic devices.
- Optics: Produces anti-reflective and protective coatings for lenses and mirrors.
- Coatings: Creates wear-resistant, corrosion-resistant, and thermal barrier coatings.
- Nanotechnology: Enables the fabrication of nanostructured materials and devices.
-
Challenges and Considerations:
- Cost: High equipment and operational costs, especially for advanced CVD techniques.
- Complexity: Requires precise control over process parameters.
- Safety: Handling of toxic or hazardous precursor gases necessitates stringent safety measures.
In summary, Chemical Vapor Deposition is a versatile and precise method for depositing thin films and coatings, essential for advanced materials and technologies. Its ability to produce high-quality, durable, and tailored materials makes it indispensable in industries ranging from electronics to aerospace.
Summary Table:
Aspect | Details |
---|---|
Definition | CVD deposits thin films on substrates via gas-phase chemical reactions. |
Key Components | Precursor gases, reaction chamber, substrate, and energy source. |
Types of CVD | APCVD, PACVD, LACVD, MOCVD. |
Advantages | High-quality films, versatility, precision, scalability. |
Applications | Semiconductors, optics, coatings, nanotechnology. |
Challenges | High cost, process complexity, safety concerns. |
Discover how CVD can revolutionize your materials processing—contact our experts today!