Dry ashing experiments are commonly used to determine the inorganic residue (ash) content of materials by oxidizing organic matter at high temperatures. The process typically involves a muffle furnace, which provides controlled heating in an air environment. Materials such as plastics, paints, food, coal, and hydrocarbons are often tested. Containers made of quartz, Pyrex, porcelain, steel, or platinum are used to hold samples during the process. Dry ashing is performed at around 500°C, though some materials may require higher or lower temperatures depending on their stability. The technique is widely used in laboratories for its simplicity and effectiveness in isolating inorganic components.
Key Points Explained:
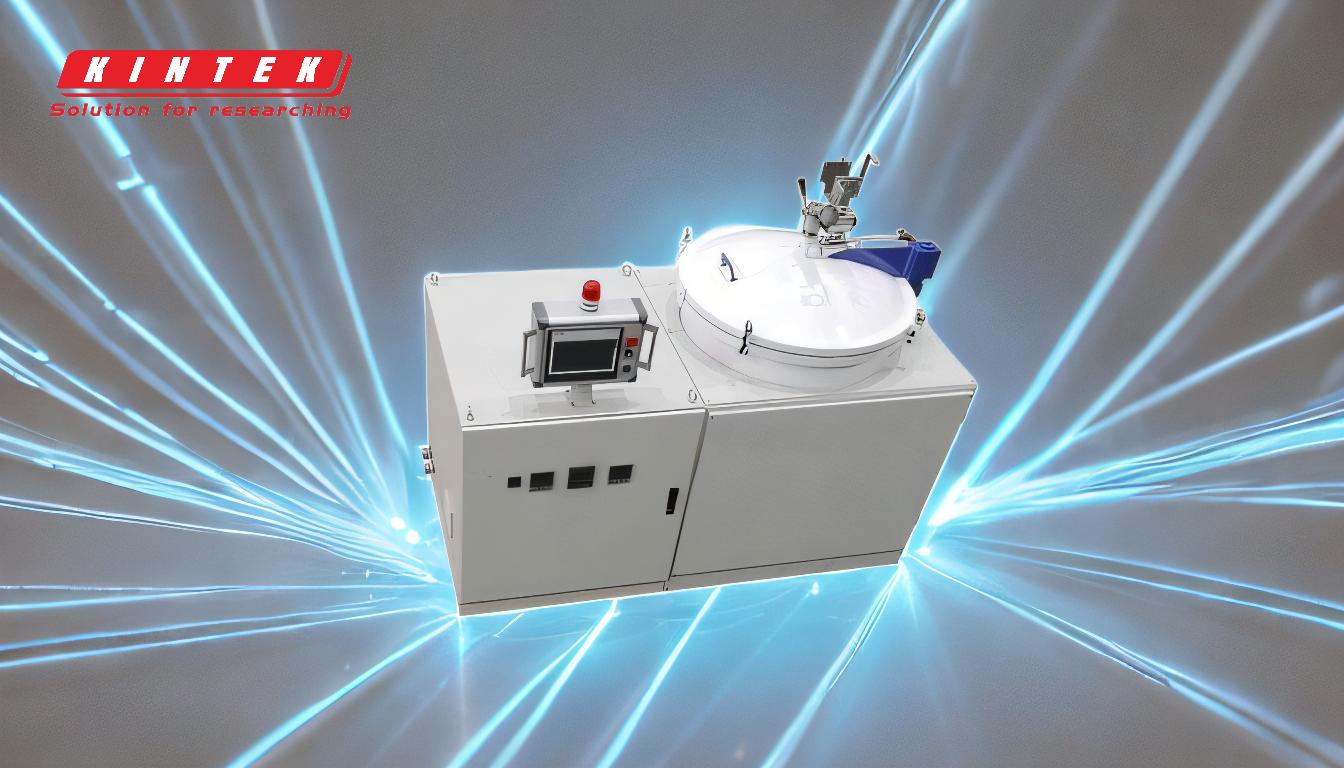
-
Muffle Furnace:
- A muffle furnace is the primary equipment used in dry ashing experiments. It provides a controlled environment for heating samples to high temperatures (typically around 500°C) in the presence of air.
- The furnace ensures uniform heating and oxidation of organic materials, leaving behind inorganic residue (ash).
- High-quality muffle furnaces are preferred for their precision and reliability in maintaining consistent temperatures.
-
Materials Tested:
- Dry ashing is commonly applied to materials such as plastics, paints, food, coal, and hydrocarbons.
- These materials are chosen because they contain organic components that can be oxidized at high temperatures, leaving behind measurable inorganic residues.
-
Containers for Ashing:
- Samples are placed in containers made of materials that can withstand high temperatures without reacting with the sample or degrading.
- Common container materials include:
- Quartz: Resistant to high temperatures and chemical corrosion.
- Pyrex: Suitable for moderate temperatures and widely used in laboratories.
- Porcelain: Durable and cost-effective for general use.
- Steel: Used for specific applications requiring high mechanical strength.
- Platinum: Ideal for high-precision experiments due to its inertness and high melting point.
-
Temperature Range:
- Dry ashing is typically performed at around 500°C, which is sufficient to oxidize most organic materials.
- Some materials, such as polymers and rubbers, may require higher temperatures (up to 900°C) if they are thermally stable.
- Lower temperatures (around 200°C) are used in low-temperature ashing techniques for heat-sensitive materials.
-
Process of Dry Ashing:
- The sample is placed in a suitable container and heated in the muffle furnace.
- Organic components in the sample are oxidized and volatilized, leaving behind inorganic ash.
- The process is carefully controlled to ensure complete combustion without losing volatile inorganic components.
-
Applications:
- Dry ashing is widely used in laboratories for:
- Determining the ash content of food products (e.g., cereals, dairy).
- Analyzing the inorganic content of plastics and polymers.
- Assessing the quality of coal and hydrocarbons.
- Studying the composition of paints and coatings.
- Dry ashing is widely used in laboratories for:
-
Advantages of Dry Ashing:
- Simple and cost-effective method for ash determination.
- Suitable for a wide range of materials.
- Provides accurate results for inorganic residue analysis.
-
Limitations:
- Not suitable for materials that decompose or volatilize at high temperatures.
- Potential loss of volatile inorganic components during the process.
- Requires careful selection of container materials to avoid contamination.
By understanding these key points, a purchaser can make informed decisions about the equipment and consumables needed for dry ashing experiments, ensuring accurate and reliable results.
Summary Table:
Aspect | Details |
---|---|
Equipment | Muffle furnace for controlled heating at high temperatures (~500°C). |
Materials Tested | Plastics, paints, food, coal, hydrocarbons. |
Container Materials | Quartz, Pyrex, porcelain, steel, platinum. |
Temperature Range | 200°C to 900°C, depending on material stability. |
Applications | Food ash content, plastic analysis, coal quality, paint composition. |
Advantages | Simple, cost-effective, accurate inorganic residue analysis. |
Limitations | Unsuitable for volatile materials; risk of losing inorganic components. |
Need help setting up your dry ashing experiments? Contact our experts today for tailored solutions!