Chemical Vapor Deposition (CVD) is a versatile and widely used technique for depositing thin films and coatings with high purity and uniformity. It involves the chemical reaction of gaseous precursors to form a solid material on a substrate, typically at elevated temperatures. CVD is employed in various industries, including semiconductors, tool manufacturing, and even the production of synthetic diamonds. The process can be tailored to specific applications by adjusting parameters such as temperature, pressure, and gas composition. CVD is particularly valued for its ability to produce high-quality films for protective coatings, electrical circuits, and advanced materials like artificial diamonds.
Key Points Explained:
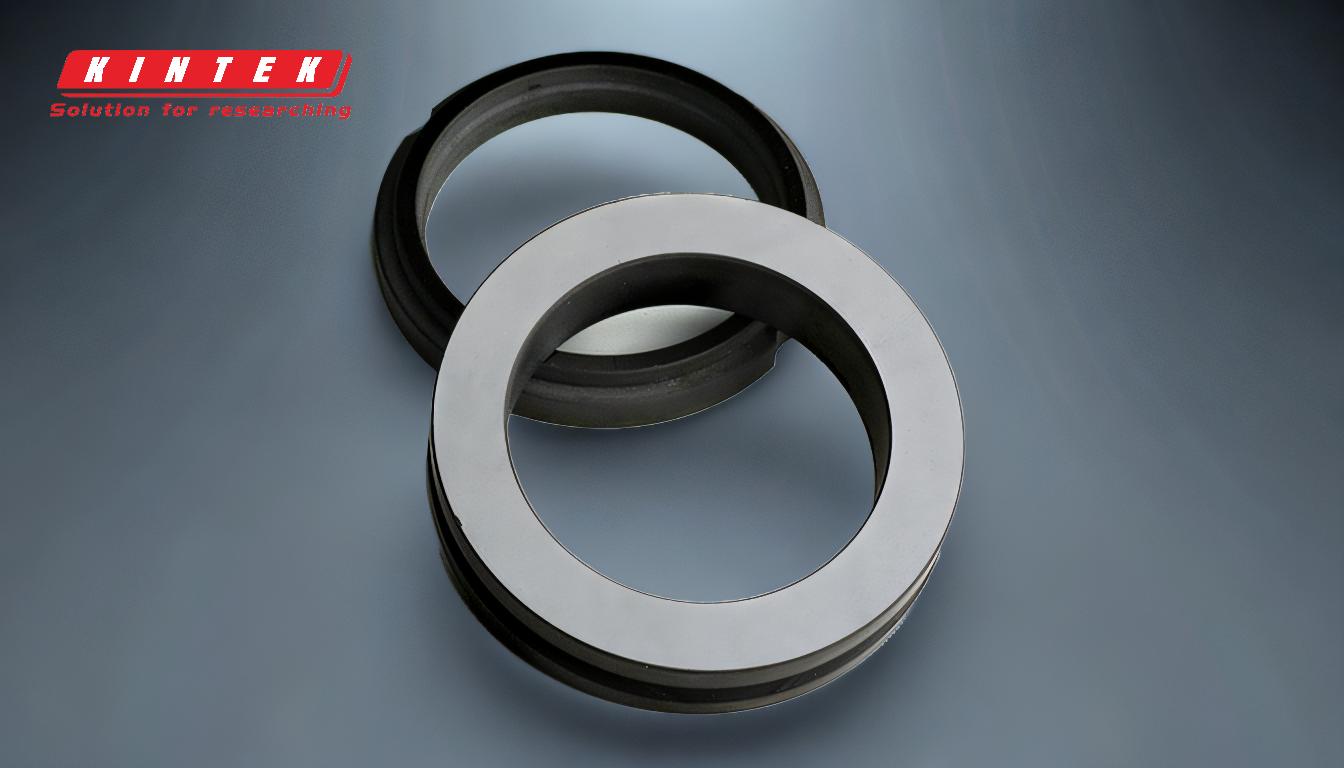
-
Definition and Mechanism of CVD:
- CVD is a process where a solid material is deposited from a vapor phase through chemical reactions occurring on or near a heated substrate surface. This is an example of a vapor-solid reaction.
- The process involves introducing gaseous precursors into a reactor, where they react or decompose to form a solid film on the substrate. The substrate is typically heated to facilitate the reaction.
-
Applications of CVD:
- Semiconductors: CVD is extensively used in the semiconductor industry to create thin films for various applications, such as patterning films, forming insulating layers (e.g., STI, PMD, IMD), and depositing conductive metals in electrical circuits.
- Protective Coatings: CVD is used to produce hard, durable coatings for machine tools, medical instruments, and automotive components, enhancing their wear resistance and longevity.
- Artificial Diamonds: CVD is employed to grow synthetic diamonds by introducing carbon atoms into a gas reactor and depositing them layer by layer on a substrate. This process is used in both industrial and gem-quality diamond production.
-
Types of CVD Processes:
- Medium-Temperature CVD (MTCVD): Operates in the temperature range of 700–900°C and is used for developing super cemented carbide coatings. It addresses challenges in high-speed cutting and heavy machining applications.
- High-Temperature CVD (HTCVD): Often used in combination with MTCVD for advanced material research and development. It involves higher temperatures and is suitable for more demanding applications.
-
Process Parameters:
- Temperature: CVD processes typically require high temperatures (e.g., 700–1300°C) to facilitate the decomposition and reaction of gaseous precursors.
- Pressure: The reaction pressure can vary widely, from low pressures (e.g., 2 × 10³ Pa) to higher pressures, depending on the specific application.
- Gas Composition: The ratio of precursor gases (e.g., CH3CN, TiCl4, H2) is carefully controlled to achieve the desired film properties.
-
Advantages of CVD:
- High Purity and Uniformity: CVD produces films with excellent purity and uniformity, making it ideal for applications requiring precise material properties.
- Versatility: The process can be adapted to deposit a wide range of materials, including metals, ceramics, and semiconductors.
- Scalability: CVD is suitable for both small-scale research and large-scale industrial production.
-
Challenges and Limitations:
- Time-Consuming: Some CVD processes, such as diamond growth, can take several weeks to complete.
- Complexity: The process requires precise control of temperature, pressure, and gas composition, making it technically challenging.
- Cost: The equipment and energy requirements for CVD can be high, particularly for high-temperature processes.
-
Future Trends:
- Advanced Materials: Ongoing research focuses on developing new materials and coatings using CVD, particularly for applications in electronics, energy, and aerospace.
- Process Optimization: Efforts are being made to reduce the time and cost of CVD processes while maintaining or improving film quality.
In summary, CVD is a critical technology for producing high-quality thin films and coatings across various industries. Its ability to deliver precise, uniform, and pure materials makes it indispensable for applications ranging from semiconductors to synthetic diamonds. Despite its challenges, ongoing advancements in CVD techniques continue to expand its potential and applications.
Summary Table:
Aspect | Details |
---|---|
Definition | CVD is a process where gaseous precursors react to form solid films on a heated substrate. |
Applications | Semiconductors, protective coatings, synthetic diamonds. |
Types of CVD | Medium-Temperature CVD (700–900°C), High-Temperature CVD (higher temps). |
Key Parameters | Temperature (700–1300°C), pressure, gas composition. |
Advantages | High purity, uniformity, versatility, scalability. |
Challenges | Time-consuming, complex, high cost. |
Future Trends | Advanced materials, process optimization. |
Ready to explore the potential of CVD for your applications? Contact our experts today to learn more!