Fast sintering techniques, such as Flash Sintering (FS), represent an innovative approach to sintering that significantly reduces both the time and energy required to densify materials. Unlike traditional sintering, which involves prolonged heating at temperatures below the melting point of the material, fast sintering leverages electric fields to achieve rapid densification. This method is particularly advantageous for materials that are sensitive to prolonged high-temperature exposure, as it minimizes grain growth and other thermal degradation effects. The process is characterized by its ability to achieve full densification in mere seconds, making it a game-changer in industries requiring high-throughput and energy-efficient manufacturing.
Key Points Explained:
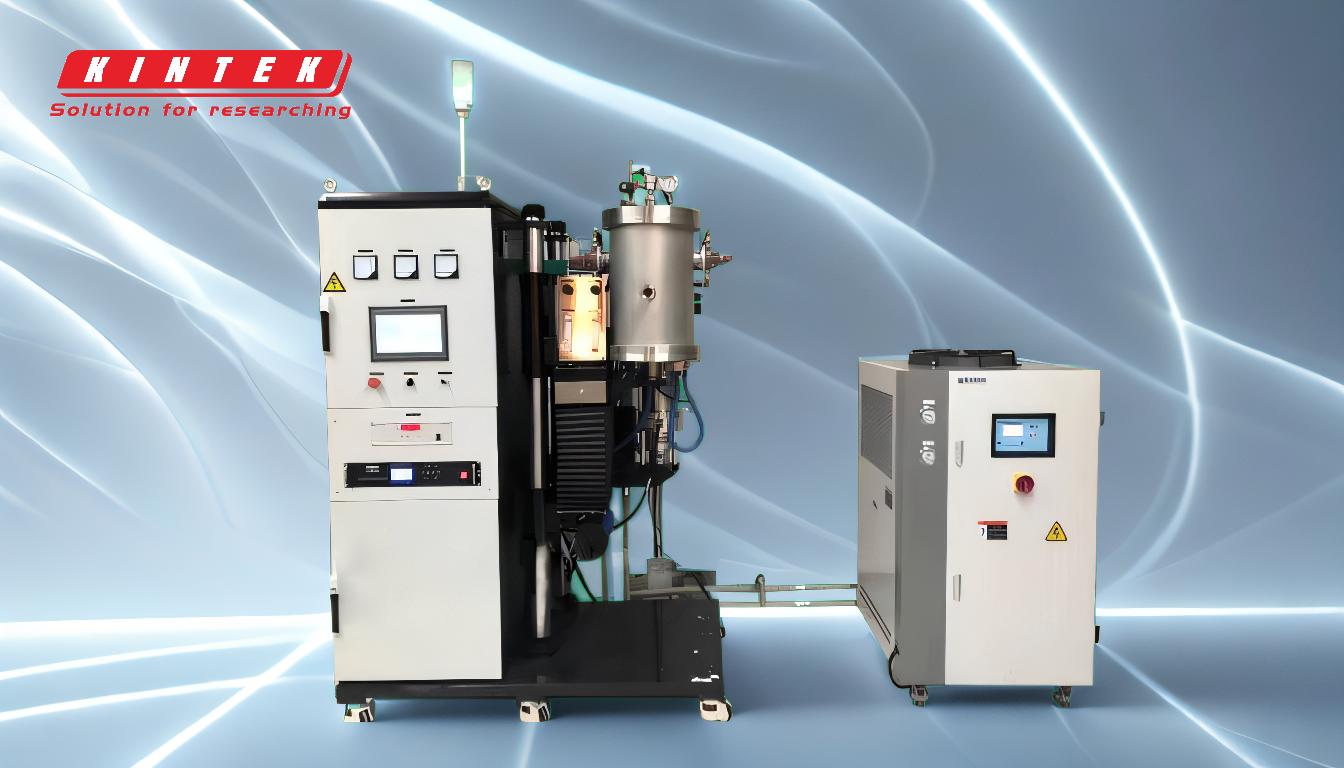
-
Definition of Fast Sintering:
- Fast sintering refers to advanced sintering techniques that drastically reduce the time and energy required to densify materials. Flash Sintering (FS) is a prime example, where an electric field is applied to the material, leading to rapid densification through phenomena like thermal runaway and Joule heating.
-
How Flash Sintering Works:
- Flash Sintering involves applying a DC or AC electric field to the material while it is heated in a furnace. Once a threshold temperature is reached, a sudden nonlinear increase in current generates intense Joule heating, which rapidly densifies the sample within seconds. This process is characterized by a sudden drop in resistivity and a flash phenomenon.
-
Advantages of Fast Sintering:
- Low Energy Consumption: Flash Sintering consumes significantly less energy compared to traditional sintering methods.
- Ultra-Fast Sintering Speed: Densification occurs in seconds, making it ideal for high-throughput manufacturing.
- Low-Temperature Sintering: The process can achieve densification at temperatures much lower than the material’s melting point, reducing thermal degradation.
- Improved Material Properties: Fast sintering minimizes grain growth and other thermal effects, leading to enhanced material properties.
-
Comparison with Traditional Sintering:
- Traditional sintering involves prolonged heating at temperatures below the melting point, which can lead to grain growth and other thermal degradation effects. In contrast, fast sintering achieves densification in a fraction of the time, with minimal thermal exposure.
-
Applications of Fast Sintering:
- Fast sintering is particularly beneficial for materials that are sensitive to prolonged high-temperature exposure. It is widely used in the manufacturing of ceramics, metals, and composites, where rapid densification and energy efficiency are critical.
-
Challenges and Future Directions:
- While fast sintering offers numerous advantages, challenges such as controlling the electric field and ensuring uniform densification remain. Ongoing research aims to optimize the process for a wider range of materials and applications.
Fast sintering techniques like Flash Sintering are revolutionizing the field of material densification by offering a faster, more energy-efficient alternative to traditional methods. As research continues to address existing challenges, the potential applications of this technology are expected to expand, further enhancing its impact on various industries.
Summary Table:
Aspect | Fast Sintering | Traditional Sintering |
---|---|---|
Time | Seconds | Hours to days |
Energy Consumption | Low | High |
Temperature | Below melting point | Below melting point, but prolonged exposure |
Material Properties | Minimized grain growth, enhanced properties | Potential grain growth and thermal degradation |
Applications | Ceramics, metals, composites (sensitive to high-temperature exposure) | Wide range, but less efficient for sensitive materials |
Learn how fast sintering can transform your manufacturing process—contact our experts today!