Furnace linings are essential components in various types of furnaces, serving multiple critical functions. They are designed to contain molten materials, protect the furnace structure, and enhance operational efficiency. In aluminum melting induction furnaces, linings are particularly important due to the unique challenges posed by molten aluminum, such as high vibration frequency and strong penetrability. Specialized linings are required to withstand these conditions and can typically be used for over 300 furnaces. Additionally, linings can be engineered in specific ways, such as cellular structures, to improve heat transfer. Overall, furnace linings play a vital role in ensuring the safe and efficient operation of furnaces across different industries.
Key Points Explained:
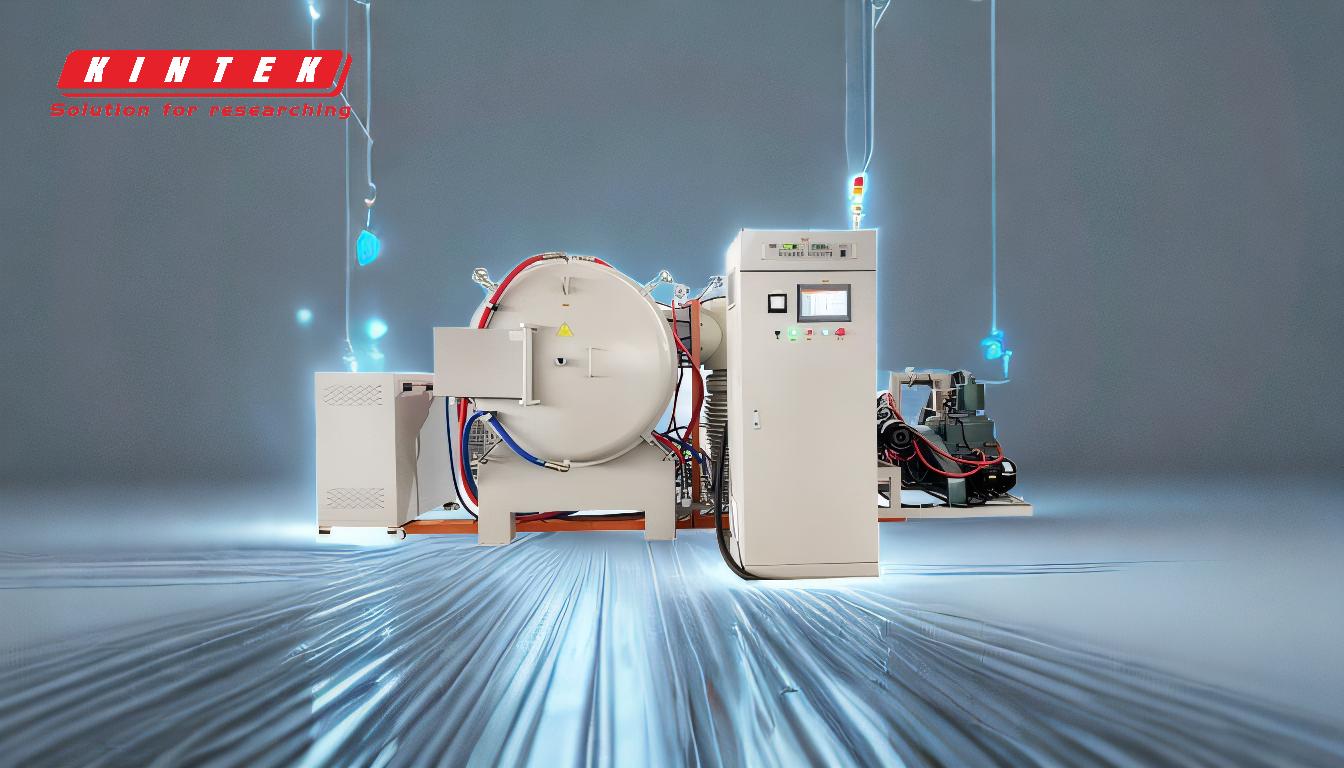
-
Containment of Molten Materials:
- The primary function of a furnace lining is to contain the molten metal within the furnace. This is crucial in processes like aluminum melting, where the molten metal must be kept separate from the furnace's structural components.
- In induction furnaces, the lining isolates the molten metal from the outer structure, such as the coil, preventing damage and ensuring the integrity of the furnace.
-
Protection of Furnace Structure:
- Furnace linings protect the furnace body from the extreme temperatures and corrosive nature of molten metals. This is particularly important in submerged arc furnaces used for smelting ferroalloys, where the lining shields the hearth and side walls from damage.
- By acting as a barrier, the lining prevents the molten metal from coming into direct contact with the furnace's structural elements, thereby extending the lifespan of the furnace.
-
Enhanced Heat Transfer:
- Some furnace linings are designed with special features, such as cellular structures, to improve heat transfer. This can lead to more efficient furnace operation by ensuring that heat is distributed evenly and effectively throughout the furnace.
- Improved heat transfer can also contribute to energy savings and better control over the melting process, which is critical in industries where precise temperature control is necessary.
-
Durability and Longevity:
- High-quality furnace linings are designed to withstand the harsh conditions within the furnace, including high temperatures and mechanical stress. In aluminum melting induction furnaces, good linings can be used for more than 300 furnaces, indicating their durability.
- The longevity of the lining reduces the need for frequent replacements, thereby minimizing downtime and maintenance costs.
-
Specialized Requirements for Different Furnaces:
- Different types of furnaces require specialized linings tailored to their specific operational conditions. For example, aluminum melting induction furnaces need linings that can handle high vibration frequencies and the strong penetrability of molten aluminum.
- The choice of lining material and design is critical to ensuring that the furnace operates efficiently and safely, highlighting the importance of selecting the right lining for each application.
In summary, furnace linings are indispensable in various industrial furnaces, providing essential functions such as containment, protection, and enhanced heat transfer. Their design and material composition are tailored to meet the specific demands of different furnace types, ensuring safe and efficient operation.
Summary Table:
Function | Description |
---|---|
Containment of Molten Materials | Prevents molten metal from damaging furnace components, ensuring operational integrity. |
Protection of Furnace Structure | Shields the furnace body from extreme temperatures and corrosive molten metals. |
Enhanced Heat Transfer | Features like cellular structures improve heat distribution and energy efficiency. |
Durability and Longevity | High-quality linings withstand harsh conditions, reducing downtime and maintenance. |
Specialized Requirements | Tailored designs for specific furnace types, such as aluminum melting induction furnaces. |
Optimize your furnace performance with the right linings—contact our experts today for tailored solutions!