Hot isostatic pressing (HIP) of castings is a manufacturing process that applies high temperature and uniform hydrostatic pressure to materials, typically metals or ceramics, to eliminate internal porosity, enhance density, and improve mechanical properties. This process is particularly beneficial for critical applications where material integrity and performance are paramount. HIP is widely used in industries such as aerospace, automotive, and medical devices to produce high-quality components with superior strength, durability, and reliability.
Key Points Explained:
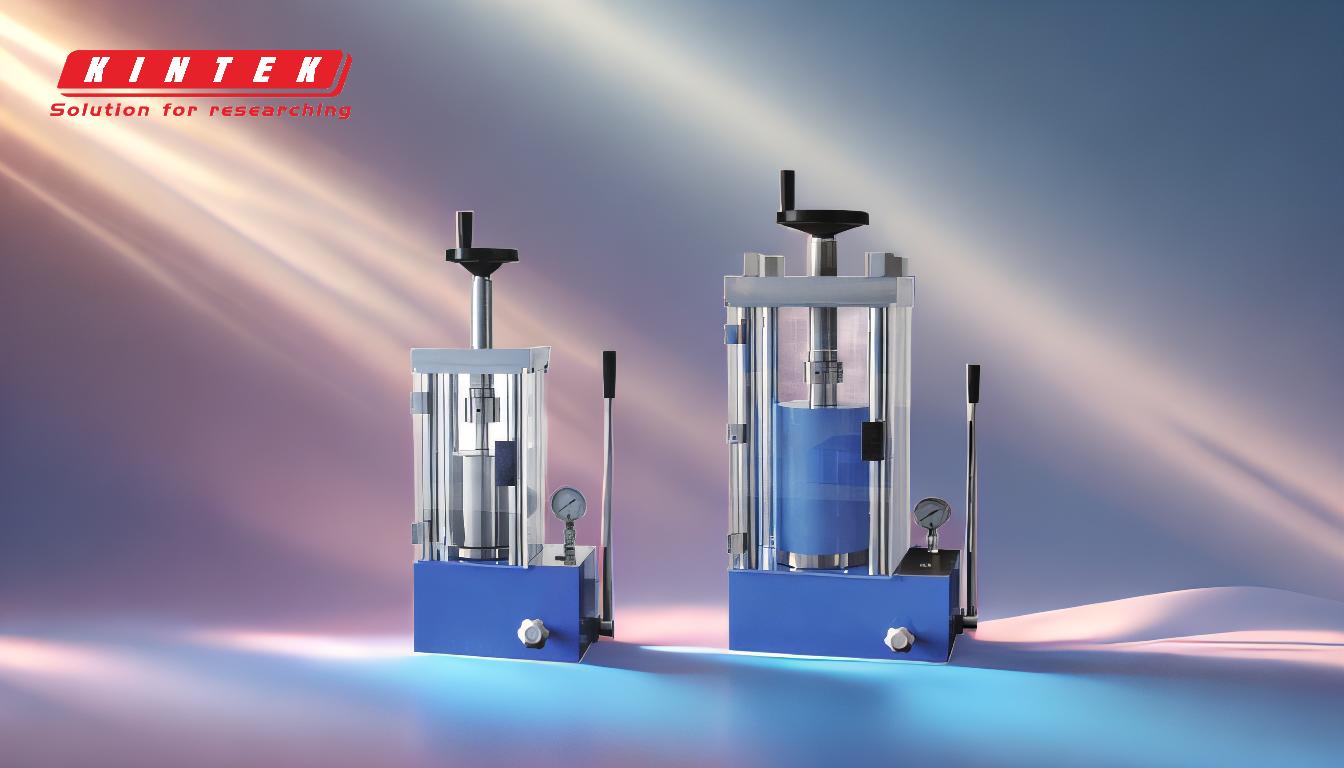
-
What is Hot Isostatic Pressing (HIP)?
- HIP is a process that combines high temperature (typically 900–2000°C) and uniform hydrostatic pressure (100–200 MPa) to densify materials and eliminate internal defects like porosity and microcracks.
- The process uses a gas, such as argon, as the pressure medium to ensure uniform pressure application from all directions.
- It is commonly applied to castings, powder metallurgy components, and additive manufacturing parts to improve their structural integrity and performance.
-
How Does HIP Work?
- The material or component is placed in a sealed container or flexible mold, which is then subjected to high temperature and pressure in a warm isostatic press.
- The pressure is transmitted uniformly through the gas medium, ensuring equal compaction in all directions.
- This process allows for the closure of internal voids and the formation of metallurgical bonds, resulting in a denser and more homogeneous material.
-
Benefits of HIP for Castings
- Elimination of Porosity: HIP effectively removes internal porosity and microcracks, which are common defects in castings. This leads to improved mechanical properties such as strength, fatigue resistance, and ductility.
- Enhanced Density: The process increases the density of the material, making it more suitable for high-stress applications.
- Improved Mechanical Properties: HIP enhances toughness, wear resistance, and thermal stability, extending the service life of components.
- Lightweight Designs: By improving material properties, HIP allows for the design of lighter components without compromising performance.
- Reduced Scrap and Losses: The ability to repair defects in castings reduces waste and improves production efficiency.
-
Applications of HIP in Industry
- Aerospace: HIP is used to produce high-performance components like turbine blades, engine parts, and structural components that require exceptional strength and reliability.
- Medical Devices: The process is employed to manufacture implants and prosthetics with superior biocompatibility and mechanical properties.
- Automotive: HIP is utilized for critical components such as engine parts, transmission systems, and lightweight structural elements.
- Energy: The technology is applied in the production of components for nuclear reactors, gas turbines, and renewable energy systems.
-
Comparison with Other Processes
- Unlike unidirectional pressing or sintering, HIP ensures uniform compaction in all directions, resulting in a more homogeneous material.
- HIP eliminates the need for lubricants and reduces geometric constraints, making it ideal for complex shapes and difficult-to-compact materials.
- The process is particularly advantageous for expensive materials like superalloys, titanium, and stainless steel, where material utilization and performance are critical.
-
Advantages Over Traditional Methods
- Uniform Pressure Application: HIP applies pressure uniformly in all directions, ensuring consistent material properties throughout the component.
- No Lubricants Required: The process eliminates the need for lubricants, reducing contamination and simplifying post-processing.
- High and Uniform Density: HIP achieves high and uniform density, which is difficult to attain with traditional pressing methods.
- Repair of Defects: The process can repair internal defects in castings, reducing scrap rates and improving production efficiency.
-
Challenges and Considerations
- Cost: HIP equipment and processing can be expensive, making it more suitable for high-value applications.
- Cycle Time: The process requires significant time for heating, pressurization, and cooling, which may affect production schedules.
- Material Compatibility: Not all materials are suitable for HIP, and careful selection is required to avoid adverse effects.
In conclusion, hot isostatic pressing is a transformative technology for enhancing the quality and performance of castings. By eliminating internal defects, improving density, and enhancing mechanical properties, HIP enables the production of high-performance components for demanding applications. Despite its challenges, the benefits of HIP make it an indispensable process in industries where material integrity and reliability are critical.
Summary Table:
Aspect | Details |
---|---|
Process | Combines high temperature (900–2000°C) and uniform hydrostatic pressure (100–200 MPa). |
Key Benefits | Eliminates porosity, enhances density, improves mechanical properties. |
Applications | Aerospace, medical devices, automotive, energy. |
Advantages Over Traditional Methods | Uniform pressure, no lubricants, high density, defect repair. |
Challenges | High cost, long cycle time, material compatibility. |
Learn how HIP can optimize your manufacturing process—contact our experts today!