The lining in an induction furnace is a critical component made of refractory materials, designed to contain molten metal, isolate it from the furnace's outer structure (such as the induction coil), and protect the furnace body during operation. It is typically made of acidic (e.g., silica) or basic (e.g., magnesia) compounds, depending on the application. For aluminum melting furnaces, specialized linings are required due to the high frequency, vibration, and penetrability of molten aluminum. The lining's quality directly impacts the furnace's efficiency, lifespan, and performance, with good linings lasting over 300 heat cycles. Proper installation and maintenance are essential to ensure optimal metallurgical performance and longevity.
Key Points Explained:
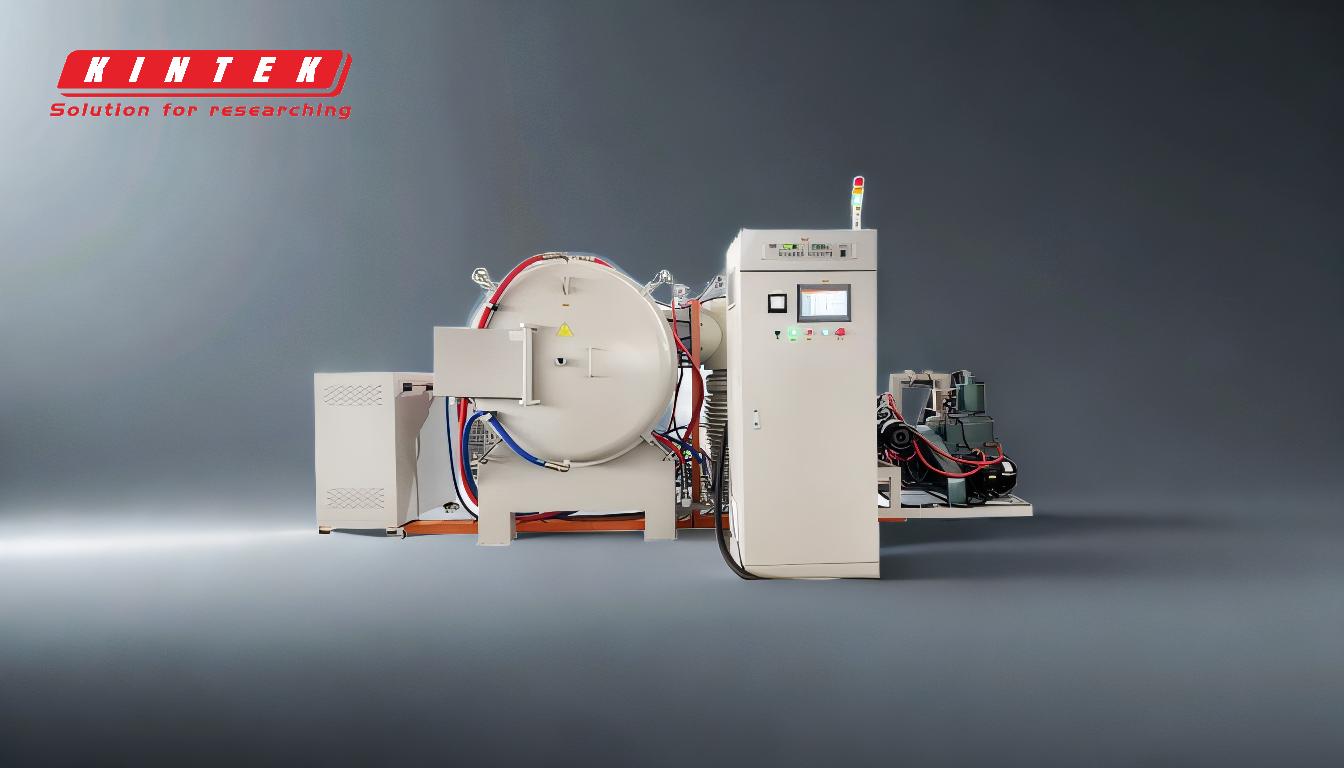
-
Definition and Purpose of Induction Furnace Lining:
- The lining is a refractory layer inside the induction furnace that serves three primary purposes:
- Containment: It holds the molten metal during melting or holding processes.
- Isolation: It prevents direct contact between the molten metal and the furnace's outer structure, such as the induction coil.
- Protection: It safeguards the furnace body from thermal and chemical damage during operation.
- The lining is the most critical component of an induction furnace, as its quality directly affects the furnace's performance and lifespan.
- The lining is a refractory layer inside the induction furnace that serves three primary purposes:
-
Materials Used in Lining:
- Refractory linings are typically made of either acidic or basic compounds:
- Acidic Linings: Commonly made of silica (SiO₂), suitable for melting non-ferrous metals like aluminum.
- Basic Linings: Often composed of magnesia (MgO), used for melting ferrous metals like steel.
- The choice of material depends on the type of metal being melted and the specific requirements of the application.
- Refractory linings are typically made of either acidic or basic compounds:
-
Special Considerations for Aluminum Melting Furnaces:
- Aluminum melting furnaces require specialized linings due to the unique properties of molten aluminum:
- High Frequency: The high operating frequency of the furnace generates intense vibrations.
- Molten Aluminum Penetrability: Aluminum has a strong tendency to penetrate and erode refractory materials.
- Vibration Frequency: The high vibration frequency of molten aluminum further stresses the lining.
- Specialized linings for aluminum furnaces are designed to withstand these challenges and typically last for more than 300 heat cycles.
- Aluminum melting furnaces require specialized linings due to the unique properties of molten aluminum:
-
Lining Installation and Quality:
- The lining installation process is crucial for ensuring the furnace's efficiency and longevity:
- Proper installation techniques are required to achieve a uniform and durable lining.
- The quality of the lining directly impacts the furnace's ability to contain molten metal, isolate it from the outer structure, and protect the furnace body.
- Poor installation can lead to premature lining failure, reduced furnace performance, and increased maintenance costs.
- The lining installation process is crucial for ensuring the furnace's efficiency and longevity:
-
Operational Life and Degradation:
- Refractory linings degrade over time due to thermal cycling, chemical reactions, and mechanical wear:
- The operational life of a lining, known as lining life, is measured by the number of heat cycles it can sustain before requiring repair or replacement.
- Regular maintenance and monitoring are essential to extend the lining's lifespan and ensure optimal metallurgical performance.
- Degradation can lead to issues such as metal leakage, reduced furnace efficiency, and increased energy consumption.
- Refractory linings degrade over time due to thermal cycling, chemical reactions, and mechanical wear:
-
Importance of Lining in Induction Furnace Operation:
- The lining is integral to the smooth operation of an induction furnace:
- It ensures the furnace can handle high temperatures and aggressive chemical environments.
- It contributes to energy efficiency by minimizing heat loss and protecting the furnace structure.
- A well-maintained lining reduces downtime and maintenance costs, improving overall productivity.
- The lining's performance directly impacts the quality of the molten metal and the efficiency of the production process.
- The lining is integral to the smooth operation of an induction furnace:
In summary, the lining in an induction furnace is a vital component that ensures the furnace's functionality, safety, and efficiency. Its material, installation, and maintenance are critical factors that determine the furnace's performance and lifespan.
Summary Table:
Key Aspect | Details |
---|---|
Purpose | Containment, isolation, and protection of molten metal and furnace structure. |
Materials | Acidic (e.g., silica) for non-ferrous metals; basic (e.g., magnesia) for ferrous metals. |
Aluminum Furnace Linings | Specialized linings withstand high frequency, vibration, and penetrability. |
Installation | Proper techniques ensure durability and performance. |
Lifespan | Good linings last over 300 heat cycles with regular maintenance. |
Importance | Enhances efficiency, reduces downtime, and improves metallurgical performance. |
Optimize your induction furnace's performance—contact our experts today for tailored solutions!