In a vacuum furnace, partial pressure refers to the controlled introduction of a specific gas into the vacuum chamber while maintaining a defined vacuum level. This technique is crucial for processes that require a controlled atmosphere to prevent oxidation, enhance heat transfer, or facilitate specific chemical reactions. The partial pressure system typically involves a mass flow controller and an adjustable gas outlet valve, managed by a programmable logic controller (PLC), to maintain precise gas flow and pressure levels. This method allows operators to balance the vacuum environment with the necessary gas atmosphere, ensuring optimal conditions for processes like sintering, brazing, or heat treatment.
Key Points Explained:
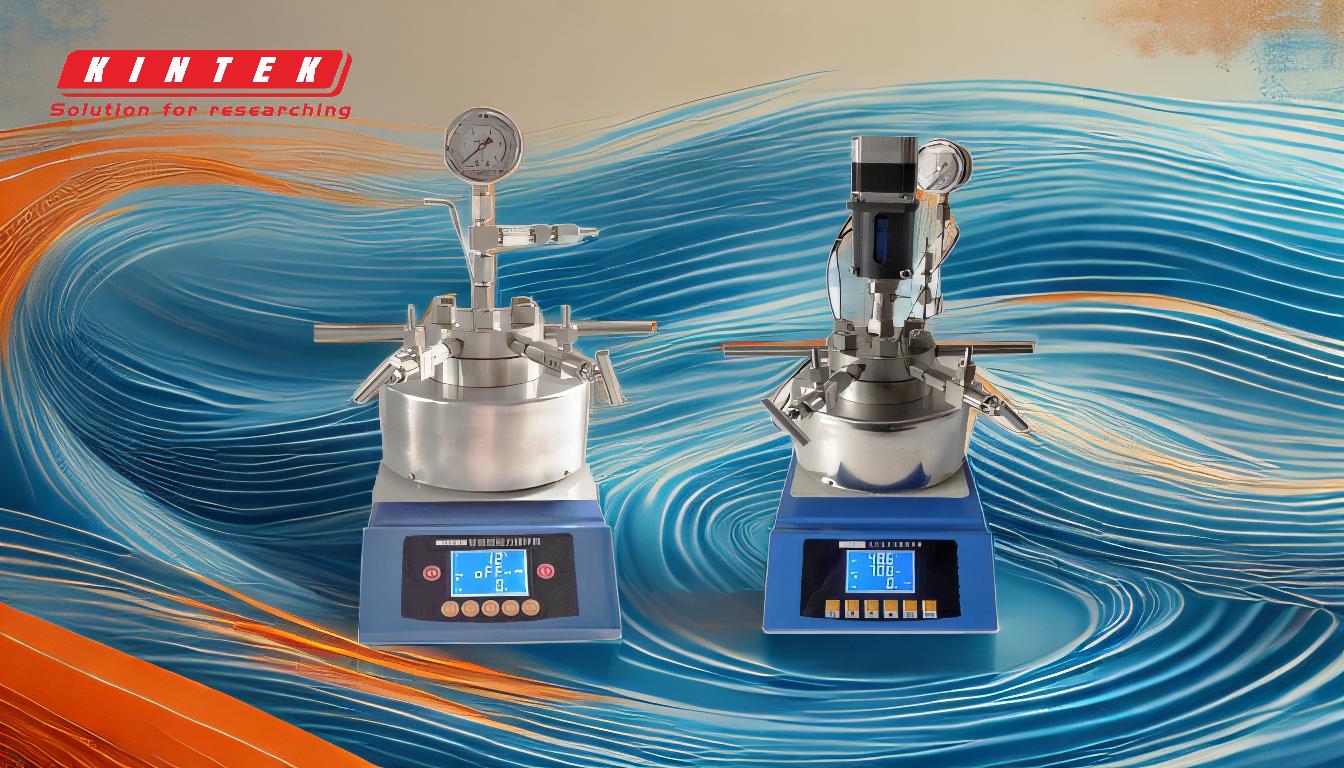
-
Definition of Partial Pressure in Vacuum Furnaces:
- Partial pressure in a vacuum furnace refers to the pressure exerted by a specific gas within the vacuum chamber while maintaining an overall vacuum environment. This is achieved by introducing a controlled flow of gas, such as hydrogen, argon, or nitrogen, into the chamber. The system ensures that the gas pressure remains within a defined range, typically between 10 and 1000 mbar, while the vacuum pump maintains the desired vacuum level.
-
Purpose of Partial Pressure:
- The primary purpose of using partial pressure is to create a controlled atmosphere that supports specific processing requirements. For example:
- Oxidation Prevention: In processes like sintering or brazing, partial pressure of inert gases like argon or nitrogen prevents oxidation of the workpiece.
- Enhanced Heat Transfer: Gases like hydrogen improve heat transfer efficiency, ensuring uniform heating of the workpiece.
- Chemical Reactions: Certain processes require specific gas atmospheres to facilitate chemical reactions, such as carburizing or nitriding.
- The primary purpose of using partial pressure is to create a controlled atmosphere that supports specific processing requirements. For example:
-
Components of a Partial Pressure System:
- A partial pressure system in a vacuum furnace typically includes:
- Mass Flow Controller: Regulates the flow rate of the gas into the chamber.
- Adjustable Gas Outlet Valve: Controls the release of gas to maintain the desired pressure.
- PLC (Programmable Logic Controller): Automates the control of gas flow and pressure, allowing precise adjustments by the operator.
- Pneumatic Valve: Works in conjunction with the vacuum pump to maintain the required vacuum pressure.
- A partial pressure system in a vacuum furnace typically includes:
-
Operation of Partial Pressure Systems:
- The operator sets the desired gas flow rate and pressure using the PLC. The mass flow controller ensures the correct amount of gas enters the chamber, while the adjustable gas outlet valve and pneumatic valve work together to maintain the specified vacuum pressure. This balance allows the furnace to operate under precise conditions, ensuring consistent results.
-
Applications of Partial Pressure in Vacuum Furnaces:
- Partial pressure is widely used in various industrial processes, including:
- Sintering: For refractory alloys like tungsten and molybdenum, partial pressure of hydrogen protects the material from oxidation while enabling high-temperature processing.
- Brazing: Controlled gas atmospheres prevent oxidation and improve the quality of brazed joints.
- Heat Treatment: Partial pressure systems are used in processes like annealing, tempering, and hardening to achieve specific material properties.
- Partial pressure is widely used in various industrial processes, including:
-
Advantages of Partial Pressure Systems:
- Precision: The ability to control gas flow and pressure with high accuracy ensures consistent and repeatable results.
- Flexibility: Operators can adjust the gas type, flow rate, and pressure to suit different materials and processes.
- Improved Process Quality: By preventing oxidation and enhancing heat transfer, partial pressure systems contribute to higher-quality outcomes.
-
Challenges and Considerations:
- Gas Selection: Choosing the right gas for the process is critical. For example, hydrogen is highly effective for heat transfer but requires careful handling due to its flammability.
- System Maintenance: Regular maintenance of the mass flow controller, valves, and vacuum pump is essential to ensure reliable operation.
- Safety: Proper safety measures must be in place when working with gases like hydrogen to prevent accidents.
By understanding and utilizing partial pressure in vacuum furnaces, operators can achieve precise control over the processing environment, leading to improved product quality and process efficiency.
Summary Table:
Aspect | Details |
---|---|
Definition | Pressure exerted by a specific gas in a vacuum chamber under controlled flow. |
Purpose | Prevent oxidation, enhance heat transfer, facilitate chemical reactions. |
Key Components | Mass flow controller, adjustable gas outlet valve, PLC, pneumatic valve. |
Applications | Sintering, brazing, heat treatment (annealing, tempering, hardening). |
Advantages | Precision, flexibility, improved process quality. |
Challenges | Gas selection, system maintenance, safety considerations. |
Optimize your vacuum furnace processes with expert guidance—contact us today!