Plasma sputtering Physical Vapor Deposition (PVD) is a thin-film deposition technique that uses plasma to generate high-energy ions, which bombard a target material, causing atoms to be ejected and deposited onto a substrate. This process is widely used in industries such as semiconductors, optics, and coatings due to its ability to produce high-quality, dense, and uniform thin films at relatively low temperatures. The process involves creating a plasma environment using a noble gas (typically argon) in a vacuum chamber, applying a voltage to ionize the gas, and directing the resulting ions to sputter target atoms onto a substrate.
Key Points Explained:
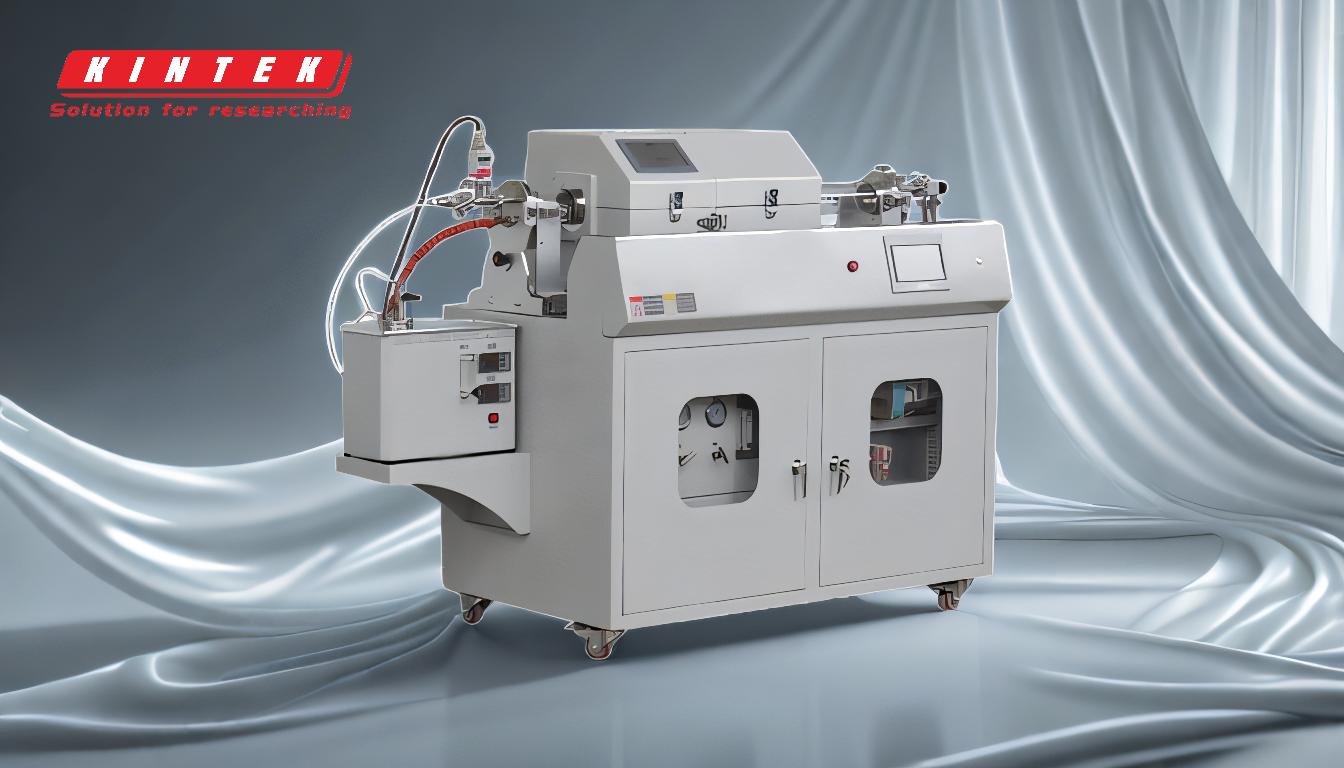
-
Definition of Plasma Sputtering PVD:
- Plasma sputtering PVD is a thin-film deposition technique where a plasma is used to generate high-energy ions that bombard a target material, causing atoms to be ejected and deposited onto a substrate.
- This process is a subset of Physical Vapor Deposition (PVD), which involves vaporizing a solid material and depositing it onto a surface in a vacuum environment.
-
Components of the Process:
- Plasma Generation: A noble gas, typically argon, is introduced into a vacuum chamber. A voltage (DC or RF) is applied to ionize the gas, creating a plasma composed of ions, electrons, and neutral atoms.
- Target Material: The material to be deposited (e.g., metals, ceramics) is placed as a target in the chamber. The target is bombarded by high-energy ions from the plasma.
- Substrate: The surface onto which the sputtered atoms are deposited. This can be a semiconductor wafer, optical lens, or any other material requiring a thin film.
-
Mechanism of Sputtering:
- Ion Bombardment: High-energy ions from the plasma collide with the target material, transferring their energy and causing atoms to be ejected from the target surface.
- Atom Ejection: The ejected atoms travel through the plasma and deposit onto the substrate, forming a thin film.
- Uniform Deposition: The process ensures a uniform and dense deposition of the target material onto the substrate, even at low temperatures (below 150 °C).
-
Advantages of Plasma Sputtering PVD:
- High-Quality Films: The process produces thin films with excellent uniformity, density, and adhesion.
- Low-Temperature Deposition: Sputtering can be performed at relatively low temperatures, making it suitable for temperature-sensitive substrates.
- Versatility: A wide range of materials, including metals, alloys, and ceramics, can be deposited using this technique.
- Reduced Residual Stress: The process minimizes residual stress in the deposited films, which is crucial for applications requiring mechanical stability.
-
Applications:
- Semiconductors: Used for depositing conductive and insulating layers in integrated circuits.
- Optics: Applied in the production of anti-reflective coatings, mirrors, and optical filters.
- Coatings: Utilized for wear-resistant, corrosion-resistant, and decorative coatings on various materials.
-
Process Parameters:
- Gas Pressure: The pressure of the noble gas in the chamber affects the plasma density and ion energy.
- Voltage and Power: The applied voltage (DC or RF) and power influence the energy of the ions and the rate of sputtering.
- Target-Substrate Distance: The distance between the target and substrate affects the uniformity and thickness of the deposited film.
-
Comparison with Other PVD Techniques:
- Evaporation: Unlike evaporation, which relies on heating the target material to produce vapor, sputtering uses ion bombardment, allowing for better control over film properties and compatibility with a wider range of materials.
- Chemical Vapor Deposition (CVD): While CVD involves chemical reactions to deposit films, sputtering PVD is a purely physical process, avoiding the need for reactive gases and high temperatures.
In summary, plasma sputtering PVD is a versatile and efficient method for depositing high-quality thin films, offering advantages in terms of film quality, low-temperature processing, and material compatibility. Its applications span across various industries, making it a critical technology in modern manufacturing and materials science.
Summary Table:
Aspect | Details |
---|---|
Definition | Thin-film deposition using plasma to sputter target atoms onto a substrate. |
Key Components | Plasma generation, target material, substrate. |
Advantages | High-quality, uniform films; low-temperature processing; material versatility. |
Applications | Semiconductors, optics, wear-resistant coatings. |
Process Parameters | Gas pressure, voltage/power, target-substrate distance. |
Discover how plasma sputtering PVD can enhance your manufacturing process—contact us today for expert guidance!