Press molding in ceramics is a manufacturing technique where granular or powdery ceramic materials are compressed under pressure to form a solid body with a specific geometric shape. This process typically uses hydraulic presses, which operate at room temperature, to apply the necessary pressure either isostatically or axially. The method is efficient and replaces traditional high-temperature kiln firing for producing items like tiles, bricks, and other ceramic products. The process involves several key steps, including material selection, preparation, and pressing, followed by finishing processes to achieve the desired final product.
Key Points Explained:
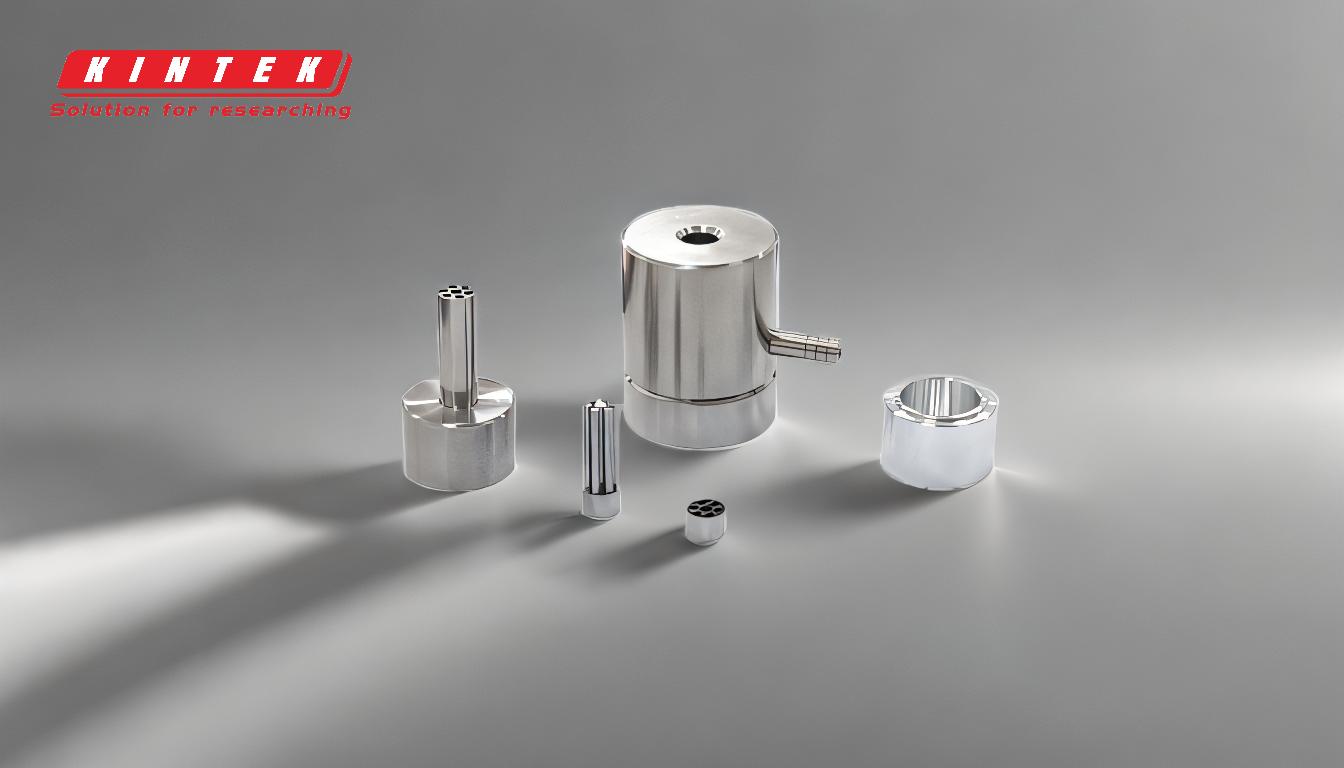
-
Definition of Press Molding in Ceramics:
- Press molding involves compressing granular or powdery ceramic materials under pressure to create a solid, geometrically defined shape.
- This technique is used to form various ceramic products such as tiles, bricks, and other objects.
-
Materials Used:
- The process typically uses specific types of ceramics, such as leucite-based or lithium disilicate-based ceramics.
- The choice of material depends on the desired properties and the final application of the ceramic product.
-
Process Steps:
- Material Selection: Choose the appropriate ceramic material based on the product requirements.
- Preparation: Follow manufacturer instructions for waxing, milling, spruing, and investing the ceramic material.
- Burnout: Allow sufficient burnout time to prepare the material for pressing.
- Pressing: Use a hydraulic press to apply the necessary pressure to form the ceramic into the desired shape.
- Finishing: After pressing, additional processes may be required to achieve the final product specifications.
-
Equipment Used:
- Hydraulic Presses: These are the primary equipment used in press molding. They can operate at room temperature and apply pressure either isostatically (uniform pressure from all directions) or axially (pressure applied from one direction).
- Advantages: Hydraulic presses are more efficient and faster than traditional kiln firing, reducing production time and energy consumption.
-
Advantages of Press Molding:
- Efficiency: The process is faster than traditional kiln firing, allowing for quicker production cycles.
- Energy Savings: Operating at room temperature reduces energy consumption compared to high-temperature kilns.
- Precision: The use of molds and hydraulic presses allows for high precision and consistency in the final product shape and dimensions.
-
Applications:
- Construction Materials: Press molding is widely used in the production of ceramic tiles, bricks, and other construction materials.
- Dental Ceramics: The technique is also used in the dental industry to create precise and durable ceramic restorations.
- Industrial Components: Various industrial components that require high precision and durability are also produced using press molding.
-
Comparison with Traditional Methods:
- Temperature: Unlike traditional kiln firing, which requires high temperatures, press molding operates at room temperature, making it more energy-efficient.
- Time: The pressing process is generally faster than kiln firing, leading to shorter production times.
- Quality: Press molding can produce high-quality, consistent products with fewer defects compared to some traditional methods.
By understanding these key points, one can appreciate the efficiency, precision, and versatility of press molding in ceramics, making it a valuable technique in both industrial and artistic applications.
Summary Table:
Aspect | Details |
---|---|
Definition | Compressing granular/powdery ceramics under pressure to form solid shapes. |
Materials Used | Leucite-based, lithium disilicate-based ceramics, etc. |
Process Steps | Material selection, preparation, burnout, pressing, finishing. |
Equipment | Hydraulic presses (isostatic/axial pressure at room temperature). |
Advantages | Faster production, energy savings, high precision, and consistency. |
Applications | Tiles, bricks, dental ceramics, industrial components. |
Comparison | More efficient and precise than traditional kiln firing. |
Ready to explore press molding for your ceramic production? Contact us today to learn more!