Pressureless sintered silicon carbide (SiC) is a high-performance ceramic material manufactured by sintering high-purity, ultra-fine silicon carbide powder with minimal sintering aids at high temperatures (1950–2100°C) under atmospheric pressure in inert gas or vacuum environments. This process yields a material with high density, uniform microstructure, and exceptional mechanical, thermal, and chemical properties. It is widely used in industrial applications such as wear-resistant and corrosion-resistant components, seals, and bearings, as well as in high-tech fields like semiconductors, nuclear energy, and aerospace. Its advantages include low production costs, the ability to produce complex shapes, and suitability for mass production.
Key Points Explained:
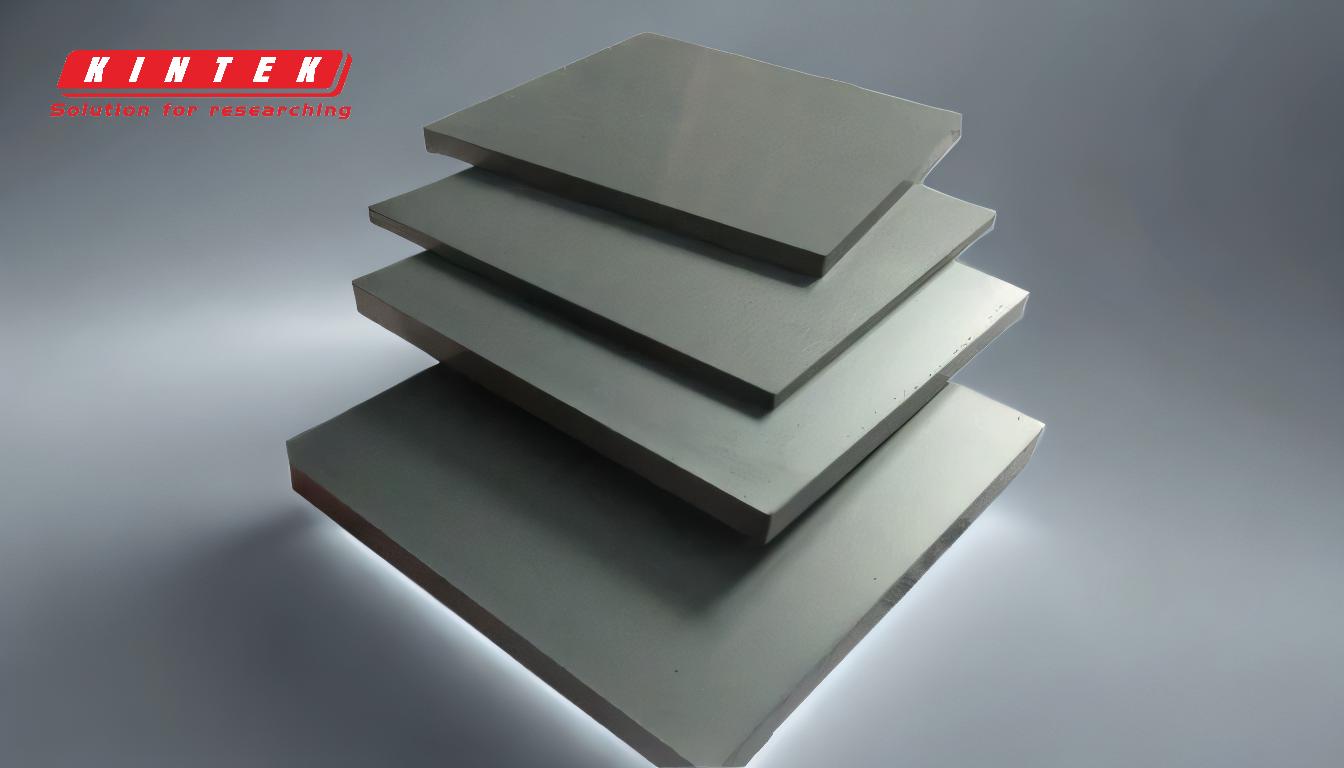
-
Definition and Manufacturing Process
- Pressureless sintered silicon carbide is a ceramic material made from high-purity, ultra-fine silicon carbide powder.
- A small amount of sintering aids is added to facilitate the process.
- Sintering occurs at high temperatures (1950–2100°C) in an inert gas or vacuum atmosphere at atmospheric pressure.
- The process avoids the need for external pressure, making it cost-effective and suitable for mass production.
-
Key Properties
- High Density and Uniform Microstructure: Ensures consistent performance and reliability.
- Mechanical Strength: Maintains high strength at temperatures up to 1400°C, with no strength loss even at 1600°C.
- Wear and Corrosion Resistance: Ideal for harsh industrial environments.
- Thermal Properties: High thermal conductivity and low thermal expansion coefficient make it resistant to thermal shock.
- Chemical Inertness: Resistant to chemical corrosion, making it suitable for corrosive environments.
-
Advantages of Pressureless Sintering
- Cost-Effective: No need for high-pressure equipment reduces production costs.
- Shape and Size Flexibility: Can produce complex shapes and large components without restrictions.
- Mass Production Feasibility: Suitable for large-scale manufacturing due to its simplicity and efficiency.
-
Applications
- Industrial Use: Sealing rings, sliding bearings, and wear-resistant components in machinery.
- High-Tech Fields: Semiconductors, nuclear energy, defense, and aerospace due to its superior thermal and mechanical properties.
- High-Temperature Applications: Kiln furniture, heat exchangers, and combustion nozzles due to its thermal shock resistance and high-temperature stability.
-
Comparison with Other SiC Types
- Recrystallized SiC: Has high porosity and thermal conductivity but lacks the density and mechanical strength of pressureless sintered SiC.
- Sintered SiC with Non-Oxide Additives: Offers high density and strength but may involve more complex processing.
- Pressureless sintered SiC strikes a balance between cost, performance, and ease of production.
-
Material Versatility
- Combines the hardness of ceramics with relatively high electrical conductivity, making it suitable for specialized applications.
- Can be manufactured using conventional ceramic forming processes like pressing or extrusion, followed by sintering.
-
Future Prospects
- Increasing demand in high-tech industries due to its exceptional properties.
- Potential for further optimization in sintering processes to enhance performance and reduce costs.
- Expanding applications in renewable energy, advanced manufacturing, and space exploration.
In summary, pressureless sintered silicon carbide is a versatile, high-performance ceramic material with a wide range of industrial and high-tech applications. Its unique combination of properties, cost-effectiveness, and manufacturing flexibility makes it a preferred choice for demanding environments and advanced technologies.
Summary Table:
Aspect | Details |
---|---|
Manufacturing Process | High-purity SiC powder sintered at 1950–2100°C in inert gas or vacuum. |
Key Properties | High density, wear resistance, thermal shock resistance, chemical inertness. |
Advantages | Cost-effective, shape flexibility, mass production feasibility. |
Applications | Industrial seals, bearings, semiconductors, aerospace, and high-temperature uses. |
Comparison with Others | Balances cost, performance, and ease of production better than other SiC types. |
Learn more about how pressureless sintered silicon carbide can benefit your applications—contact us today!