Sintering of clay is a critical process in ceramic manufacturing where powdered clay particles are compacted and transformed into a dense, solid mass by applying heat and pressure below the material's melting point. This process involves the diffusion of atoms across particle boundaries, leading to the fusion of particles, reduction of porosity, and increased density. Sintering is essential for creating durable and strong ceramic products, such as pottery and porcelain, as it enhances the material's mechanical properties and structural integrity.
Key Points Explained:
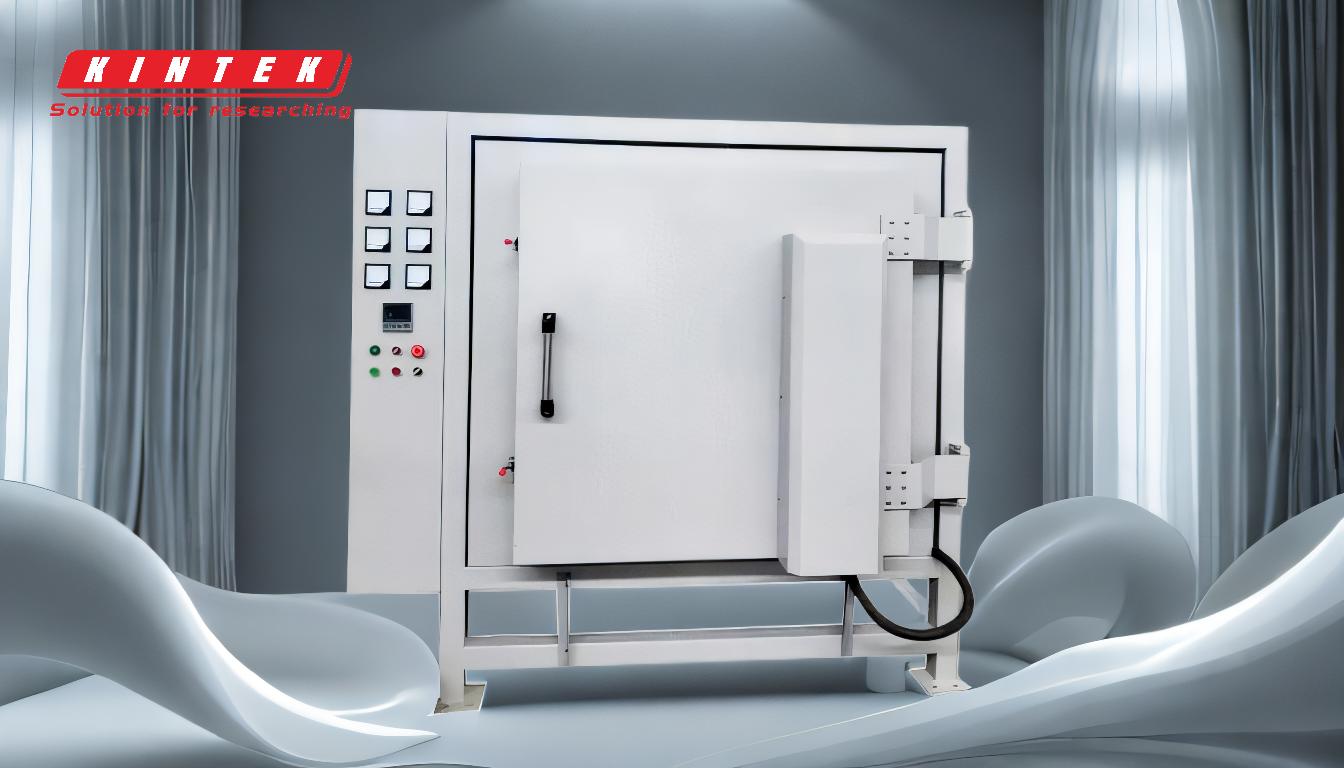
-
Definition of Sintering
- Sintering is a process that compacts and forms a solid mass of material by applying heat or pressure without melting it to the point of liquefaction.
- It involves the diffusion of atoms across particle boundaries, fusing them together to create a dense, solid piece.
- This process is particularly useful for materials with high melting points, such as ceramics and metals like tungsten and molybdenum.
-
Stages of Sintering
-
Initial Stage (Binder Removal):
- The green body (unfired clay) is heated slowly to evaporate any remaining organic binders.
- This occurs at lower temperatures and prepares the material for the next stage.
-
Intermediate Stage (Diffusion Bonding):
- At higher temperatures, powder particles begin to diffusion bond at points of contact.
- This increases the contact area between particles and pulls their centers closer, reducing porosity.
-
Final Stage (Densification):
- The material undergoes further heating to a temperature high enough to fuse particles completely.
- This results in the elimination of small pores and the formation of a dense, solid part.
-
Initial Stage (Binder Removal):
-
Role of Heat and Pressure
- Heat and pressure are applied to force atoms into tighter bonds, resulting in a harder, stronger, and more durable mass.
- The temperature is carefully controlled to remain below the material's melting point, ensuring that the material does not liquefy.
- Pressure helps in compacting the particles, reducing gaps, and enhancing the material's density.
-
Applications in Ceramic Manufacturing
- Sintering is widely used in the production of pottery, porcelain, and other ceramic products.
- It transforms powdered clay into a dense, durable ceramic body with improved mechanical properties.
- The process is essential for creating items like tiles, tableware, and industrial ceramics.
-
Benefits of Sintering
- Increased Density: Sintering reduces porosity, making the material denser and stronger.
- Enhanced Mechanical Properties: The process improves hardness, strength, and durability of the final product.
- Shrinkage Control: The part typically shrinks by about 20% during sintering, which is accounted for in the design phase.
- Cost-Effective: Sintering allows for the production of complex shapes with minimal material waste.
-
Process Parameters
- Temperature: Must be high enough to facilitate atomic diffusion but below the melting point of the material.
- Atmosphere: Controlled environments (e.g., inert gases) are often used to prevent oxidation or contamination.
- Time: The duration of heating is critical to ensure complete densification without over-sintering.
-
Material Transformation
- During sintering, powder particles undergo material migration and grain boundary movement.
- Over time, the ceramic material becomes densified, forming a porcelain body with a certain strength.
- The process transforms a loose, powdery material into a cohesive, solid structure.
By understanding the sintering process, manufacturers can optimize the production of ceramic materials, ensuring high-quality, durable products that meet specific application requirements.
Summary Table:
Key Aspect | Details |
---|---|
Definition | Compacts powdered clay into a solid mass using heat and pressure. |
Stages | 1. Binder Removal 2. Diffusion Bonding 3. Densification |
Role of Heat & Pressure | Enhances density, strength, and durability without liquefaction. |
Applications | Pottery, porcelain, tiles, tableware, and industrial ceramics. |
Benefits | Increased density, improved mechanical properties, and cost-effectiveness. |
Process Parameters | Controlled temperature, atmosphere, and time for optimal results. |
Ready to optimize your ceramic manufacturing process? Contact us today to learn more!