Sintering is a manufacturing process that involves compacting and fusing powdered materials into a solid mass using heat and pressure, without reaching the material's melting point. This process reduces porosity and enhances material properties, making it ideal for creating complex shapes and improving material strength. Sintering is widely used in industries such as ceramics, metals, and plastics, and is essential in applications like 3D printing and the production of custom metal forms. For example, sintering is used to create ceramic components, metal parts, and even diamond tools. The process relies on atomic diffusion, where particles bond together under controlled thermal conditions, resulting in a durable and cohesive final product.
Key Points Explained:
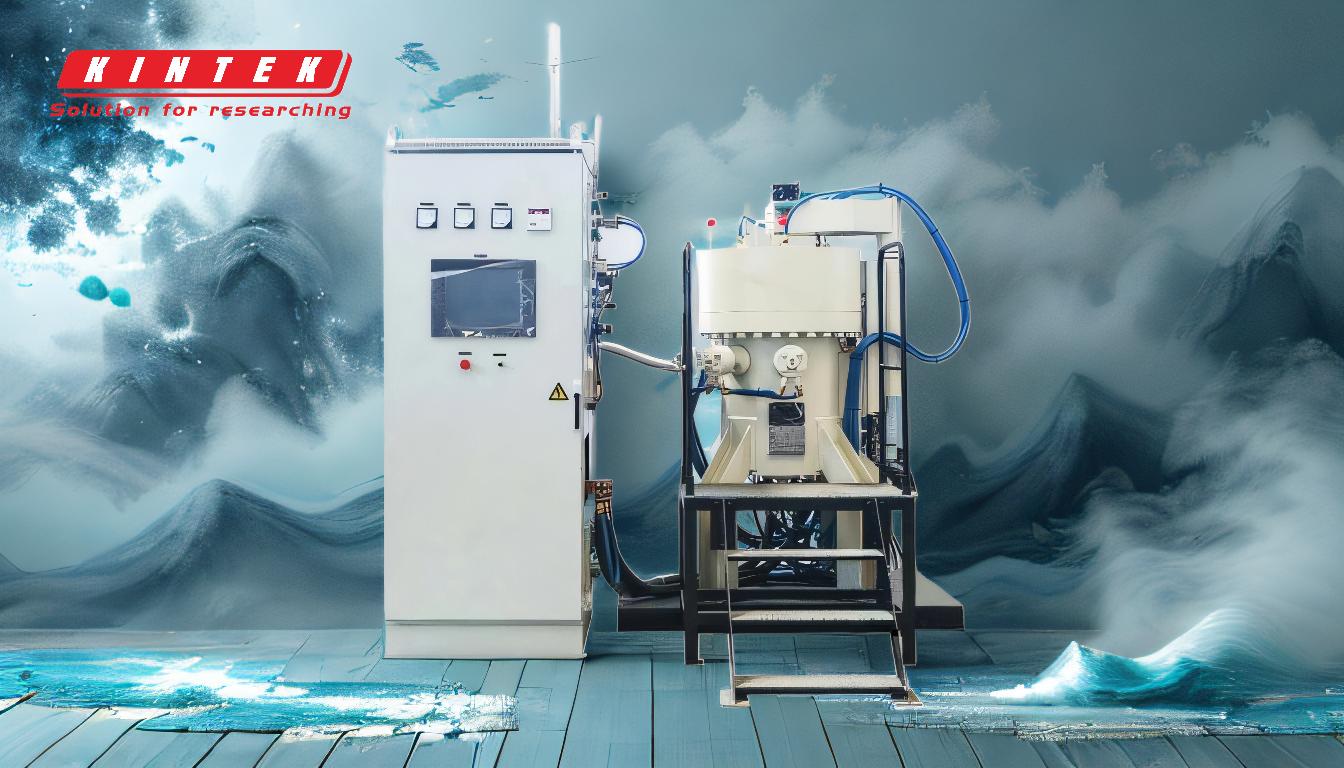
-
Definition of Sintering:
- Sintering is a process that compacts and fuses powdered materials into a solid mass using heat and pressure, without melting the material. This technique is used to reduce porosity and improve the mechanical properties of the final product.
-
Stages of Sintering:
- Compaction: The powdered material is compressed into a specific shape, often using a temporary binder to hold the particles together.
- Heating: The compacted material is heated to a temperature below its melting point, allowing atoms to diffuse across particle boundaries and fuse together, forming a solid piece.
-
Mechanism of Sintering:
- Sintering works through atomic diffusion, where atoms move across particle boundaries under the influence of heat and pressure. This process bonds the particles together, creating a cohesive and durable material.
-
Applications of Sintering:
- Metals: Used for metals with high melting points, such as tungsten and titanium, to create custom shapes and reduce porosity.
- Ceramics: Commonly used to produce ceramic components like insulators, cutting tools, and dental implants.
- 3D Printing: Sintering is integral to additive manufacturing, where metal or ceramic powders are fused layer by layer to create complex 3D structures.
- Diamond Tools: Sintering is used to bond diamond particles to metal substrates, creating durable cutting tools like diamond saw blades.
-
Example of Sintering:
- A practical example of sintering is the production of ceramic inserts for cutting tools. Powders of ceramic materials are compacted into the desired shape and then heated in a sintering furnace to fuse the particles, resulting in a strong and wear-resistant component.
-
Advantages of Sintering:
- Energy Efficiency: Sintering operates at temperatures below the material's melting point, reducing energy consumption.
- Material Properties: The process enhances material strength, density, and wear resistance.
- Complex Shapes: Sintering allows for the creation of intricate and customized shapes that are difficult to achieve with traditional manufacturing methods.
-
Natural vs. Industrial Sintering:
- Natural Sintering: Occurs in nature, such as the compaction of snowfall into glaciers or the formation of hard snowballs.
- Industrial Sintering: A controlled process used in manufacturing to produce high-performance materials and components.
-
Role of Sintering Furnaces:
- Sintering furnaces are essential for the sintering process, providing the controlled heat and environment needed to fuse particles. They are used in various industries, including ceramics, metallurgy, and tool manufacturing.
By understanding the principles and applications of sintering, manufacturers can produce high-quality, durable materials and components tailored to specific industrial needs. The use of advanced equipment like sintering furnaces ensures precision and efficiency in the sintering process.
Summary Table:
Aspect | Details |
---|---|
Definition | Compacting and fusing powdered materials using heat and pressure. |
Stages | Compaction and heating below the material's melting point. |
Mechanism | Atomic diffusion bonds particles under controlled thermal conditions. |
Applications | Metals, ceramics, 3D printing, and diamond tools. |
Example | Production of ceramic inserts for cutting tools. |
Advantages | Energy efficiency, enhanced material properties, and complex shape creation. |
Ready to explore sintering solutions for your manufacturing needs? Contact us today to learn more!