Sputtering deposition is a physical vapor deposition (PVD) technique used to create thin films on substrates by ejecting atoms from a solid target material using high-energy ion bombardment. These ejected atoms then deposit onto a substrate in a vacuum chamber, forming a thin, uniform layer. This process is widely utilized in industries such as semiconductors, optics, and manufacturing, where precise and durable coatings are required. Applications range from creating reflective coatings on glass and polymers to developing advanced materials for electronics, magnetic storage, and solar cells. Sputtering deposition is valued for its ability to produce high-quality, uniform films with excellent adhesion and control over film composition and thickness.
Key Points Explained:
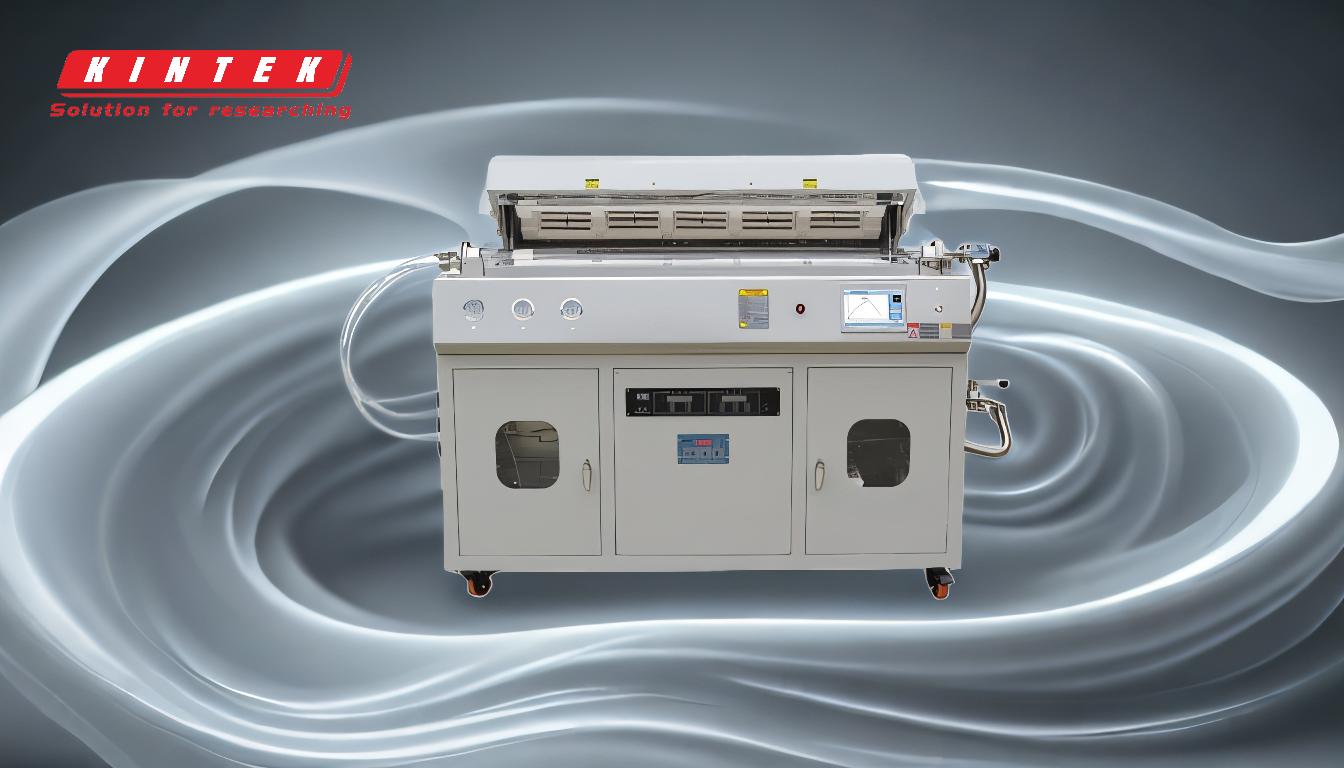
-
Definition and Process of Sputtering Deposition
- Sputtering deposition is a PVD technique where high-energy ions bombard a solid target material, ejecting atoms from its surface.
- These ejected atoms travel through a vacuum chamber and deposit onto a substrate, forming a thin film.
- The process is conducted in a vacuum to minimize contamination and ensure precise control over film properties.
-
Applications of Sputtering Deposition
- Semiconductor Industry: Used for depositing thin films in integrated circuits, contact metals in thin-film transistors, and other microelectronic components.
- Optical Coatings: Applied to create anti-reflective coatings on glass, reflective coatings on polymers, and optical waveguides.
- Magnetic and Data Storage: Essential for producing magnetic films in computer hard disks and coatings for CDs and DVDs.
- Solar Energy: Used in the fabrication of photovoltaic solar cells to create efficient and durable layers.
- Tool Coatings: Enhances durability and wear resistance of cutting tools using materials like titanium nitride.
- Decorative and Functional Coatings: Applied to architectural glass, polymers, and other materials for aesthetic and functional purposes.
-
Advantages of Sputtering Deposition
- High-Quality Films: Produces uniform, dense, and well-adhered thin films with precise control over thickness and composition.
- Versatility: Can deposit a wide range of materials, including metals, alloys, oxides, and nitrides.
- Scalability: Suitable for both small-scale research and large-scale industrial production.
- Clean Process: Conducted in a vacuum, reducing contamination and ensuring high-purity coatings.
-
Mechanism of Sputtering Deposition
- High-energy ions (typically from an inert gas like argon) are accelerated toward the target material.
- These ions collide with the target, transferring energy and ejecting atoms from its surface.
- The ejected atoms travel ballistically through the vacuum chamber and deposit onto the substrate, forming a thin film layer by layer.
-
Industries and Technologies Benefiting from Sputtering Deposition
- Electronics and Semiconductors: Enables the miniaturization and performance enhancement of devices.
- Optics and Photonics: Improves the efficiency and functionality of optical components.
- Energy: Supports the development of efficient solar cells and energy-saving coatings.
- Manufacturing: Extends the lifespan and performance of tools and components through durable coatings.
-
Future Trends and Innovations
- Development of advanced materials, such as 2D materials and nanostructured films, for next-generation technologies.
- Integration of sputtering deposition with other techniques, like atomic layer deposition (ALD), for hybrid film fabrication.
- Increased use in renewable energy applications, such as perovskite solar cells and energy-efficient coatings.
By understanding the principles, applications, and advantages of sputtering deposition, purchasers and engineers can make informed decisions about its use in various industries, ensuring the production of high-quality, durable, and functional coatings.
Summary Table:
Aspect | Details |
---|---|
Definition | PVD technique using high-energy ions to eject atoms from a target material. |
Applications | Semiconductors, optics, magnetic storage, solar cells, tool coatings. |
Advantages | High-quality, uniform films; versatile; scalable; clean process. |
Key Industries | Electronics, optics, energy, manufacturing. |
Future Trends | Advanced materials, hybrid techniques, renewable energy applications. |
Discover how sputtering deposition can enhance your projects—contact our experts today!