The annealing process is a critical heat treatment technique widely used in metallurgy and materials science to enhance the properties of metals and alloys. Its primary purpose is to soften materials, relieve internal stresses, and improve ductility, making them more suitable for further processing such as machining, cold working, or additional heat treatments. Annealing achieves these effects by heating the material to its recrystallization temperature, holding it at that temperature for a specific duration, and then cooling it down slowly. This process helps restore the material to a more workable state, reduces hardness, and increases toughness, making it ideal for applications ranging from manufacturing to structural engineering. Below, the key aspects and applications of annealing are explained in detail.
Key Points Explained:
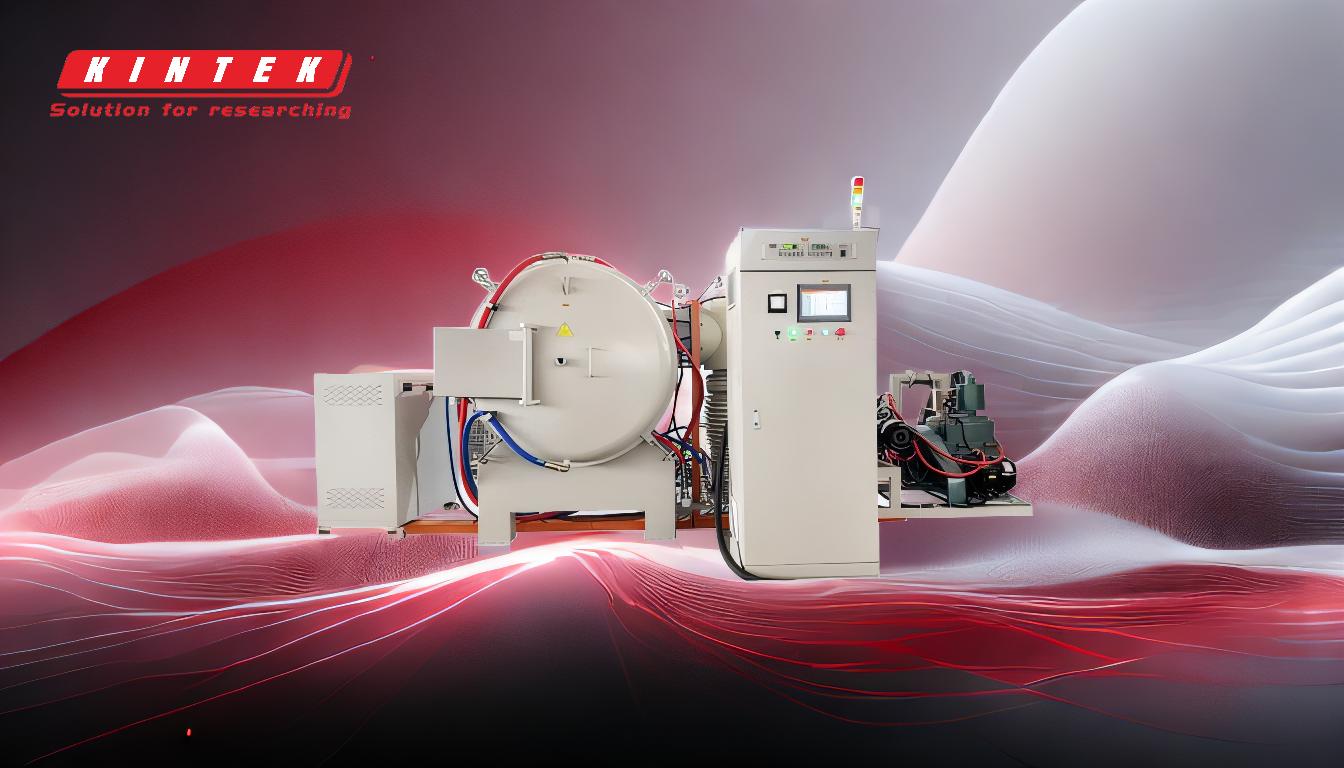
-
Softening Metals for Cold Working
- Annealing is primarily used to soften metals, making them easier to shape and form through cold working processes like bending, drawing, or stamping.
- By heating the material to its recrystallization temperature, the internal crystal structure is rearranged, reducing dislocations and making the material more ductile.
- This is particularly useful in industries where metals undergo extensive deformation, such as automotive manufacturing or metal fabrication.
-
Relieving Internal Stresses
- During processes like welding, machining, or cold working, internal stresses can build up within the material, leading to potential failure or deformation.
- Annealing helps relieve these stresses by allowing the material to relax and reorganize its microstructure, resulting in a more uniform and stable internal structure.
- This is crucial for components that require high precision and reliability, such as aerospace parts or structural beams.
-
Reversing Work Hardening
- Work hardening, or strain hardening, occurs when a metal is deformed through cold working, making it harder but more brittle.
- Annealing reverses this effect by restoring the material's ductility, enabling further processing without the risk of cracking or fracturing.
- This is essential in industries like wire drawing or sheet metal forming, where repeated deformation is required.
-
Improving Machinability
- Hardened materials are difficult to machine due to their high resistance to cutting tools.
- Annealing reduces hardness and increases ductility, making the material easier to cut, drill, or shape with machining tools.
- This is particularly beneficial in manufacturing industries where precision machining is required for components like gears, shafts, or engine parts.
-
Enhancing Electrical and Physical Properties
- In some cases, annealing is used to improve the electrical conductivity or other physical properties of metals.
- By refining the grain structure and reducing defects, annealing can enhance the material's performance in electrical applications, such as wiring or electronic components.
-
Preparing Materials for Further Heat Treatment
- Annealing is often used as a preparatory step before other heat treatment processes, such as quenching or tempering.
- It ensures that the material has a uniform microstructure and is free of internal stresses, which is critical for achieving consistent results in subsequent treatments.
-
Applications in Specific Industries
- Automotive Industry: Annealing is used to produce components like gears, springs, and chassis parts that require high ductility and toughness.
- Aerospace Industry: Critical components such as turbine blades and structural frames are annealed to ensure they can withstand extreme stress and temperature conditions.
- Electronics Industry: Annealing improves the electrical properties of metals used in wiring, connectors, and semiconductors.
- Construction Industry: Structural steel and reinforcement bars are annealed to enhance their workability and durability.
-
Types of Annealing Processes
- Full Annealing: Involves heating the material above its recrystallization temperature and cooling it slowly to achieve maximum softness and ductility.
- Process Annealing: Used to soften metals during intermediate stages of manufacturing, particularly in wire and sheet metal production.
- Stress Relief Annealing: Focuses on reducing internal stresses without significantly altering the material's hardness or microstructure.
- Spheroidizing Annealing: Used to produce a spherical microstructure in high-carbon steels, improving their machinability.
In summary, the annealing process is a versatile and essential technique in materials science, offering numerous benefits such as stress relief, improved ductility, and enhanced machinability. Its applications span a wide range of industries, making it indispensable for producing high-quality, durable, and workable materials.
Summary Table:
Key Aspect | Description |
---|---|
Softening Metals | Makes metals easier to shape and form through cold working processes. |
Relieving Internal Stresses | Reduces stress from welding, machining, or cold working for stable structures. |
Reversing Work Hardening | Restores ductility, enabling further processing without cracking. |
Improving Machinability | Reduces hardness, making materials easier to cut, drill, or shape. |
Enhancing Properties | Improves electrical conductivity and physical performance in metals. |
Preparing for Heat Treatment | Ensures uniform microstructure for consistent results in subsequent processes. |
Applications | Used in automotive, aerospace, electronics, and construction industries. |
Types of Annealing | Full, process, stress relief, and spheroidizing annealing for specific needs. |
Discover how annealing can optimize your materials—contact our experts today!