The arc melting technique is a specialized electrothermal metallurgical method used to melt metals by generating an electric arc between an electrode and the material to be melted. This process relies on the high temperatures produced by the electric arc, which is a self-sustaining discharge phenomenon. The technique is commonly implemented in arc melting furnaces, which convert standard voltage (220V or 380V) into low voltage and high current to create the arc. This method is particularly useful for melting metals like scrap steel without altering their chemical properties, making it a valuable tool in metallurgy and material processing.
Key Points Explained:
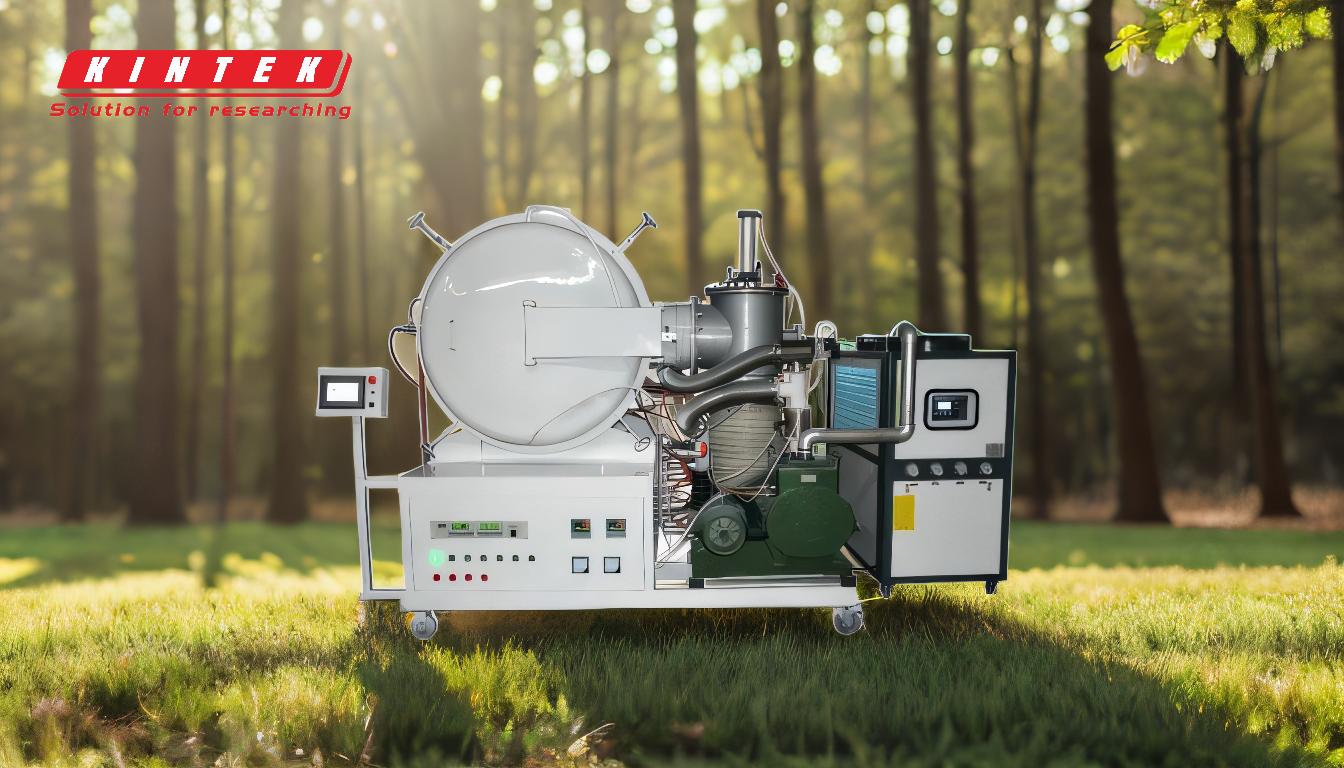
-
Definition and Purpose of Arc Melting:
- Arc melting is an electrothermal metallurgical process that uses electric energy to generate an electric arc. This arc produces extremely high temperatures, which are used to melt metals.
- The primary purpose of arc melting is to liquefy metals, such as scrap steel, for recycling or further processing, without changing their chemical composition.
-
Components of an Arc Melting Furnace:
- The main component of an arc melting furnace is the electric welder, which converts standard voltage (220V or 380V) into low voltage and high current.
- The furnace also includes electrodes and a chamber where the material to be melted is placed. The electric arc is generated between the electrodes or between an electrode and the material.
-
Mechanism of Arc Generation:
- The electric arc is triggered by an instantaneous short circuit between the positive and negative poles of the electrode system.
- Once initiated, the arc becomes a self-sustaining discharge phenomenon, meaning it continues to burn stably without external intervention, as long as the electrical supply is maintained.
-
High-Temperature Plasma and Its Role:
- The electric arc creates a thermal plasma, which is a high-energy state of matter with temperatures high enough to melt metals.
- This plasma is the primary source of heat in the arc melting process, enabling the efficient melting of materials.
-
Applications of Arc Melting:
- Arc melting is widely used in industries that require the melting of metals, such as steel recycling, foundries, and metallurgical research.
- It is particularly advantageous for processing scrap metals, as it allows for the melting of materials without altering their chemical properties.
-
Advantages of Arc Melting:
- High Efficiency: The electric arc generates extremely high temperatures, allowing for rapid melting of metals.
- Chemical Integrity: The process does not alter the chemical composition of the metals being melted, making it ideal for recycling and reprocessing.
- Versatility: Arc melting can be used for a wide range of metals and alloys, making it a versatile tool in metallurgy.
-
Challenges and Considerations:
- Energy Consumption: Arc melting requires significant electrical energy, which can be costly.
- Equipment Maintenance: The high temperatures and intense energy involved can lead to wear and tear on the furnace components, requiring regular maintenance.
- Safety Precautions: Due to the high temperatures and electrical hazards, proper safety measures must be in place to protect operators and equipment.
-
Comparison with Other Melting Techniques:
- Unlike induction melting, which uses electromagnetic fields to generate heat, arc melting relies on direct electrical discharge.
- Arc melting is often preferred for its ability to handle larger volumes of material and its suitability for melting scrap metals.
By understanding these key points, one can appreciate the arc melting technique's role in modern metallurgy and its importance in processes like metal recycling and material processing.
Summary Table:
Key Aspect | Details |
---|---|
Definition | Electrothermal process using an electric arc to melt metals. |
Purpose | Melting metals like scrap steel for recycling without chemical alteration. |
Main Components | Electric welder, electrodes, and a melting chamber. |
Mechanism | Self-sustaining electric arc generates high-temperature plasma. |
Applications | Steel recycling, foundries, and metallurgical research. |
Advantages | High efficiency, chemical integrity, and versatility. |
Challenges | High energy consumption, equipment maintenance, and safety precautions. |
Comparison | Preferred over induction melting for larger volumes and scrap metal use. |
Ready to optimize your metal melting process? Contact our experts today to learn more about arc melting solutions!