An induction furnace operates on the principle of electromagnetic induction and the Joule effect, enabling non-contact heating of conductive materials. It functions similarly to a transformer, where an alternating current (AC) in the primary coil (induction coil) generates a magnetic field. This field induces eddy currents in the metal charge (secondary circuit), which heats up due to electrical resistance (Joule effect). The heat generated within the metal itself allows for precise and rapid melting, making induction furnaces ideal for creating alloys with exact compositions. The primary coil is cooled by water circulation, and the process occurs at high frequencies (500 Hz to 1000 Hz), ensuring efficient energy transfer and minimal heat loss.
Key Points Explained:
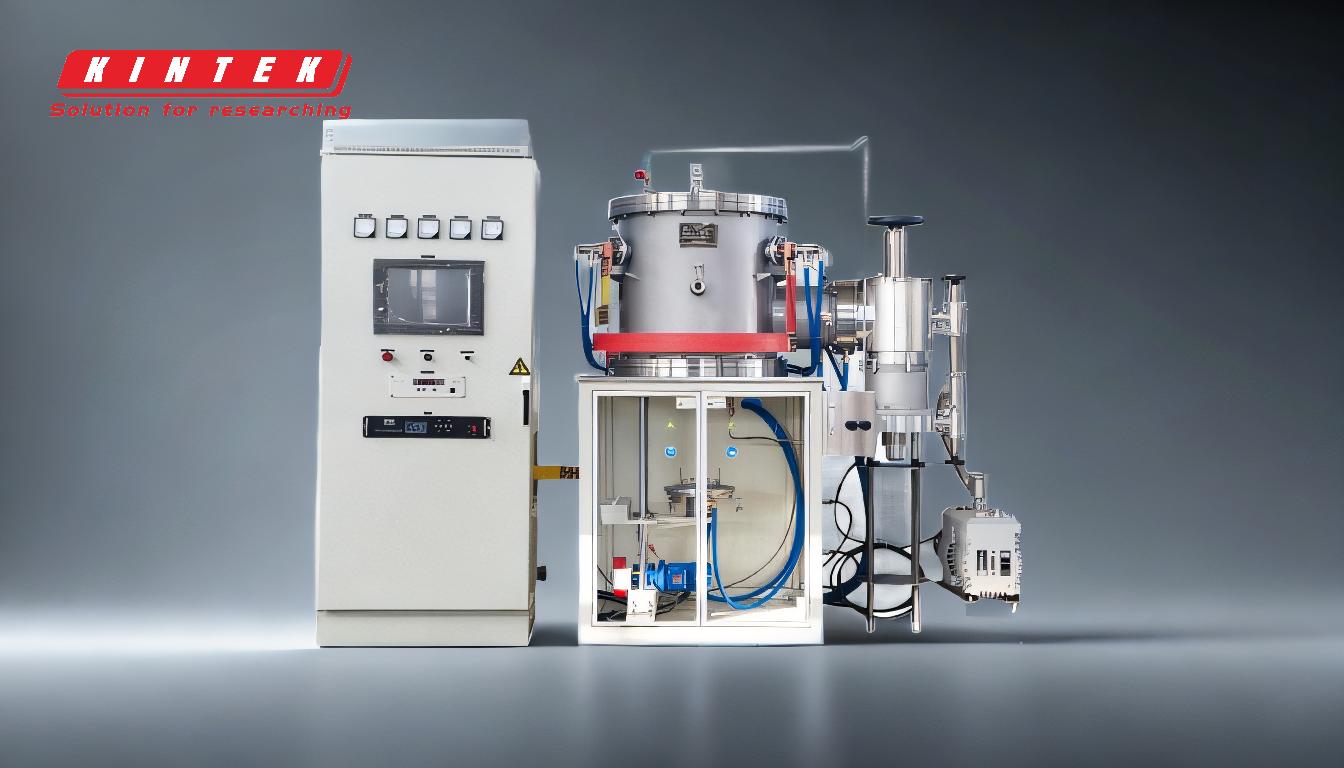
-
Electromagnetic Induction:
- The core principle of an induction furnace is electromagnetic induction, where an alternating current (AC) in the primary coil creates a fluctuating magnetic field.
- This magnetic field penetrates the conductive metal charge placed inside the furnace, inducing eddy currents within the metal.
-
Joule Effect (Resistive Heating):
- The induced eddy currents flow through the metal, encountering electrical resistance.
- According to the Joule effect, this resistance converts electrical energy into heat, raising the temperature of the metal rapidly and uniformly.
-
Transformer Analogy:
- The furnace operates like a transformer, with the primary coil (connected to the AC power supply) acting as the primary winding and the metal charge acting as the secondary winding.
- Energy is transferred from the primary coil to the metal charge without physical contact, ensuring clean and efficient heating.
-
Non-Contact Heating:
- Induction heating is a non-contact process, meaning the heat is generated directly within the metal charge rather than being transferred from an external source.
- This eliminates contamination and allows for precise control over the melting process.
-
High-Frequency Operation:
- Induction furnaces typically operate at high frequencies (500 Hz to 1000 Hz), which enhances the efficiency of energy transfer and ensures rapid heating.
- Higher frequencies also improve the penetration depth of the magnetic field, making the process suitable for a wide range of metal types and sizes.
-
Cooling System:
- The primary coil is cooled by circulating water to prevent overheating and maintain operational efficiency.
- This cooling mechanism ensures the longevity of the furnace components and consistent performance.
-
Applications and Advantages:
- Induction furnaces are widely used in melting metals and creating alloys with precise compositions.
- Advantages include energy efficiency, rapid heating, minimal heat loss, and the ability to maintain a clean and controlled environment for melting.
-
Heat Generation Within the Metal:
- Unlike traditional furnaces, where heat is applied externally, induction furnaces generate heat directly within the metal charge.
- This results in faster melting times and reduced energy consumption.
By combining electromagnetic induction and the Joule effect, induction furnaces provide a highly efficient and controlled method for melting metals, making them indispensable in modern metallurgical processes.
Summary Table:
Key Aspect | Details |
---|---|
Principle | Electromagnetic induction and Joule effect |
Heating Mechanism | Non-contact heating via eddy currents |
Frequency Range | 500 Hz to 1000 Hz |
Cooling System | Water-cooled primary coil |
Applications | Melting metals, creating precise alloys |
Advantages | Energy efficiency, rapid heating, minimal heat loss, clean melting process |
Discover how an induction furnace can optimize your metal melting process—contact our experts today!