The best heating element for a furnace depends on several factors, including the required operating temperature, furnace type (e.g., vacuum, muffle, or industrial), and the specific application. Common heating elements include ferrochromium-aluminum wire, silicon carbide rods, silicon molybdenum rods, and high-strength graphite or carbon-carbon composites. Each material has distinct temperature limits and performance characteristics. For instance, ferrochromium-aluminum wire is suitable for temperatures up to 1200°C, while silicon carbide rods can handle up to 1400°C, and silicon molybdenum rods are ideal for 1400°C-1700°C. Additionally, factors like furnace atmosphere, maintenance practices, and design considerations play a crucial role in determining the optimal heating element for reliable and efficient performance.
Key Points Explained:
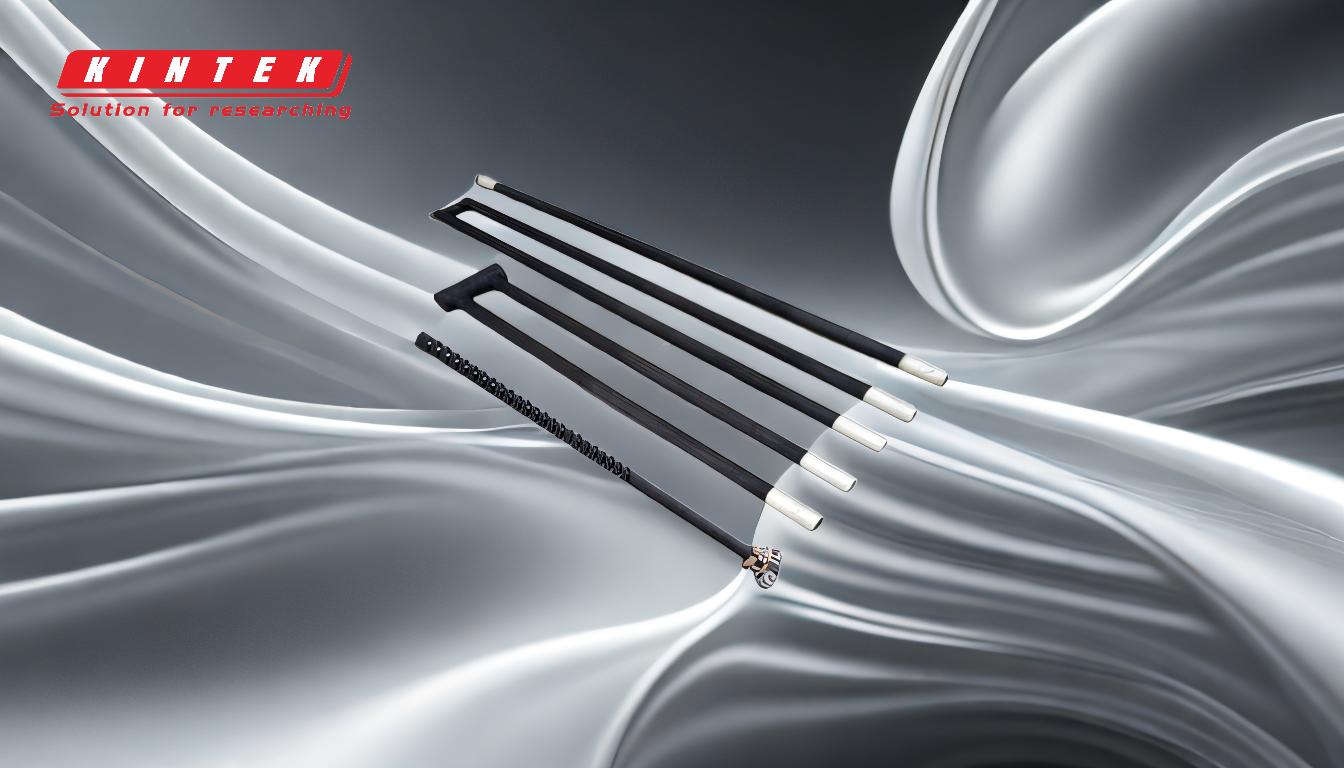
-
Operating Temperature Range:
- Different heating elements are designed for specific temperature ranges. For example:
- Ferrochromium-aluminum wire: Suitable for temperatures up to 1200°C.
- Silicon carbide rods: Effective for temperatures between 1300°C and 1400°C.
- Silicon molybdenum rods: Ideal for high-temperature applications ranging from 1400°C to 1700°C.
- Selecting a heating element that matches the required temperature range ensures optimal performance and longevity.
- Different heating elements are designed for specific temperature ranges. For example:
-
Furnace Type and Application:
- The type of furnace (e.g., vacuum, muffle, or industrial) influences the choice of heating element. For instance:
- Vacuum furnaces: Often use high-strength graphite or carbon-carbon composite materials due to their ability to withstand high temperatures and improve cooling rates.
- Muffle furnaces: Require heating elements like resistance wire, silicon carbide rods, or silicon molybdenum rods, depending on the temperature range.
- The furnace's purpose and importance in production also play a role in determining the most suitable heating element.
- The type of furnace (e.g., vacuum, muffle, or industrial) influences the choice of heating element. For instance:
-
Material Properties:
- The material of the heating element affects its performance and durability. Key considerations include:
- Oxide layer protection: The lifespan of heating elements like silicon carbide and silicon molybdenum rods depends on the integrity of their oxide layer, which can be compromised by frequent shutdowns or exposure to corrosive gases.
- Heat storage and cooling rates: Carbon-carbon composites offer thinner thickness and smaller heat storage, enhancing cooling rates in vacuum furnaces.
- The material of the heating element affects its performance and durability. Key considerations include:
-
Furnace Atmosphere:
- The presence or absence of specific atmospheres (e.g., endo gas or low-pressure carburizing) influences the choice of heating element. For example:
- Endo gas atmospheres: May require heating elements designed to resist oxidation or chemical reactions.
- Vacuum or inert atmospheres: Favor materials like graphite or carbon-carbon composites that perform well in low-oxygen environments.
- The presence or absence of specific atmospheres (e.g., endo gas or low-pressure carburizing) influences the choice of heating element. For example:
-
Design and Installation:
- Proper design and installation of heating elements are critical to avoid operational issues. Poorly designed or installed elements are more likely to fail or cause problems, such as uneven heating or reduced efficiency.
-
Maintenance and Longevity:
- Regular maintenance and proper use are essential to extend the lifespan of heating elements. Factors to consider include:
- Avoiding frequent shutdowns, which can damage the oxide layer on heating elements.
- Protecting elements from corrosive gases or environments that could degrade their performance.
- Regular maintenance and proper use are essential to extend the lifespan of heating elements. Factors to consider include:
-
Cost and Availability:
- The availability of materials like natural gas or specific alloys may influence the choice of heating elements. Additionally, cost considerations, including initial investment and long-term maintenance, should be evaluated to ensure cost-effectiveness.
By carefully considering these factors, you can select the best heating element for your furnace, ensuring reliable performance, efficiency, and durability tailored to your specific needs.
Summary Table:
Heating Element | Temperature Range | Furnace Type | Key Features |
---|---|---|---|
Ferrochromium-aluminum wire | Up to 1200°C | Muffle, Industrial | Cost-effective, suitable for moderate temperatures |
Silicon carbide rods | 1300°C - 1400°C | Muffle, Industrial | High durability, ideal for consistent high-temperature use |
Silicon molybdenum rods | 1400°C - 1700°C | Muffle, Industrial | Excellent for extreme high-temperature applications |
High-strength graphite/carbon | Up to 2000°C+ | Vacuum | Thin thickness, smaller heat storage, ideal for vacuum environments |
Need help selecting the perfect heating element for your furnace? Contact our experts today for tailored solutions!