Carburizing is a heat treatment process that increases the carbon content on the surface of low-carbon steel, enhancing its hardness and wear resistance while maintaining a ductile core. The carbon content added during carburizing typically ranges between 0.8% and 1.2%, depending on the steel type and process parameters like temperature and time. This process is widely used to produce components that require a hard exterior for durability and a tough interior for flexibility, such as gears, shafts, and fasteners.
Key Points Explained:
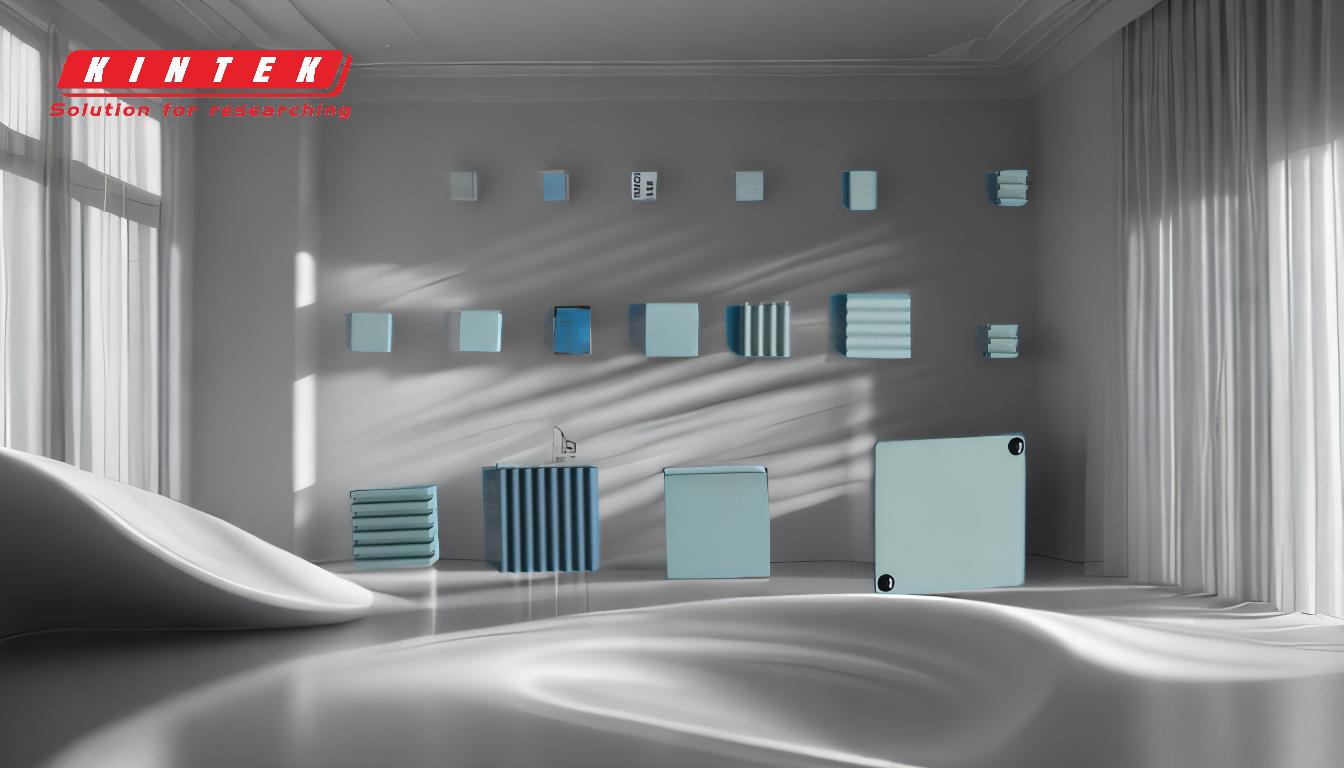
-
Definition and Purpose of Carburizing:
- Carburizing is a case hardening process where carbon is diffused into the surface of low-carbon steel to increase its hardness and wear resistance.
- The process is used to create parts with a hard outer layer and a soft, ductile core, making them ideal for applications requiring both durability and flexibility.
-
Carbon Content in Carburizing:
- The carbon content added to the steel surface during carburizing typically ranges between 0.8% and 1.2%.
- This range is determined by the Iron Carbon Equilibrium diagram, which dictates the optimal carbon potential for achieving the desired hardness and microstructure.
-
Factors Influencing Carbon Content:
- Temperature: Higher temperatures increase the diffusion rate of carbon into the steel, allowing for greater carbon absorption.
- Time: Longer carburizing times result in deeper case depths and higher carbon content in the surface layer.
- Steel Type: The base carbon content of the steel and its alloying elements influence the final carbon content and hardness.
-
Process Mechanism:
- The steel is heated to temperatures below its melting point in a carbon-rich environment, such as a gas or solid medium containing carbon.
- Carbon atoms diffuse into the steel surface, altering its grain structure and increasing its hardness.
- After carburizing, the steel is quenched in oil or another medium to lock in the hardened surface layer.
-
Applications of Carburized Parts:
- Carburizing is commonly used to produce gears, shafts, fasteners, and tools that require a combination of surface hardness and core toughness.
- The process is ideal for components subjected to high wear, abrasion, or fatigue.
-
Typical Case Depths:
- The depth of the hardened layer (case depth) typically ranges from 0.020″ to 0.050″, depending on the application and process parameters.
- Deeper case depths are achieved with longer carburizing times and higher temperatures.
-
Comparison with Carbonitriding:
- While carburizing focuses solely on adding carbon, carbonitriding introduces both carbon and nitrogen into the steel.
- Carbonitriding is used when through-hardening is required, providing additional strength and wear resistance.
-
Benefits of Carburizing:
- Improved Wear Resistance: The hard surface layer resists abrasion and wear.
- Enhanced Fatigue Strength: The process increases the steel's ability to withstand cyclic loading.
- Ductile Core: The soft interior ensures the part remains flexible and resistant to fracture.
By understanding the carbon content and process parameters of carburizing, manufacturers can tailor the treatment to meet specific performance requirements for their components. This makes carburizing a versatile and essential process in the production of durable mechanical parts.
Summary Table:
Aspect | Details |
---|---|
Carbon Content | 0.8% to 1.2% (surface layer) |
Process Temperature | Below melting point, typically 850°C to 950°C |
Case Depth | 0.020″ to 0.050″ (adjustable with time and temperature) |
Applications | Gears, shafts, fasteners, tools |
Benefits | Improved wear resistance, enhanced fatigue strength, ductile core |
Comparison | Carburizing vs. Carbonitriding: Carbon only vs. Carbon + Nitrogen addition |
Discover how carburizing can optimize your steel components—contact our experts today for tailored solutions!