The compression ratio of a pellet mill die is a critical factor in determining the quality and durability of the pellets produced. It is defined as the ratio of the effective length (E) of the die to the diameter (D) of the die hole, often referred to as the L/D ratio. This ratio influences the resistance the feed encounters as it moves through the die, directly affecting pellet compactness and density. A higher L/D ratio results in greater resistance and more compact pellets, while a lower L/D ratio reduces resistance and produces less compact pellets. Understanding and optimizing the compression ratio is essential for achieving desired pellet quality and extending the life of the pellet mill die.
Key Points Explained:
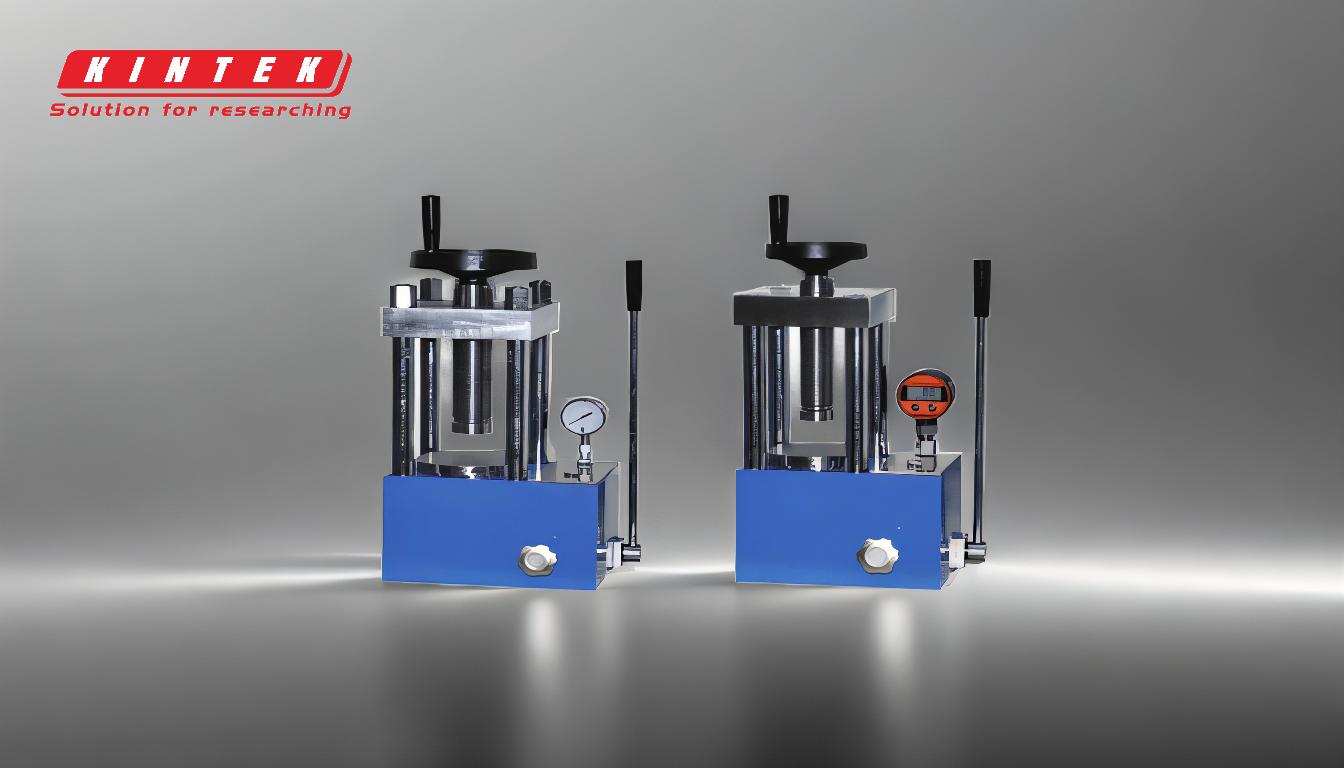
-
Definition of Compression Ratio:
- The compression ratio of a pellet mill die is the ratio of the effective length (E) to the diameter (D) of the die hole (L/D ratio). This ratio is crucial because it determines the resistance the feed material encounters as it is forced through the die, impacting the compactness and density of the pellets.
-
Effective Length (E):
- The effective length is the portion of the die thickness that actively works on compressing the feed material. A greater effective length results in more compact and denser pellets, while a shorter effective length produces less compact pellets. This parameter is directly related to the quality of the pellets and the efficiency of the pellet mill.
-
Relief (R):
- Relief refers to the space provided for the pellet feed to exit the die. A lesser relief increases pellet compactness by allowing more compression before the pellets exit the die. Conversely, more relief reduces compactness. The amount of relief needed varies depending on the feed formulation and specific production requirements.
-
Impact of L/D Ratio on Pellet Quality:
- A high L/D ratio provides high resistance, leading to more compact and durable pellets. This is beneficial for applications requiring high pellet quality and durability. On the other hand, a low L/D ratio results in lower resistance, producing less compact pellets, which might be suitable for specific applications where density is not a critical factor.
-
Factors Affecting Die Life:
- The life of a pellet mill die is influenced by several factors, including feed formulation, raw material properties, fat content, particle size, moisture content, and operator skill. High fiber content, abrasive materials, and poor conditioning can reduce die life, while consistent particle size, optimal moisture content, and regular maintenance can extend it.
-
Optimizing Die Performance:
- To maximize die life and performance, it is essential to consider factors such as feed formulation, regular maintenance, and operator skill. Using separate dies for different types of feed, such as broiler and layer feed, can also optimize performance and extend die life.
-
Maintenance Practices:
- Regular maintenance practices, such as cleaning magnets every 6 hours, timely changing of roll shells, tightening roll shell support stud bolts, and changing the side of the die for uniform wear, are crucial for maintaining die performance and extending its life.
Understanding and optimizing the compression ratio, along with proper maintenance and operational practices, are essential for achieving high-quality pellet production and extending the life of the pellet mill die.
Summary Table:
Key Factor | Description |
---|---|
Compression Ratio (L/D) | Ratio of effective length (E) to die hole diameter (D). Higher ratios = denser pellets. |
Effective Length (E) | Portion of die thickness compressing feed. Longer E = more compact pellets. |
Relief (R) | Space for pellet exit. Less R = more compact pellets. |
Impact on Pellet Quality | High L/D = durable, dense pellets. Low L/D = less compact pellets. |
Die Life Factors | Feed formulation, raw materials, moisture, particle size, and maintenance. |
Maintenance Practices | Regular cleaning, roll shell changes, and uniform die wear management. |
Optimize your pellet mill die performance—contact our experts today for tailored solutions!