The cooling system in a furnace is a critical component designed to manage and control the temperature of the furnace and its contents after high-temperature processing. It ensures rapid and controlled cooling, which is essential for achieving desired material properties, maintaining process efficiency, and preventing damage to the furnace and its components. Cooling systems vary depending on the type of furnace and its application, but they generally involve the use of inert gases, water cooling, or specialized cooling zones. Proper cooling system management is vital to avoid operational issues, energy inefficiencies, and potential damage to the furnace.
Key Points Explained:
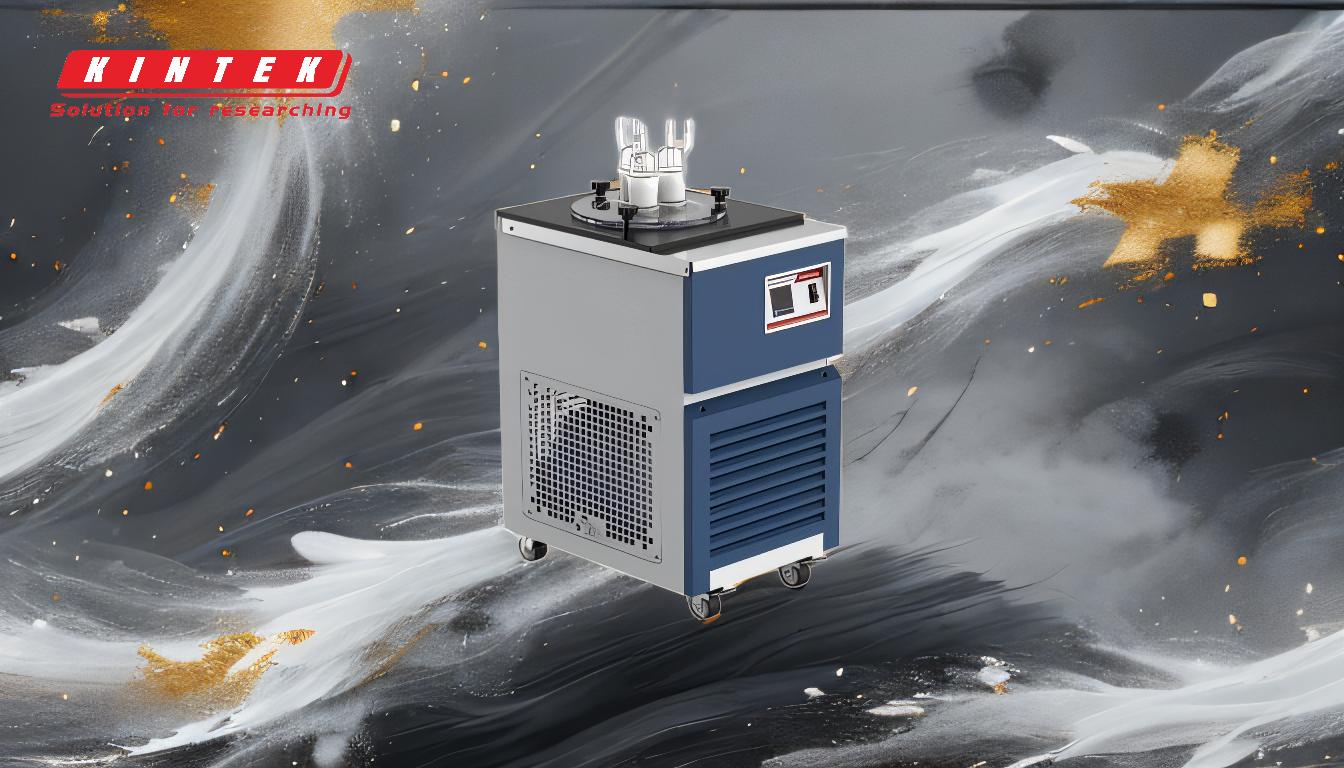
-
Purpose of Cooling Systems in Furnaces
- Cooling systems are essential for rapidly lowering the temperature of workpieces after high-temperature processing. This ensures that the desired material properties, such as hardness, strength, and microstructure, are achieved.
- They also protect the furnace components from thermal stress and damage caused by prolonged exposure to high temperatures.
-
Types of Cooling Systems
-
Inert Gas Cooling (Vacuum Furnaces):
- In high-temperature vacuum furnaces, inert gases like argon are pumped into the airtight chamber to facilitate rapid cooling. This method allows precise control over the cooling rate, ensuring consistent and high-quality heat treatment results.
-
Water Cooling (Submerged Arc Furnaces):
- In submerged arc furnaces, cooling water is circulated through components such as short nets, pressure rings, and furnace shells to manage high-temperature conditions. A water separator is often used to ensure efficient cooling.
-
Water-Jacketed Cooling (Sintering Furnaces):
- Sintering furnaces use water-jacketed cooling zones to cool down sintered parts to a manageable temperature for further handling. This method is particularly useful for batch processes.
-
Chiller-Based Cooling (Sputtering Process):
- In sputtering processes, chillers with water knockout drums are used to cool vacuum pumps and targets. While effective, this method can reduce production rates and increase energy costs.
-
Inert Gas Cooling (Vacuum Furnaces):
-
Components of a Cooling System
- Cooling systems typically include:
- Manifolds: Compact units containing pressure regulators, valves, and flow regulators.
- Hoses and Fittings: Supply and drain hoses for transporting cooling media.
- Optional Dual Loop Systems: Advanced setups that provide additional cooling capacity for high-demand applications.
- Cooling systems typically include:
-
Importance of Cooling System Management
- Proper maintenance of cooling systems is crucial to prevent operational failures. For example, in vacuum furnaces, blocked cooling water channels can lead to overheating and automatic shutdowns.
- Efficient cooling system management also minimizes energy consumption and extends the lifespan of furnace components.
-
Challenges and Trade-offs
- While cooling systems are essential, they can introduce challenges such as increased energy costs and reduced production rates, particularly in processes like sputtering.
- Balancing cooling efficiency with operational costs is a key consideration for furnace operators.
By understanding the role and mechanisms of cooling systems in various types of furnaces, operators can optimize their processes, improve product quality, and ensure the longevity of their equipment.
Summary Table:
Aspect | Details |
---|---|
Purpose | Rapid and controlled cooling to achieve desired material properties. |
Types | Inert gas cooling, water cooling, water-jacketed cooling, chiller-based. |
Components | Manifolds, hoses, fittings, optional dual loop systems. |
Importance | Prevents damage, ensures efficiency, and extends furnace lifespan. |
Challenges | Energy costs, reduced production rates, and balancing efficiency. |
Optimize your furnace cooling system today—contact our experts for tailored solutions!