Deposition is a process where material is laid down or deposited onto a surface, either through natural processes like sediment transport or through engineered methods like physical vapor deposition. In natural contexts, deposition involves the settling of sediment carried by wind, water, or ice, which can include particles like sand, mud, or dissolved salts. In industrial and scientific applications, physical deposition techniques are used to create thin films of solid material. These methods involve placing a material in an energetic environment, causing particles to escape its surface and form a solid layer on a cooler surface within a vacuum chamber. The process is widely used in manufacturing, electronics, and materials science.
Key Points Explained:
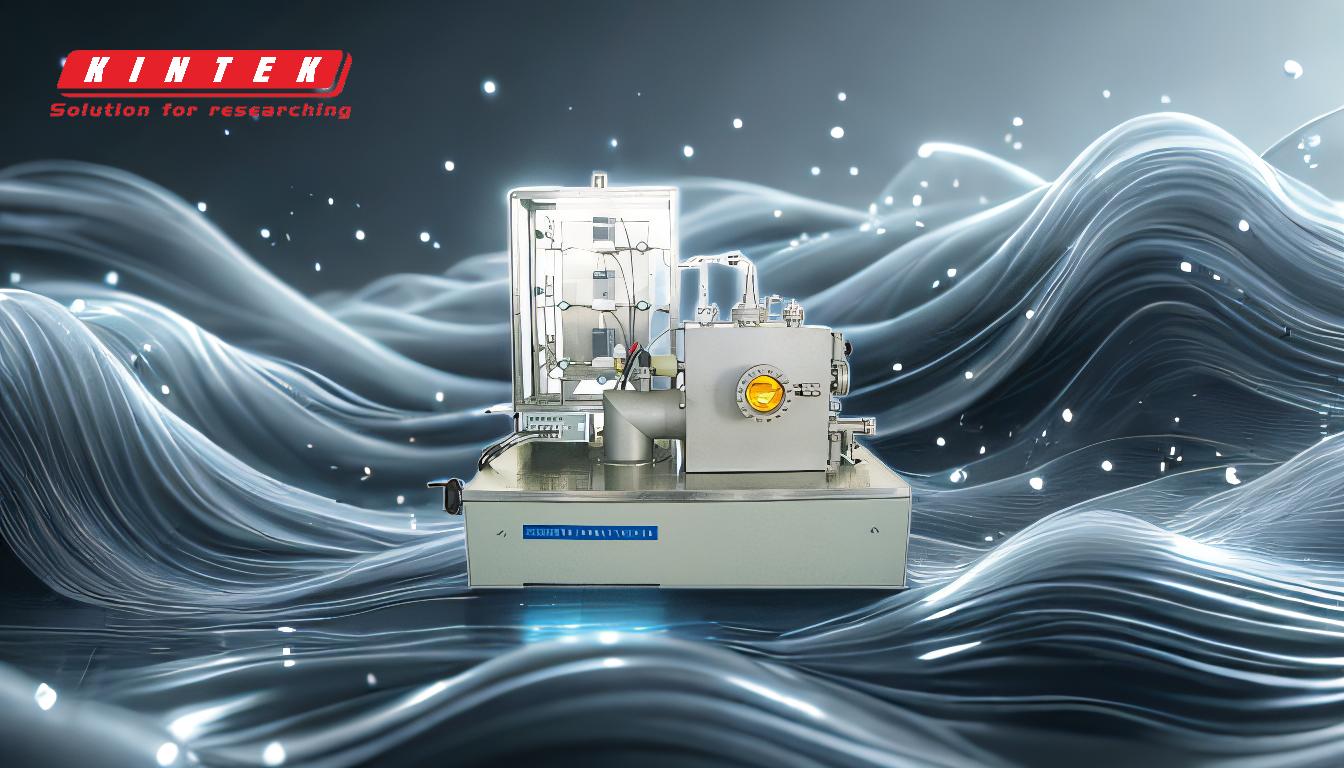
-
Definition of Deposition:
- Deposition refers to the process of laying down or depositing material onto a surface. This can occur naturally, such as when sediment settles after being transported by wind, water, or ice, or artificially, as in industrial processes that create thin films of material.
-
Natural Deposition Processes:
- In natural environments, deposition is a key part of geological and ecological cycles. Sediment, which can include particles like pebbles, sand, and mud, is transported by natural forces such as wind, flowing water, or glaciers. Over time, these particles settle and accumulate, forming layers of sediment.
- Dissolved salts can also be deposited through processes like evaporation or biological activity, such as the formation of sea shells.
-
Industrial and Scientific Deposition:
- In industrial and scientific contexts, deposition is a controlled process used to create thin films of solid material. This is often achieved through physical vapor deposition (PVD) or similar techniques.
- The material to be deposited is placed in an energetic environment, such as a vacuum chamber, where it is subjected to high energy. This causes particles to escape from the material's surface and travel through the chamber.
- These particles then settle on a cooler surface, forming a thin, uniform layer of solid material. This process is widely used in the production of semiconductors, coatings, and other advanced materials.
-
Applications of Deposition:
- Electronics: Deposition is crucial in the fabrication of microchips, solar panels, and other electronic components. Thin films of conductive, insulating, or semiconducting materials are deposited onto substrates to create functional devices.
- Coatings: Deposition techniques are used to apply protective or decorative coatings to surfaces. For example, anti-reflective coatings on eyeglasses or wear-resistant coatings on industrial tools.
- Materials Science: Researchers use deposition to create new materials with unique properties, such as superconductors or nanomaterials.
-
Types of Deposition Techniques:
- Physical Vapor Deposition (PVD): Involves vaporizing a material in a vacuum and depositing it onto a substrate. Common PVD methods include sputtering and evaporation.
- Chemical Vapor Deposition (CVD): Uses chemical reactions to deposit a solid material from a gas phase onto a substrate. This method is often used for creating high-purity, high-performance materials.
- Electrochemical Deposition: Involves using electrical currents to deposit material from a solution onto a conductive surface, commonly used in electroplating.
-
Key Factors in Deposition:
- Energy Source: The energy source (e.g., heat, plasma, or electrical current) determines how particles are released from the source material.
- Vacuum Environment: A vacuum chamber is often used to control the environment, minimizing contamination and allowing precise control over the deposition process.
- Substrate Temperature: The temperature of the substrate can influence the quality and properties of the deposited film. A cooler surface typically results in a more uniform layer.
-
Advantages of Deposition Techniques:
- Precision: Deposition allows for the creation of extremely thin and uniform layers, often at the nanometer scale.
- Versatility: A wide range of materials, including metals, ceramics, and polymers, can be deposited using various techniques.
- Scalability: Deposition processes can be scaled up for industrial production or down for laboratory research.
-
Challenges in Deposition:
- Cost: High-energy processes and vacuum equipment can be expensive to operate and maintain.
- Complexity: Achieving the desired film properties often requires precise control over numerous variables, such as temperature, pressure, and energy input.
- Contamination: Even small amounts of contamination can significantly affect the quality of the deposited film, making cleanliness a critical factor.
By understanding the deposition process, whether in natural or industrial contexts, we can better appreciate its role in shaping our environment and advancing technology.
Summary Table:
Aspect | Details |
---|---|
Definition | Process of laying down material onto a surface, naturally or artificially. |
Natural Processes | Sediment transport by wind, water, or ice; salt deposition via evaporation. |
Industrial Techniques | Physical Vapor Deposition (PVD), Chemical Vapor Deposition (CVD). |
Applications | Electronics, coatings, materials science. |
Advantages | Precision, versatility, scalability. |
Challenges | High cost, complexity, contamination risks. |
Unlock the potential of deposition for your projects—contact our experts today!