The desired range of chamber pressure to start the sputtering process typically falls between 5 x 10^-4 mbar and 1 x 10^-2 mbar when using an argon plasma. This range ensures optimal conditions for generating a stable plasma and achieving efficient sputtering. The process begins by evacuating the chamber to a high vacuum (around 10^-6 mbar) to reduce background gases and ensure purity. Once the base pressure is achieved, argon gas is introduced, and the pressure is regulated to the operational range. Lower pressures allow for high-energy ballistic impacts, while higher pressures moderate ion motion through collisions with gas atoms. Proper pressure control is critical for achieving the desired thin-film quality and deposition efficiency.
Key Points Explained:
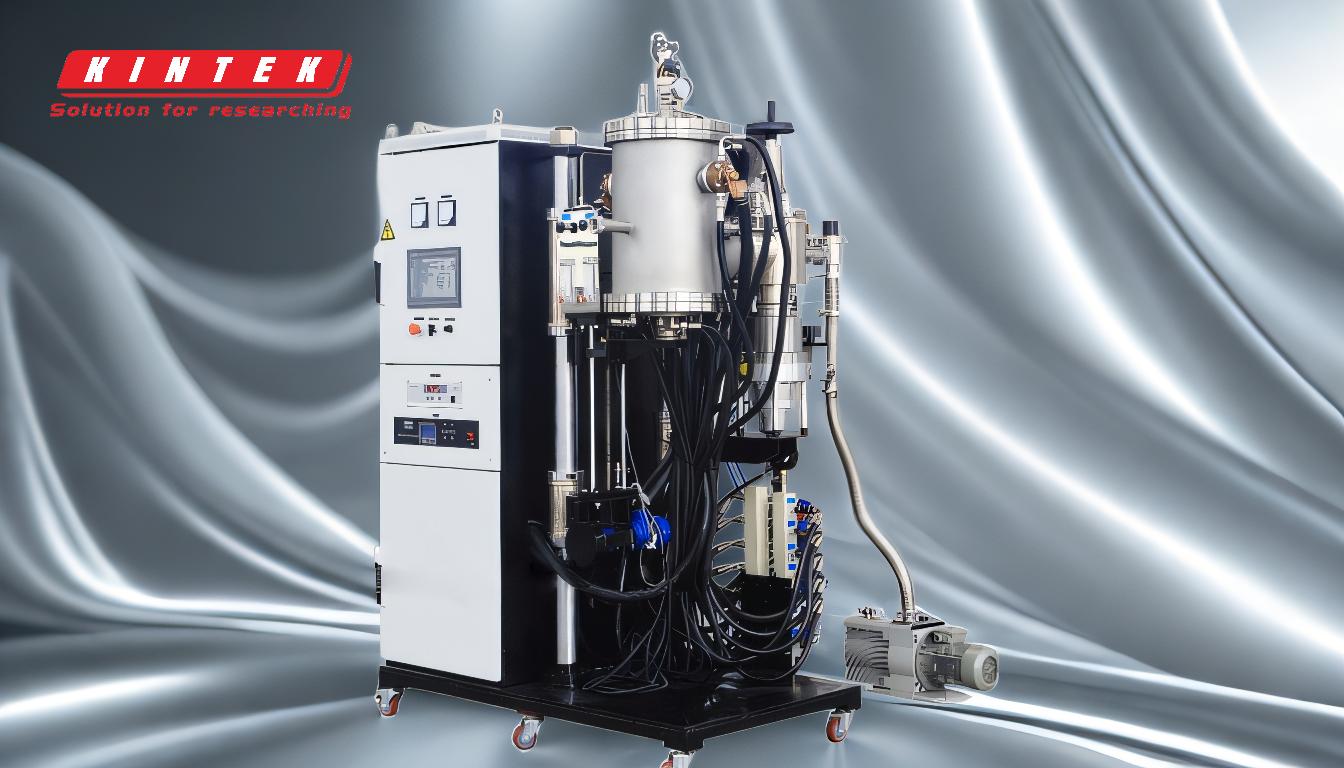
-
Base Pressure Requirements:
- Before introducing the sputtering gas (e.g., argon), the chamber must be evacuated to a high vacuum, typically in the range of 10^-6 mbar. This ensures minimal contamination from background gases and prepares the chamber for the sputtering process.
- Achieving this base pressure is essential for maintaining the purity of the deposited thin film and ensuring consistent process conditions.
-
Operational Pressure Range:
- Once the base pressure is achieved, argon gas is introduced, and the chamber pressure is regulated to the operational range of 5 x 10^-4 mbar to 1 x 10^-2 mbar.
- This range is critical for generating and sustaining a stable plasma, which is necessary for the sputtering process to occur effectively.
-
Impact of Pressure on Ion Motion:
- At lower pressures, sputtered ions travel ballistically with high energy, leading to more direct and energetic impacts on the substrate. This is ideal for achieving high-quality, dense thin films.
- At higher pressures, ions collide more frequently with gas atoms, causing them to move diffusively. This moderates their energy and results in a more random deposition pattern, which can affect film uniformity and density.
-
Pressure Control Mechanisms:
- Pressure in the sputter chamber is controlled using flow controllers and throttle valves. Turbomolecular pumps (TMPs) are used to achieve the initial high vacuum, but their rotational speed is too slow for precise pressure regulation during sputtering.
- A throttle valve is often used in conjunction with the TMP to fine-tune the pressure during the sputtering process. Dry pump systems are commonly employed to back magnetic TMPs, providing better control and efficiency.
-
Role of Argon Gas:
- Argon is the most commonly used sputtering gas due to its inert nature and ability to generate a stable plasma. The introduction of argon gas at the desired pressure range initiates the plasma generation process.
- The plasma ionizes the argon atoms, creating positively charged argon ions that are accelerated toward the negatively charged cathode (target material). This ion bombardment ejects atoms from the target, which then deposit onto the substrate.
-
Importance of Vacuum Conditions:
- Vacuum conditions are crucial for the sputtering process, as they minimize the presence of contaminants and ensure a controlled environment for deposition.
- The vacuum pump continuously removes air and other gases from the chamber, maintaining the required pressure levels throughout the process.
-
Practical Considerations for Equipment:
- Modern sputtering systems often use dry pump systems for backing magnetic TMPs, as they provide better control over pressure and reduce the risk of contamination.
- Flow controllers and throttle valves are essential components for maintaining the precise pressure range required for sputtering, ensuring consistent and high-quality film deposition.
By carefully controlling the chamber pressure within the specified range, the sputtering process can achieve optimal thin-film deposition with the desired properties, such as purity, density, and uniformity.
Summary Table:
Aspect | Details |
---|---|
Base Pressure | 10^-6 mbar (high vacuum) to minimize contamination. |
Operational Pressure | 5x10^-4 to 1x10^-2 mbar for stable plasma and efficient sputtering. |
Low Pressure Effects | High-energy ballistic impacts for dense, high-quality films. |
High Pressure Effects | Diffusive ion motion for moderated energy and random deposition patterns. |
Pressure Control | Flow controllers, throttle valves, and dry pump systems for precision. |
Role of Argon Gas | Generates stable plasma for efficient ion bombardment and thin-film growth. |
Vacuum Importance | Ensures purity and controlled deposition environment. |
Optimize your sputtering process with expert guidance—contact us today!