Tube furnaces and box furnaces are both essential tools in high-temperature processing, but they differ significantly in design, application, and functionality. Tube furnaces are compact, cylindrical, and ideal for continuous heating of small or powdered samples, often used in chemical synthesis under inert atmospheres. They offer precise temperature and gas flow control, making them suitable for applications like graphene production. Box furnaces, on the other hand, are larger and designed for batch heating of larger objects in a sealed chamber. They are commonly used for heating, ash content measurement, and processes requiring a stable atmosphere. The choice between the two depends on the specific needs of the application, including sample size, heating uniformity, and space constraints.
Key Points Explained:
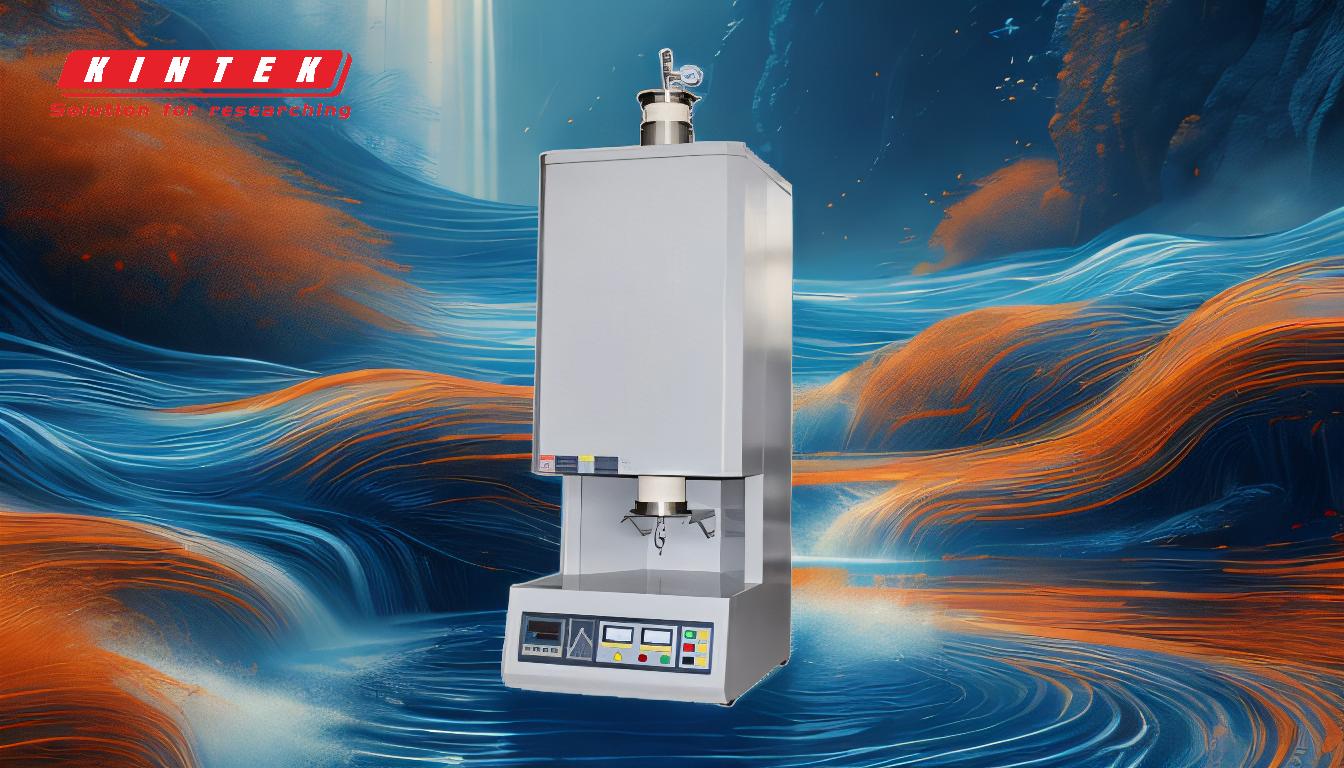
-
Design and Structure:
- Tube Furnace: Compact and cylindrical, with internal heating elements. The design allows for continuous heating of materials as they pass through the tube.
- Box Furnace: Larger and box-shaped, with heating elements surrounding the chamber. It is designed for batch heating of materials inside a sealed space.
-
Applications:
- Tube Furnace: Primarily used for chemical synthesis under inert atmospheres, continuous heating of long or powdered samples, and precise temperature control applications like graphene production.
- Box Furnace: Commonly used for heating larger objects, ash content measurement, and processes requiring a stable atmosphere, such as sintering stainless steel or targets.
-
Heating Elements:
- Both furnaces use silicon rods as heating elements. However, tube furnaces often have a circulated atmosphere, while box furnaces maintain a stable atmosphere.
-
Space and Capacity:
- Tube Furnace: More compact and space-efficient, suitable for smaller samples and laboratory settings.
- Box Furnace: Larger and requires more space, ideal for batch processing of larger objects.
-
Temperature and Gas Flow Control:
- Tube Furnace: Offers more precise and immediate control of temperature and gas flow, with exposed ends conducive to managing temperature gradients.
- Box Furnace: Provides uniform heating within the chamber but lacks the precise gas flow control of tube furnaces.
-
Customization and Features:
- Both furnaces can be customized to meet specific needs, including size, heating elements, and additional features like vacuum and inert gas management systems.
-
Heating Uniformity:
- Tube Furnace: Suitable for processes requiring precise temperature gradients and uniform heating along the length of the tube.
- Box Furnace: Provides uniform heating within the chamber, ideal for batch processing of small parts or large workpieces.
-
Atmosphere Control:
- Tube Furnace: Typically operates under atmospheric conditions, with the ability to manage inert gas flow.
- Box Furnace: Often operates as a muffle furnace, maintaining a stable and controlled atmosphere within the chamber.
Understanding these differences is crucial for selecting the appropriate furnace for your specific application, ensuring optimal performance and efficiency.
Summary Table:
Feature | Tube Furnace | Box Furnace |
---|---|---|
Design | Compact, cylindrical | Larger, box-shaped |
Applications | Chemical synthesis, graphene production | Heating, ash content measurement |
Heating Elements | Silicon rods, circulated atmosphere | Silicon rods, stable atmosphere |
Space & Capacity | Compact, ideal for small samples | Larger, suitable for batch processing |
Temperature Control | Precise and immediate | Uniform heating within chamber |
Atmosphere Control | Manages inert gas flow | Stable and controlled atmosphere |
Need help selecting the right furnace for your application? Contact our experts today for personalized advice!