Vacuum furnaces and inert gas furnaces are both specialized equipment used for heat treatment processes, but they differ significantly in their operating environments and mechanisms. A vacuum furnace operates in a low-pressure or vacuum environment, removing air and reactive gases to prevent oxidation and contamination. It uses electric heating elements and ensures uniform temperature distribution without convection. In contrast, an inert gas furnace replaces the air with inert gases like argon to create a non-reactive atmosphere, allowing for controlled cooling and preventing oxidation. While both are designed to minimize contamination, vacuum furnaces excel in high-temperature applications and precision, whereas inert gas furnaces are more versatile for processes requiring rapid cooling and lower-temperature operations.
Key Points Explained:
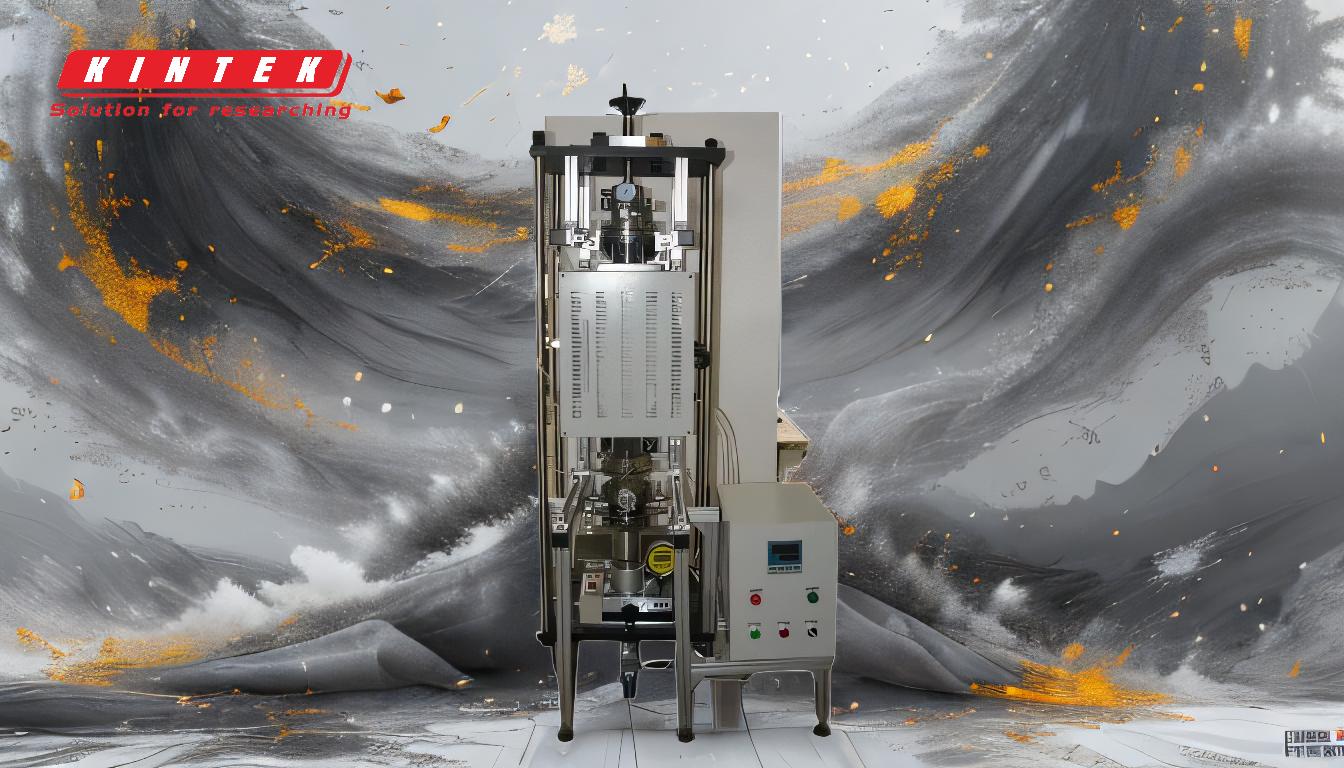
-
Operating Environment:
- Vacuum Furnace: Operates in a vacuum or low-pressure environment, removing air and reactive gases entirely. This eliminates oxidation, decarburization, and contamination, making it ideal for high-precision applications.
- Inert Gas Furnace: Uses inert gases like argon or nitrogen to replace air in the chamber. While it prevents oxidation, it does not achieve the same level of contamination control as a vacuum furnace.
-
Heating Mechanism:
- Vacuum Furnace: Typically uses electric heating elements such as graphite or ceramic coils. The absence of convection ensures uniform heat distribution and precise temperature control.
- Inert Gas Furnace: Can use various heating methods, including electric or gas-based systems. The inert gas helps maintain a stable environment but does not eliminate convection entirely.
-
Cooling Process:
- Vacuum Furnace: Cooling is often slower and controlled, relying on the vacuum environment to prevent contamination during the cooling phase.
- Inert Gas Furnace: Inert gases like argon can be used for rapid cooling, which is beneficial for processes requiring quick transitions from high to low temperatures.
-
Temperature Range:
- Vacuum Furnace: Capable of reaching extremely high temperatures (up to 2,400°F or higher), making it suitable for advanced metallurgical processes.
- Inert Gas Furnace: Generally operates at lower temperatures compared to vacuum furnaces, though it can still handle a wide range of heat treatment applications.
-
Contamination Control:
- Vacuum Furnace: Offers superior contamination control due to the complete absence of air and reactive gases. This is critical for processes requiring high purity, such as sintering or brazing.
- Inert Gas Furnace: Provides good contamination control but may still allow trace amounts of impurities, depending on the quality of the inert gas and the sealing of the chamber.
-
Applications:
- Vacuum Furnace: Ideal for high-temperature processes like sintering, annealing, and brazing, where precision and purity are paramount.
- Inert Gas Furnace: Suitable for processes requiring controlled cooling, such as hardening and tempering, as well as applications where rapid cooling is necessary.
-
Cost and Maintenance:
- Vacuum Furnace: Typically has higher initial and operating costs due to the complexity of the vacuum system and the need for high-quality materials to maintain the vacuum seal.
- Inert Gas Furnace: Generally more cost-effective, with lower operating costs and simpler maintenance requirements.
-
Flexibility:
- Vacuum Furnace: Less flexible in terms of cooling options but offers unmatched precision and purity for high-temperature applications.
- Inert Gas Furnace: More versatile, especially for processes requiring rapid cooling or lower-temperature treatments.
In summary, the choice between a vacuum furnace and an inert gas furnace depends on the specific requirements of the heat treatment process. Vacuum furnaces are preferred for high-precision, high-temperature applications where contamination control is critical, while inert gas furnaces are more suitable for processes requiring rapid cooling and flexibility at lower temperatures.
Summary Table:
Aspect | Vacuum Furnace | Inert Gas Furnace |
---|---|---|
Operating Environment | Operates in a vacuum or low-pressure environment, eliminating air and reactive gases. | Uses inert gases like argon or nitrogen to replace air, preventing oxidation. |
Heating Mechanism | Electric heating elements (e.g., graphite or ceramic coils) ensure uniform heating. | Can use electric or gas-based systems; inert gas maintains a stable environment. |
Cooling Process | Slower, controlled cooling in a vacuum environment. | Rapid cooling using inert gases like argon. |
Temperature Range | Extremely high temperatures (up to 2,400°F or higher). | Lower temperatures compared to vacuum furnaces. |
Contamination Control | Superior control due to the absence of air and reactive gases. | Good control, but may allow trace impurities. |
Applications | High-temperature processes like sintering, annealing, and brazing. | Processes requiring rapid cooling, hardening, and tempering. |
Cost and Maintenance | Higher initial and operating costs; complex vacuum system. | More cost-effective with simpler maintenance. |
Flexibility | Less flexible in cooling options but offers unmatched precision. | More versatile for rapid cooling and lower-temperature treatments. |
Need help choosing the right furnace for your heat treatment process? Contact our experts today!