Batch and continuous furnaces are two distinct types of industrial furnaces used for heat treatment processes, each with unique operational characteristics, advantages, and limitations. Batch furnaces are closed systems where materials are loaded, processed, and unloaded in discrete batches. They are simpler, less expensive, and easier to maintain but require more manual intervention and fixtures like baskets or racks. Continuous furnaces, on the other hand, operate with materials moving through the furnace at a constant speed, maintaining a consistent temperature. They are more complex, expensive, and require frequent maintenance but offer higher efficiency, reduced energy consumption, and eliminate the need for fixtures. The choice between the two depends on factors such as production volume, process requirements, and cost considerations.
Key Points Explained:
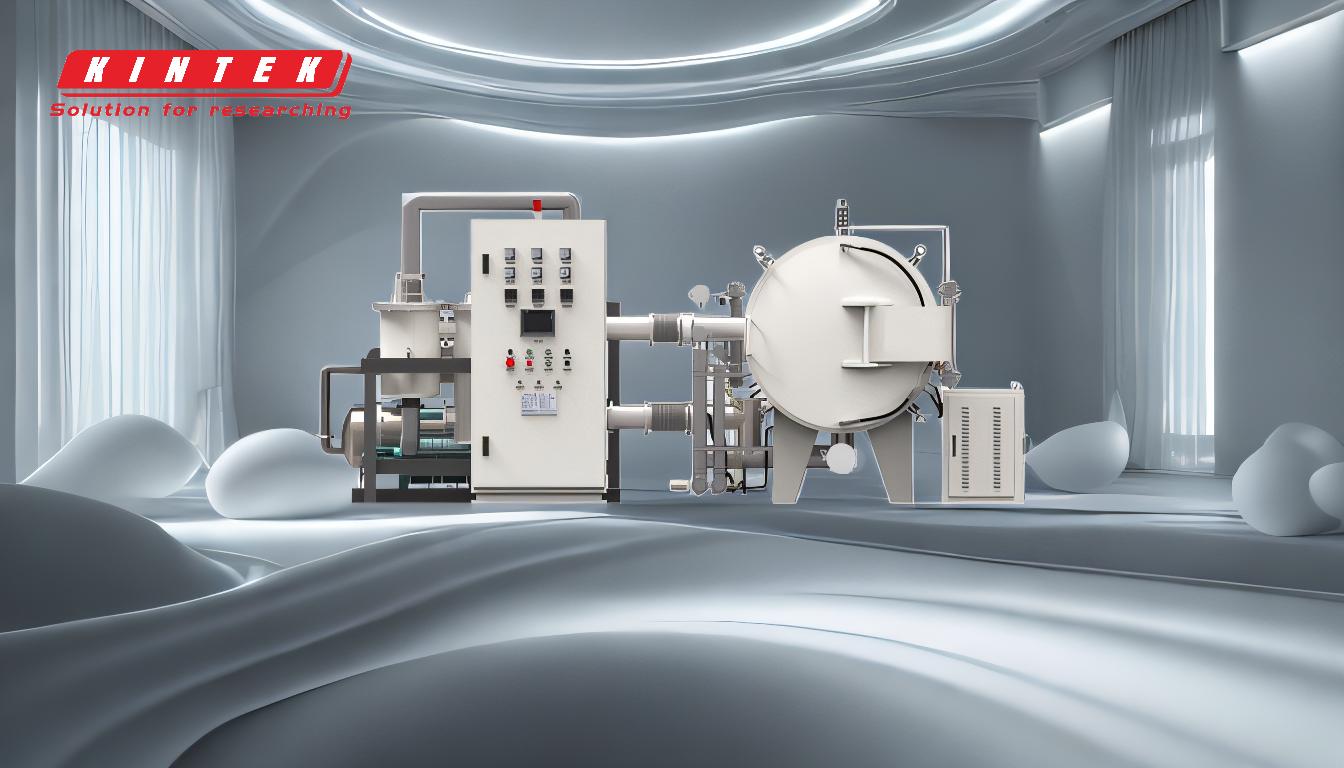
-
Operational Mechanism:
- Batch Furnaces: These are closed systems where materials are loaded in batches, processed, and then unloaded. The furnace is heated to the desired temperature, and the entire batch undergoes the heat treatment simultaneously. This method is suitable for smaller production volumes or specific applications requiring cleanroom standards or inert atmospheres.
- Continuous Furnaces: In continuous furnaces, materials move through the furnace at a constant speed, passing through different temperature zones. This allows for a continuous flow of materials, making it ideal for high-volume production. The consistent temperature and movement eliminate the need for fixtures like racks or baskets.
-
Complexity and Cost:
- Batch Furnaces: These are generally less complex, making them easier to maintain and less expensive both initially and over time. They are well-suited for applications where the production volume does not justify the higher cost and complexity of a continuous furnace.
- Continuous Furnaces: Continuous furnaces are more complex due to their design and the need for precise control over temperature and material flow. This complexity leads to higher initial costs and more frequent maintenance requirements. However, the efficiency and throughput can justify the higher investment for large-scale operations.
-
Maintenance Requirements:
- Batch Furnaces: These require less frequent maintenance due to their simpler design. However, they may need more manual intervention for loading and unloading, which can increase labor costs.
- Continuous Furnaces: The continuous operation and complexity of these furnaces necessitate more frequent maintenance to ensure consistent performance. The need for regular upkeep is a trade-off for the higher efficiency and throughput.
-
Energy Consumption:
- Batch Furnaces: These furnaces may consume more energy per unit of material processed because the entire furnace must be heated and cooled for each batch. This can lead to higher overall energy consumption, especially for smaller batches.
- Continuous Furnaces: Continuous furnaces are generally more energy-efficient because they operate at a constant temperature, reducing the energy required to heat and cool the furnace repeatedly. The continuous flow of materials also allows for better heat utilization.
-
Applications and Suitability:
- Batch Furnaces: Ideal for applications requiring specific environmental conditions, such as cleanroom standards or inert atmospheres. They are also suitable for processes that require varying temperatures or durations for different batches.
- Continuous Furnaces: Best suited for high-volume production where consistent temperature and throughput are critical. They are often used in industries where materials need to be processed continuously, such as in the production of wire mesh or other continuous products.
-
Material Handling:
- Batch Furnaces: Require fixtures like baskets or racks to hold materials during processing. This can add to the complexity of loading and unloading but allows for more flexibility in handling different types of materials.
- Continuous Furnaces: Eliminate the need for fixtures by allowing materials to move through the furnace on a conveyor or other continuous system. This reduces the complexity of material handling but may limit the types of materials that can be processed.
-
Production Volume:
- Batch Furnaces: Suitable for low to medium production volumes where the flexibility to process different materials or batches with varying requirements is more important than high throughput.
- Continuous Furnaces: Designed for high production volumes where the ability to process materials continuously and efficiently is paramount. The continuous operation allows for higher throughput and better utilization of resources.
In summary, the choice between batch and continuous furnaces depends on the specific needs of the production process, including the volume of materials to be processed, the required environmental conditions, and the available budget for initial investment and ongoing maintenance. Batch furnaces offer flexibility and lower costs for smaller-scale operations, while continuous furnaces provide efficiency and high throughput for large-scale production.
Summary Table:
Feature | Batch Furnaces | Continuous Furnaces |
---|---|---|
Operational Mechanism | Closed system; materials processed in discrete batches | Materials move continuously through the furnace at a constant speed |
Complexity & Cost | Less complex, lower initial and maintenance costs | More complex, higher initial and maintenance costs |
Maintenance | Less frequent maintenance but more manual intervention | Frequent maintenance required for consistent performance |
Energy Efficiency | Higher energy consumption per unit due to heating/cooling cycles | More energy-efficient due to constant temperature operation |
Applications | Ideal for low to medium volumes, cleanroom standards, or inert atmospheres | Best for high-volume production requiring consistent temperature and throughput |
Material Handling | Requires fixtures like baskets or racks | Eliminates the need for fixtures, uses conveyors or continuous systems |
Production Volume | Suitable for low to medium production volumes | Designed for high production volumes |
Still unsure which furnace is right for your needs? Contact our experts today for personalized advice!