Heating and sintering are two distinct thermal processes used in metallurgy and material science, each with unique characteristics and applications. Heating is a broad term that refers to raising the temperature of a material, often to achieve specific properties like softening or annealing. Sintering, on the other hand, is a specialized process where powdered materials are compacted and heated below their melting point to form a solid mass. This process relies on atomic diffusion to bond particles, resulting in enhanced mechanical properties without liquefaction. While both processes involve heat, sintering is more energy-efficient and precise, making it ideal for creating complex parts with high melting points and improved strength.
Key Points Explained:
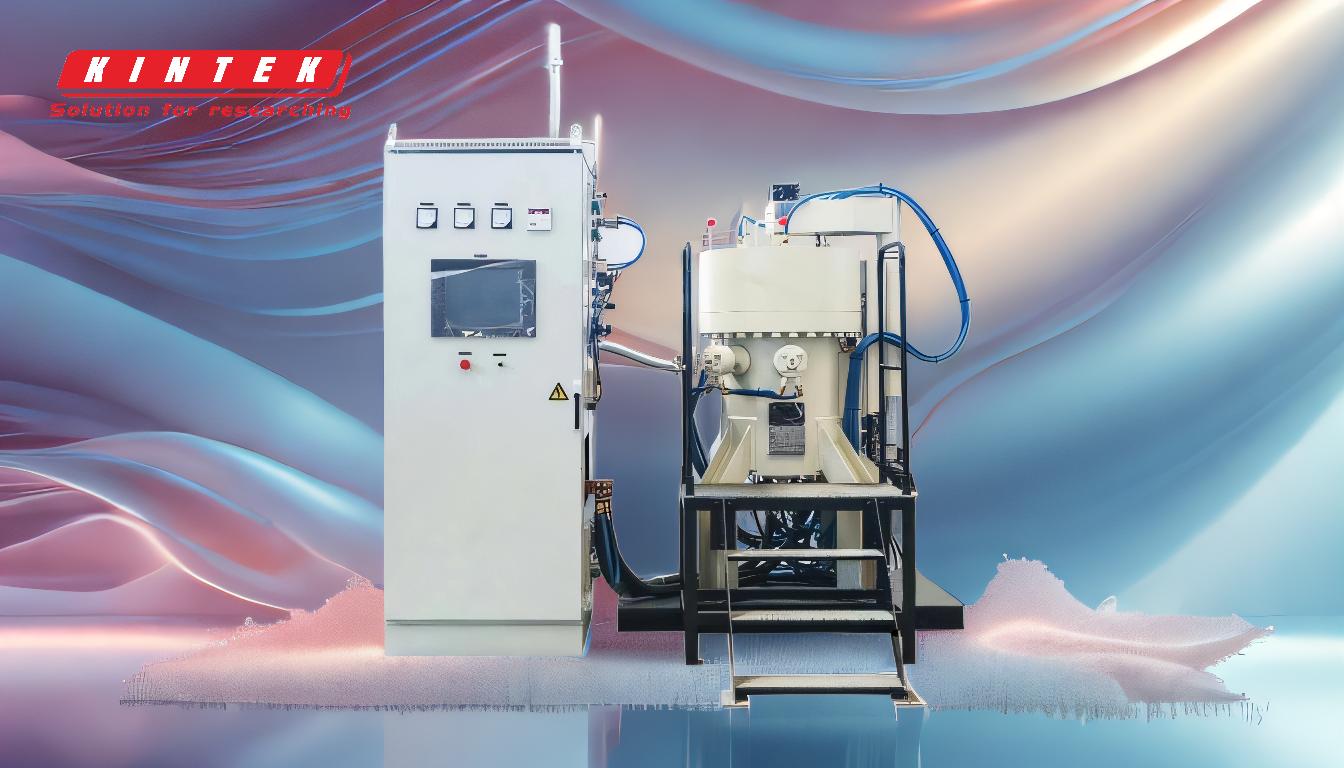
-
Definition and Purpose:
- Heating: A general process of increasing the temperature of a material, often used to alter its physical properties, such as softening or annealing.
- Sintering: A specific process where powdered materials are compacted and heated below their melting point to form a solid mass, enhancing mechanical properties like strength and hardness.
-
Temperature Range:
- Heating: Can involve a wide range of temperatures, depending on the desired outcome (e.g., annealing, melting).
- Sintering: Occurs at temperatures just below the melting point of the material, ensuring particles bond without liquefying.
-
Energy Consumption:
- Heating: May require significant energy, especially if the goal is to melt the material.
- Sintering: More energy-efficient due to the lower temperatures involved, making it a cost-effective alternative to melting.
-
Mechanism of Action:
- Heating: Typically involves a phase change (e.g., solid to liquid in melting) or structural changes (e.g., annealing to reduce hardness).
- Sintering: Relies on atomic diffusion across particle boundaries, leading to bonding and densification without a phase change.
-
Applications:
- Heating: Used in various processes like annealing, tempering, and melting, depending on the material and desired properties.
- Sintering: Commonly used in powder metallurgy to create complex parts with high melting points, improved strength, and controlled porosity.
-
Outcome and Properties:
- Heating: Can result in softened, more malleable materials or completely melted metals, depending on the process.
- Sintering: Produces solid structures with enhanced mechanical properties, such as increased strength and hardness, without the imperfections often associated with melting.
-
Control and Precision:
- Heating: Less precise, especially in processes like melting, which can lead to imperfections.
- Sintering: Offers greater control over the final product, resulting in consistent and high-quality parts.
By understanding these key differences, equipment and consumable purchasers can make informed decisions about which process best suits their needs, whether they require softened materials for further processing or complex, high-strength parts for specific applications.
Summary Table:
Aspect | Heating | Sintering |
---|---|---|
Definition | General process of raising material temperature. | Compacting and heating powdered materials below melting point. |
Temperature Range | Wide range, depending on the process (e.g., annealing, melting). | Below the melting point of the material. |
Energy Consumption | High, especially for melting processes. | More energy-efficient due to lower temperatures. |
Mechanism | Phase changes (e.g., solid to liquid) or structural changes (e.g., annealing). | Atomic diffusion bonds particles without liquefaction. |
Applications | Annealing, tempering, melting. | Powder metallurgy for complex, high-strength parts. |
Outcome | Softened or melted materials. | Solid structures with enhanced strength and hardness. |
Precision | Less precise, may result in imperfections. | High precision, consistent, and high-quality parts. |
Need help choosing the right thermal process for your materials? Contact our experts today!
For more information on electric heating elements, sintering furnaces, or vacuum melting furnaces, visit our topic pages.