RF (Radio Frequency) plasma and DC (Direct Current) plasma are two distinct methods used in sputtering processes, primarily differing in the type of power source and their suitability for different materials. RF plasma uses an alternating current (AC) power source, which allows it to handle insulating (dielectric) materials by preventing charge buildup on the target. This is achieved by alternating the electrical potential, neutralizing positive ions during one half-cycle and sputtering target atoms during the other. In contrast, DC plasma relies on a direct current (DC) power source, making it effective only for conductive materials. DC sputtering struggles with insulating materials due to charge accumulation, which can disrupt the process. Additionally, RF sputtering operates at higher voltages and lower chamber pressures, reducing collisions and improving efficiency for non-conductive materials.
Key Points Explained:
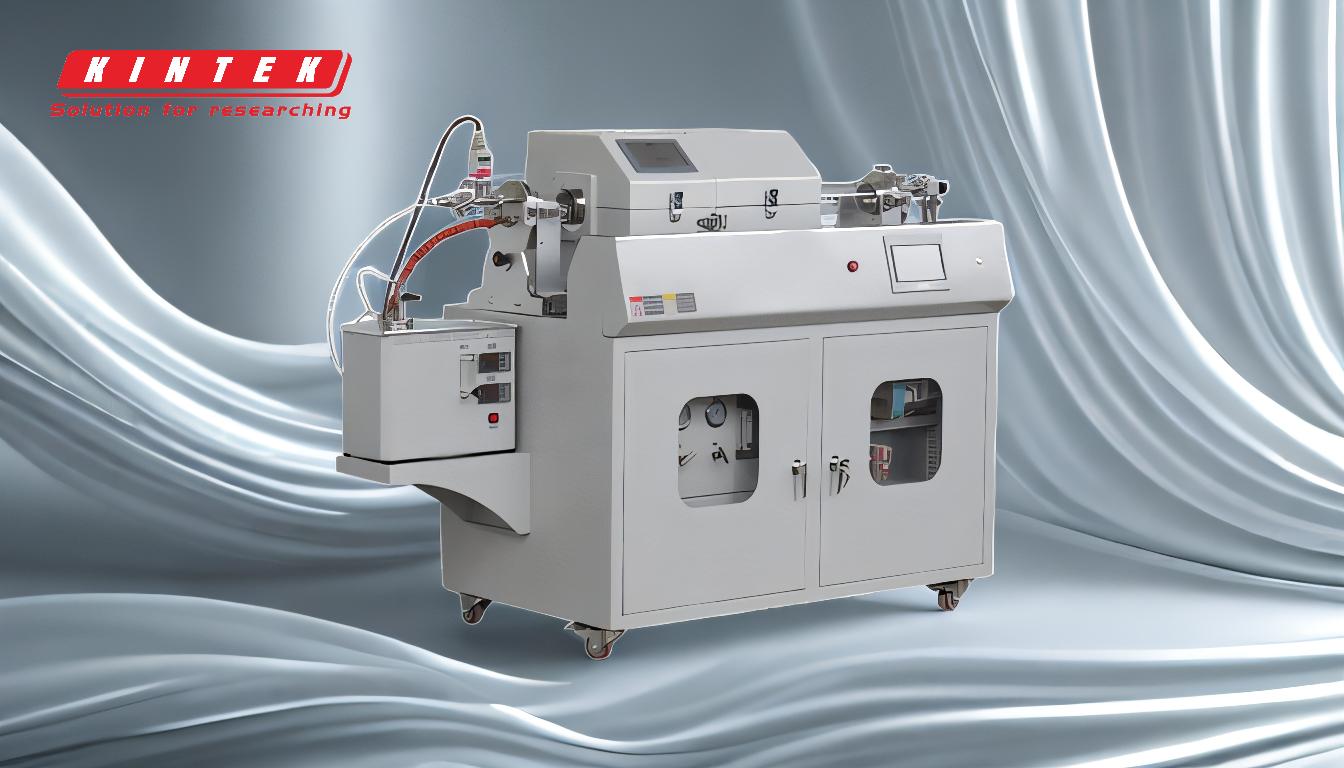
-
Power Source Differences:
- RF Plasma: Uses an alternating current (AC) power source with a frequency in the range of radio waves. The alternating polarity prevents charge buildup on insulating targets, enabling continuous sputtering of dielectric materials.
- DC Plasma: Relies on a direct current (DC) power source. It is effective for conductive materials but struggles with insulating materials due to charge accumulation, which can halt the sputtering process.
-
Material Suitability:
- RF Plasma: Ideal for sputtering insulating (dielectric) materials. The alternating current neutralizes positive ions on the target surface, preventing charge buildup and allowing for consistent sputtering.
- DC Plasma: Limited to conductive materials. Insulating materials cause charge accumulation, leading to arcing and process disruption.
-
Voltage and Pressure Requirements:
- RF Plasma: Operates at higher voltages (1,012 volts or higher) and lower chamber pressures. This reduces collisions in the plasma, improving efficiency and preventing charge buildup on the target.
- DC Plasma: Typically requires voltages between 2,000 and 5,000 volts. It operates at higher chamber pressures, which can lead to more collisions and less efficient sputtering for insulating materials.
-
Mechanism of Sputtering:
- RF Plasma: Alternates the electrical potential, allowing electrons to neutralize positive ions during one half-cycle and sputter target atoms during the other. This alternating process ensures continuous sputtering without charge accumulation.
- DC Plasma: Uses a constant electrical potential, which can lead to charge buildup on insulating materials, causing arcing and interrupting the sputtering process.
-
Applications:
- RF Plasma: Commonly used in applications requiring the deposition of insulating materials, such as oxides, nitrides, and other dielectric films.
- DC Plasma: Primarily used for depositing metallic coatings and other conductive materials.
In summary, RF plasma is more versatile for handling insulating materials due to its alternating current mechanism, while DC plasma is limited to conductive materials. The choice between RF and DC plasma depends on the specific material properties and application requirements.
Summary Table:
Aspect | RF Plasma | DC Plasma |
---|---|---|
Power Source | Alternating Current (AC) | Direct Current (DC) |
Material Suitability | Ideal for insulating (dielectric) materials | Limited to conductive materials |
Voltage Requirements | Higher voltages (1,012V+) | 2,000V to 5,000V |
Chamber Pressure | Lower pressure, reducing collisions | Higher pressure, leading to more collisions |
Mechanism | Alternates electrical potential to prevent charge buildup | Constant electrical potential, prone to charge buildup on insulators |
Applications | Deposition of insulating materials (e.g., oxides, nitrides) | Deposition of metallic coatings and conductive materials |
Need help choosing the right plasma sputtering method for your materials? Contact our experts today!