Sintering is a critical process in materials science, particularly in the production of ceramics, metals, and composites. It involves heating compacted powder materials to temperatures below their melting points, which facilitates particle bonding and densification. The effect of sintering on hardness is significant, as it directly influences the material's mechanical properties. Increasing sintering time and optimizing cooling rates can enhance hardness and strength. Sintering furnaces play a pivotal role in this process, offering precise control over temperature and atmosphere to achieve consistent and desirable material properties.
Key Points Explained:
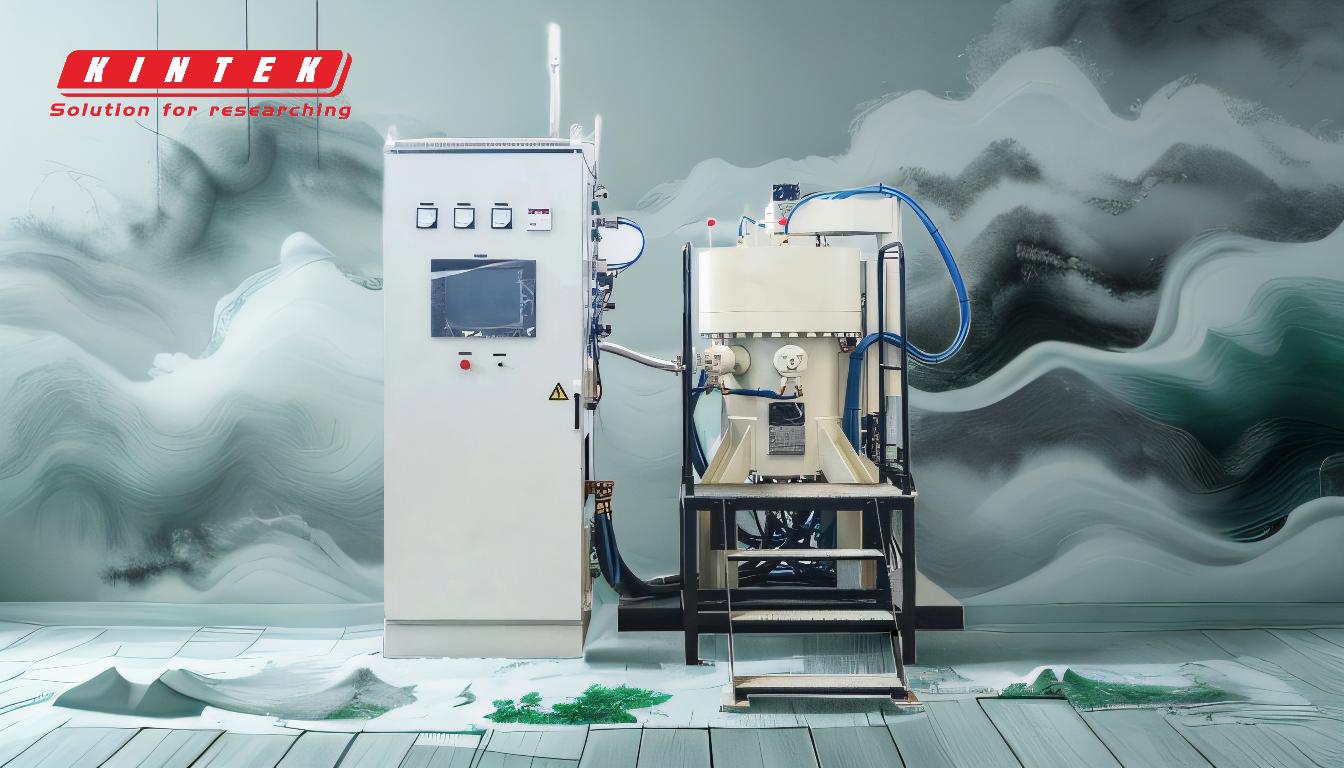
-
Definition and Role of Sintering:
- Sintering is a thermal process where powdered materials are heated to below their melting points, causing particles to bond and densify.
- This process is crucial for enhancing the mechanical properties of materials, such as hardness, strength, and durability.
- Sintering is widely used in industries like ceramics, metallurgy, and powder metallurgy to produce high-performance components.
-
Effect of Sintering on Hardness:
- Increased Sintering Time: Longer sintering durations allow for more thorough particle bonding and densification, leading to increased hardness. This is because extended exposure to heat facilitates the diffusion of atoms, resulting in a more compact and cohesive microstructure.
- Cooling Rate: Faster cooling rates after sintering can also enhance hardness. Rapid cooling helps to lock in the microstructure formed during sintering, preventing grain growth and maintaining a fine-grained structure, which is generally harder.
-
Role of Sintering Furnaces:
- Sintering furnaces are essential for controlling the sintering environment, including temperature, atmosphere, and heating/cooling rates.
- These furnaces use solid-state sintering methods, ensuring that the material is shaped without liquefaction, which is critical for maintaining the desired material properties.
- The precise control offered by sintering furnaces allows for consistent reproduction of results, particularly in terms of size and hardness.
-
Practical Implications:
- Material Selection: The choice of sintering parameters, including time and cooling rate, should be tailored to the specific material and desired properties.
- Process Optimization: Understanding the relationship between sintering conditions and material hardness is crucial for optimizing manufacturing processes and achieving high-quality products.
- Quality Control: Consistent use of sintering furnaces with controlled parameters ensures uniform hardness and strength across batches, which is vital for industrial applications.
-
Future Considerations:
- Advanced Sintering Techniques: Emerging technologies, such as spark plasma sintering and microwave sintering, offer new possibilities for enhancing material properties.
- Material Innovations: Ongoing research into new materials and sintering methods continues to expand the potential applications of sintered products, particularly in high-performance industries like aerospace and automotive.
In summary, sintering significantly impacts the hardness of materials, with increased sintering time and optimized cooling rates leading to enhanced mechanical properties. Sintering furnaces are indispensable in this process, providing the necessary control to achieve consistent and high-quality results. Understanding and optimizing sintering parameters is essential for producing materials with superior hardness and strength.
Summary Table:
Key Factor | Effect on Hardness |
---|---|
Increased Sintering Time | Enhances particle bonding and densification, leading to increased hardness. |
Optimized Cooling Rate | Faster cooling locks in microstructure, preventing grain growth and improving hardness. |
Sintering Furnace Control | Ensures precise temperature and atmosphere control for consistent hardness results. |
Optimize your material hardness with advanced sintering solutions—contact us today to learn more!