Induction melting is a highly efficient process used to heat and melt metals through electromagnetic induction. The efficiency of this process is influenced by several factors, including the design of the induction furnace, the type of metal being melted, and the power supply. Induction melting offers advantages such as rapid heating, precise temperature control, and reduced energy losses compared to traditional melting methods. However, its overall efficiency depends on the specific application and operational conditions.
Key Points Explained:
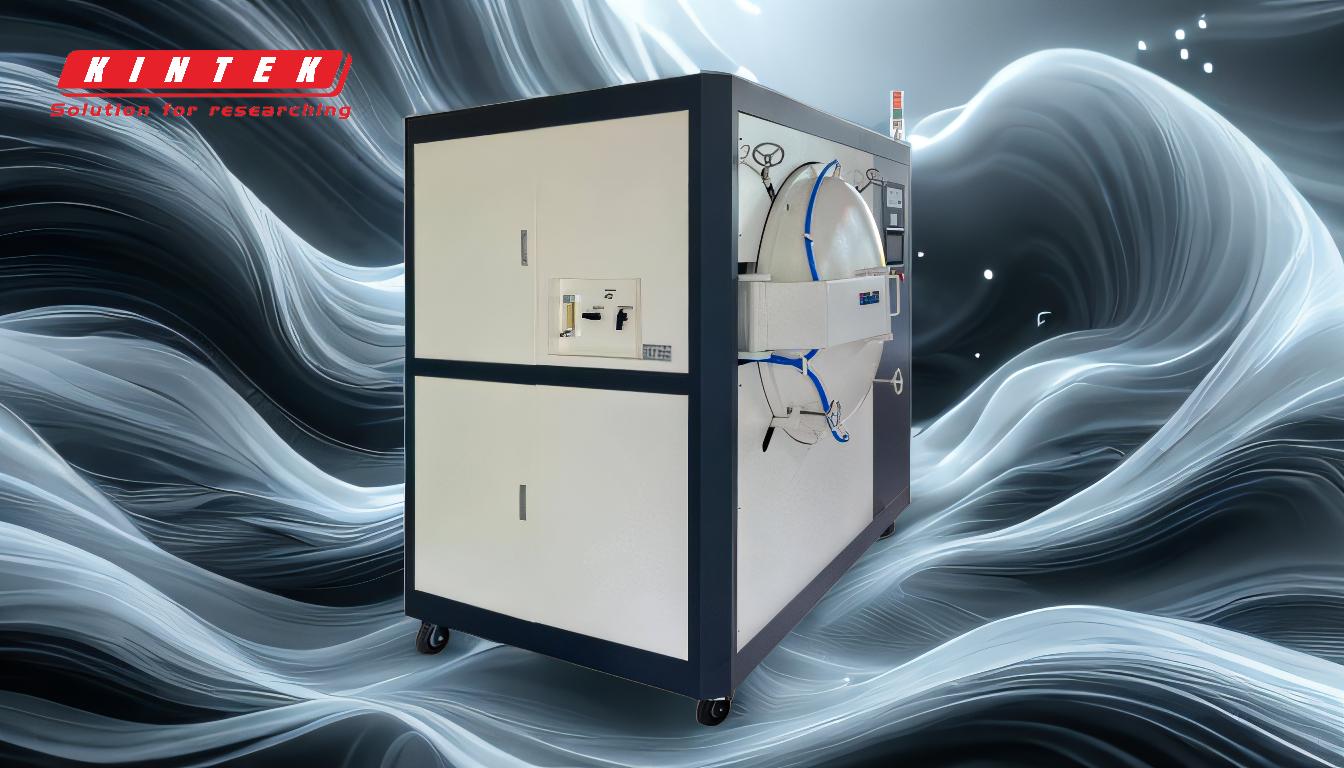
-
Principle of Induction Melting:
- Induction melting works by generating an electromagnetic field within a coil, which induces eddy currents in the conductive metal placed inside the crucible. These eddy currents generate heat due to the metal's electrical resistance, leading to rapid and uniform heating.
- The process is contactless, meaning there is no direct flame or external heat source, which minimizes contamination and energy losses.
-
Factors Affecting Efficiency:
- Power Supply and Frequency: The efficiency of induction melting depends on the frequency of the alternating current used. Higher frequencies are suitable for smaller loads and provide better control, while lower frequencies are more efficient for larger volumes of metal.
- Material Properties: The electrical conductivity and magnetic permeability of the metal being melted play a significant role. Metals with higher conductivity, such as copper and aluminum, heat up more efficiently.
- Furnace Design: The design of the induction furnace, including the coil configuration and crucible material, affects heat transfer and energy utilization. Proper insulation and coil design can minimize energy losses.
-
Advantages of Induction Melting:
- Rapid Heating: Induction melting heats metals quickly, reducing processing time and improving productivity.
- Precise Temperature Control: The process allows for accurate temperature regulation, which is crucial for achieving desired material properties.
- Energy Efficiency: Compared to traditional methods like gas or arc furnaces, induction melting has lower energy losses and higher thermal efficiency.
- Clean and Contaminant-Free: Since there is no direct contact with a flame or combustion gases, the process reduces the risk of contamination.
-
Challenges and Limitations:
- Initial Cost: Induction melting systems require a significant upfront investment in equipment and power supply infrastructure.
- Material Limitations: Not all materials are suitable for induction melting. Non-conductive or poorly conductive materials cannot be effectively heated using this method.
- Energy Consumption: While induction melting is efficient, it still requires a substantial amount of electrical energy, which can be a concern in regions with high electricity costs.
-
Applications and Industry Use:
- Induction melting is widely used in industries such as foundries, jewelry manufacturing, and aerospace for melting metals like steel, iron, aluminum, and precious metals.
- Its efficiency and precision make it ideal for applications requiring high-quality metal casting and alloy production.
In summary, induction melting is a highly efficient and versatile process for melting metals, offering rapid heating, precise control, and reduced energy losses. However, its efficiency depends on factors such as power supply, material properties, and furnace design. While it has some limitations, its advantages make it a preferred choice in many industrial applications.
Summary Table:
Aspect | Details |
---|---|
Principle | Generates heat via electromagnetic induction, creating eddy currents in metal. |
Key Factors | Power supply frequency, material properties, and furnace design. |
Advantages | Rapid heating, precise temperature control, energy efficiency, and cleanliness. |
Challenges | High initial cost, material limitations, and energy consumption. |
Applications | Foundries, jewelry manufacturing, aerospace, and alloy production. |
Discover how induction melting can optimize your metal processing—contact us today!