The firing temperature of alumina, a key parameter in its processing, is typically around 1350°C for achieving high-density and fine-grained structures, as evidenced by the reference stating that pure alumina powder compacts fired at this temperature for 20 minutes achieve 99% of the theoretical density with a grain size of 1.2 μm. Alumina, or aluminum oxide (Al2O3), is a versatile ceramic material known for its high-temperature resistance, mechanical strength, and chemical stability, making it suitable for demanding industrial applications. While its melting point is around 2000°C, the firing temperature is lower, as it is optimized for sintering and densification during processing. This temperature ensures the material's structural integrity and desired properties, such as wear resistance, thermal conductivity, and corrosion resistance, which are critical for applications like crucibles, electrical insulators, and high-temperature components.
Key Points Explained:
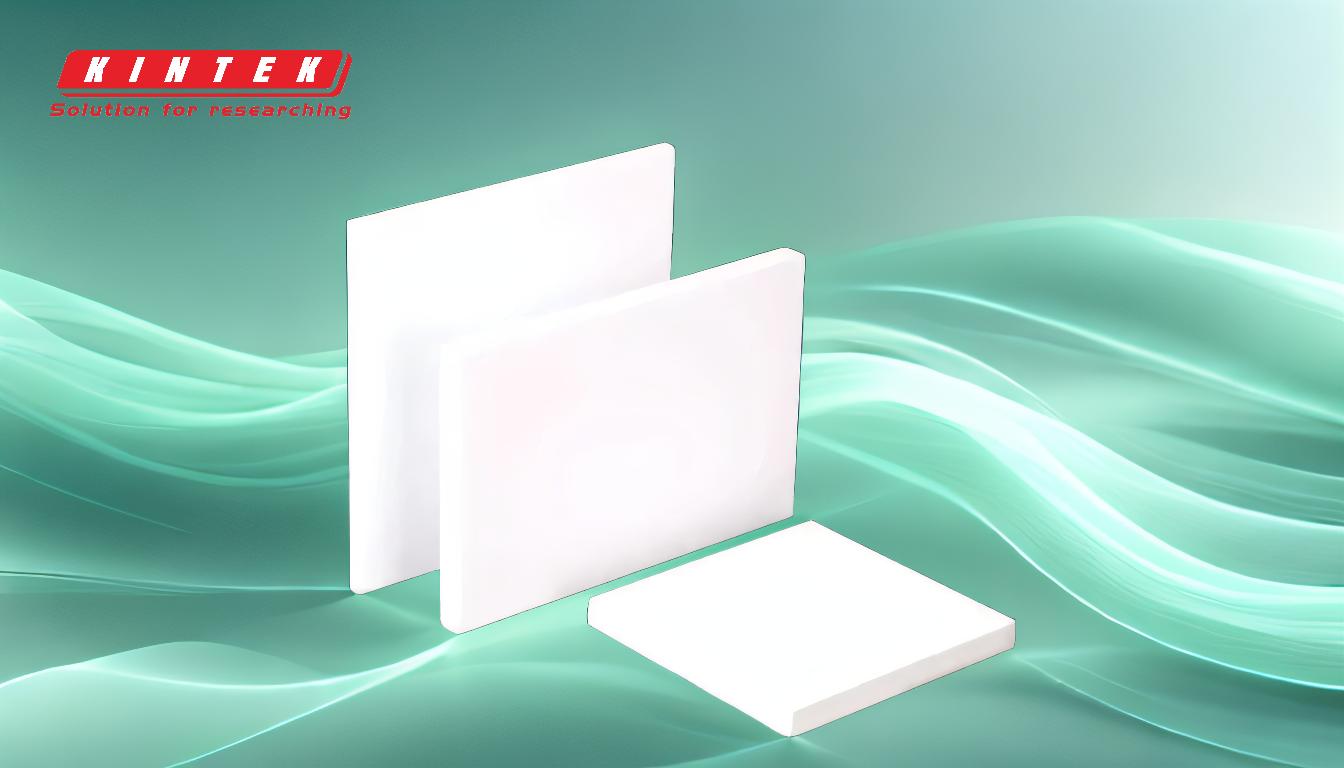
-
Firing Temperature of Alumina:
- The firing temperature for alumina is typically 1350°C, as demonstrated in the reference where pure alumina powder compacts achieve 99% of the theoretical density and a grain size of 1.2 μm when fired at this temperature for 20 minutes.
- This temperature is crucial for sintering, a process that densifies the material by bonding particles together without melting them completely.
-
Alumina's High-Temperature Properties:
- Alumina is known for its high-temperature stability, with a melting point of approximately 2000°C. This makes it suitable for applications requiring resistance to extreme heat.
- Its thermal conductivity (about 3000 W/m·K) and thermal expansion coefficient allow it to withstand high internal pressures and thermal shocks, making it ideal for use in crucibles and other high-temperature environments.
-
Importance of Firing Temperature in Processing:
- The firing temperature is lower than the melting point to ensure proper sintering and densification. At 1350°C, alumina achieves optimal density and grain structure, which are critical for its mechanical and thermal properties.
- Overheating or underheating during firing can lead to defects such as porosity or incomplete densification, compromising the material's performance.
-
Applications of Alumina:
- Alumina's high-temperature resistance and mechanical strength make it suitable for crucibles, electrical insulators, and components in high-temperature furnaces.
- Its chemical resistance and bio-inertness also make it ideal for use in corrosive environments and medical applications.
-
Comparison with Other Materials:
- Alumina is harder than materials like iron or graphite, with superior wear resistance and thermal conductivity. This makes it a preferred choice for demanding industrial applications.
- Its high thermal expansion coefficient allows it to handle thermal stresses better than many other ceramics.
-
Natural Occurrence and Processing:
- Alumina is derived from aluminum oxide, which constitutes about 15% of the Earth's crust. It is extracted from naturally occurring minerals and refined into ceramic materials through processes like sintering at controlled temperatures.
By understanding the firing temperature and its role in alumina's processing, manufacturers can optimize the material's properties for specific applications, ensuring durability and performance in high-temperature and corrosive environments.
Summary Table:
Key Aspect | Details |
---|---|
Firing Temperature | 1350°C for 20 minutes achieves 99% theoretical density and 1.2 μm grain size |
Melting Point | ~2000°C |
Key Properties | High-temperature stability, wear resistance, thermal conductivity |
Applications | Crucibles, electrical insulators, high-temperature components |
Processing Importance | Ensures sintering, densification, and structural integrity |
Optimize your alumina processing—contact our experts today!