Sintering is a thermal process used to transform powdered materials, such as metals or ceramics, into solid, dense, and durable components without melting the material. By heating the powder below its melting point in a controlled environment, sintering enables atomic diffusion, which bonds particles together, reduces porosity, and enhances mechanical properties like strength and durability. This process is widely used in manufacturing to produce complex parts with precise dimensions and tailored properties, making it essential in industries such as automotive, aerospace, and electronics.
Key Points Explained:
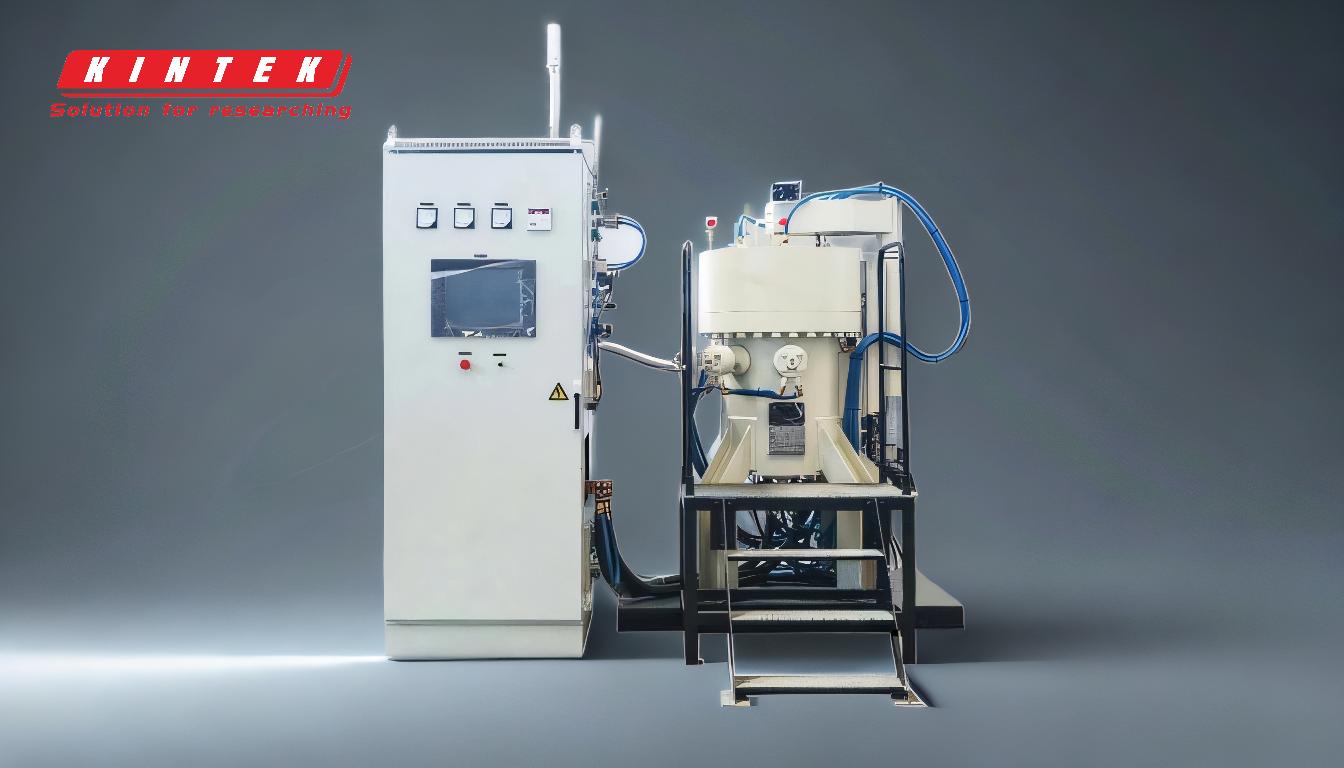
-
Definition and Purpose of Sintering:
- Sintering is a heat treatment process that transforms powdered materials into solid, dense components by heating them below their melting point.
- The primary purpose is to bond particles together, reduce porosity, and improve mechanical properties such as strength, durability, and dimensional stability.
-
How Sintering Works:
- Atomic Diffusion: At elevated temperatures, atoms in the powder particles diffuse across particle boundaries, fusing them together.
- Controlled Environment: Sintering occurs in a controlled atmosphere furnace to prevent oxidation and ensure proper bonding.
- Temperature Range: The process is conducted at temperatures slightly below the material's melting point to avoid liquefaction while enabling atomic movement.
-
Stages of Sintering:
- Initial Stage: Particles begin to bond at contact points, forming necks between them.
- Intermediate Stage: Pores between particles start to shrink, and the material becomes denser.
- Final Stage: The material reaches its maximum density, and the part achieves its final dimensions and mechanical properties.
-
Benefits of Sintering:
- Improved Mechanical Properties: Sintering enhances strength, hardness, and wear resistance.
- Dimensional Precision: The process allows for minor shrinkage, which is accounted for during the design phase, ensuring accurate final dimensions.
- Cost-Effectiveness: Sintering is efficient and reduces material waste, making it economical for mass production.
- Versatility: It can be applied to a wide range of materials, including metals, ceramics, and plastics.
-
Applications of Sintering:
- Industrial Components: Used to manufacture gears, bearings, pulleys, rotors, and sprockets.
- Electronics: Produces electrical contacts and armatures.
- Ceramics: Creates high-strength ceramic parts for aerospace and medical applications.
- Automotive: Used for engine components and other high-performance parts.
-
Factors Influencing Sintering:
- Temperature and Time: Higher temperatures and longer sintering times generally improve bonding and density.
- Atmosphere: The furnace atmosphere must be controlled to prevent oxidation or contamination.
- Powder Characteristics: Particle size, shape, and distribution affect the sintering process and final properties.
-
Comparison to Other Manufacturing Processes:
- Unlike melting, sintering does not liquefy the material, preserving its original composition and reducing energy consumption.
- Compared to traditional machining, sintering allows for the production of complex shapes with minimal material waste.
By understanding these key points, equipment and consumable purchasers can evaluate the suitability of sintering for their specific needs, ensuring they select the right materials and processes for their applications.
Summary Table:
Aspect | Details |
---|---|
Definition | Heat treatment process transforming powders into solid, dense components. |
Key Benefits | Improved strength, dimensional precision, cost-effectiveness, versatility. |
Stages | Initial bonding, intermediate densification, final property enhancement. |
Applications | Industrial components, electronics, ceramics, automotive parts. |
Influencing Factors | Temperature, time, atmosphere, powder characteristics. |
Discover how sintering can optimize your manufacturing process—contact our experts today!