The heat transfer in a muffle furnace is a critical aspect of its operation, as it determines how efficiently the furnace can heat materials to the desired temperatures. The furnace primarily relies on electric resistance heating, where electrical energy is converted into heat and transferred to the workpiece. The design of the muffle furnace, including its insulation, heating elements, and chamber structure, plays a significant role in ensuring effective heat transfer. Factors such as furnace size, power availability, and material construction also influence the heat transfer process. Understanding these elements helps in optimizing the furnace's performance for specific applications, such as material testing or heat treatment.
Key Points Explained:
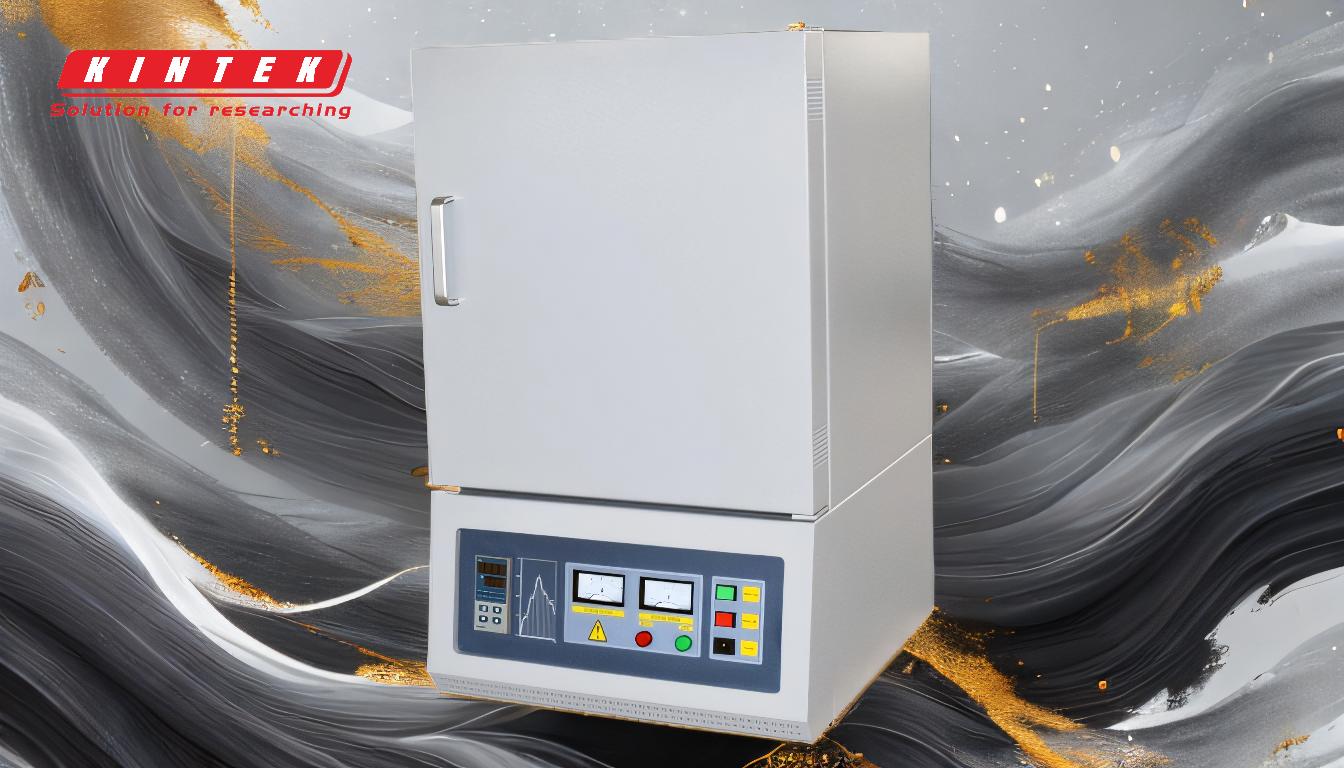
-
Working Principle of Heat Transfer:
- The muffle furnace operates on the principle of electric resistance heating. Electrical energy is converted into heat by the heating elements, which is then transferred to the workpiece.
- The law of conservation of energy ensures that the heat generated is effectively utilized within the furnace chamber.
-
Design and Construction:
- Muffle furnaces are typically barrel-shaped and constructed from high-temperature-resistant materials. This design helps in maintaining high temperatures and ensuring efficient heat transfer.
- The heating elements are often placed inside firebricks or within the insulation, allowing heat to be transferred to the inner chamber through the walls.
-
Temperature Control and Consistency:
- Modern muffle furnaces use electric heating elements, which provide greater temperature control and consistency compared to older combustion-based designs.
- The separate combustion and heating chambers in older designs were gas-sealed to prevent contamination, but electric designs eliminate combustion byproducts entirely.
-
Factors Affecting Heat Transfer:
- Supply Voltage: Adequate voltage is necessary to ensure the heating elements can generate sufficient heat.
- Heating Element Condition: Worn or damaged heating elements can reduce heat transfer efficiency.
- Furnace Chamber Size and Structure: Larger chambers may require more energy to achieve the same temperature, while the structure affects heat distribution.
- Temperature Controller Precision: Accurate temperature control ensures consistent heat transfer.
- Furnace Chamber Sealing: Proper sealing prevents heat loss and maintains temperature consistency.
- Insulation Quality: High-quality insulation minimizes heat loss and improves efficiency.
- Load Condition: The amount and type of material being heated can affect heat transfer rates.
- Thermocouple Accuracy: Accurate temperature measurement is crucial for effective heat management.
- Furnace Door Sealing: A well-sealed door prevents heat escape and contamination.
- Operational Practices: Proper operation, including avoiding frequent door opening and minimizing dust accumulation, helps maintain efficient heat transfer.
-
Applications and Importance of Heat Transfer:
- Muffle furnaces are used in laboratories for high-temperature processes such as ash content testing in rubber and polymer materials.
- Effective heat transfer ensures that materials are heated uniformly and to the required temperatures, which is crucial for accurate experimental results and material properties analysis.
-
Historical and Modern Adaptations:
- Historically, muffle furnaces had separate combustion and heating chambers to prevent contamination. With the advent of electric heating elements in the mid-1950s, most furnaces were converted to electric, enhancing heat transfer efficiency and control.
- Modern electric muffle furnaces offer greater flexibility and adaptability, making them suitable for a wide range of high-temperature applications.
Understanding these key points helps in selecting and operating a muffle furnace effectively, ensuring optimal heat transfer and performance for specific laboratory or industrial needs.
Summary Table:
Key Aspect | Details |
---|---|
Working Principle | Electric resistance heating converts electrical energy into heat. |
Design Features | Barrel-shaped, high-temperature-resistant materials, and insulated walls. |
Temperature Control | Electric heating elements ensure precise and consistent temperature control. |
Factors Affecting Efficiency | Supply voltage, heating element condition, insulation quality, and more. |
Applications | Used in labs for ash content testing, material analysis, and heat treatment. |
Modern Adaptations | Electric designs eliminate combustion byproducts, enhancing efficiency. |
Optimize your lab's heat transfer efficiency with a muffle furnace—contact us today for expert advice!