The heating rate for alumina depends on the specific application and the type of furnace being used. Generally, the recommended heating rate for alumina furnace tubes is 5-10°C/min, with a preference for 5°C/min to avoid thermal shock and ensure uniform sintering. Cooling rates should also be controlled, ideally below 10°C/min, with 5°C/min being optimal. Rapid temperature changes can cause thermal stress, leading to breakage or insufficient sintering. For initial heating, a slower rate of 150-300°C per hour is advised to minimize thermal shock. These guidelines ensure the longevity and performance of alumina components in high-temperature environments.
Key Points Explained:
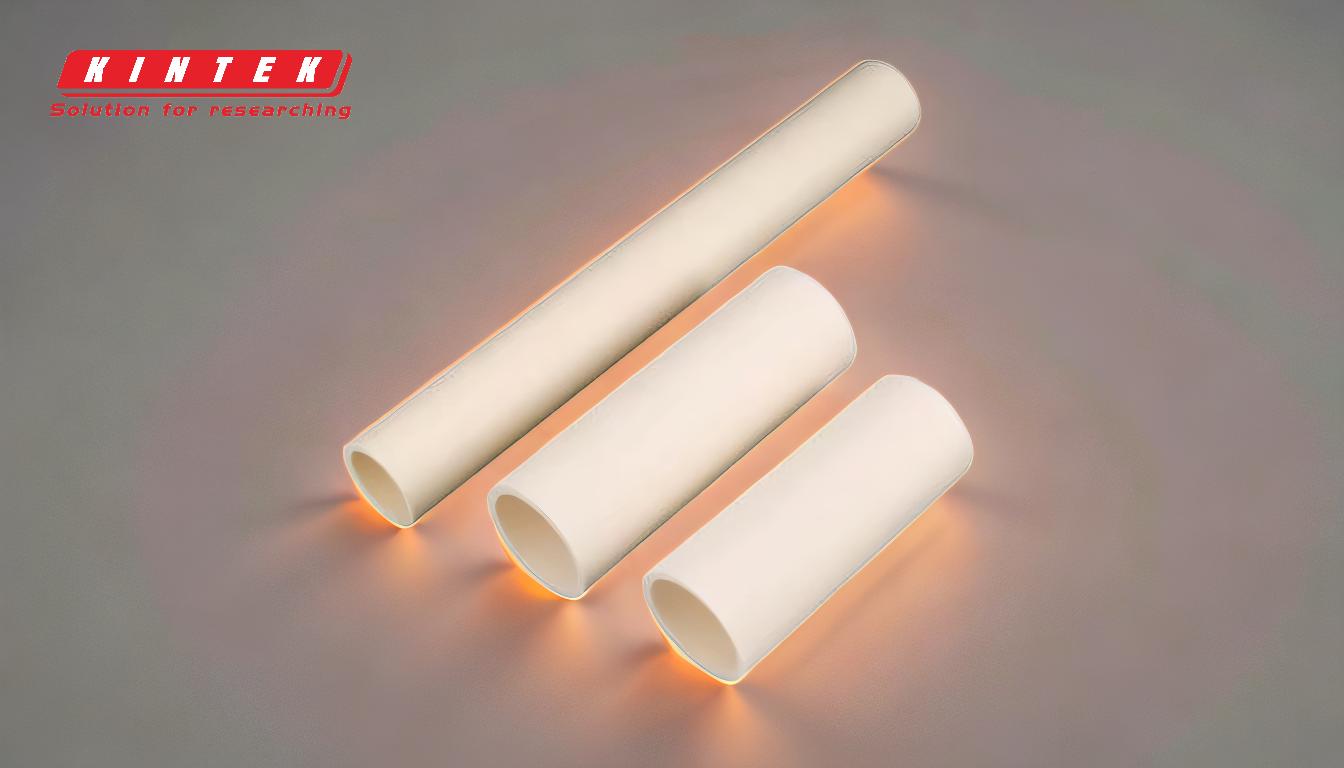
-
Recommended Heating Rate for Alumina:
- The standard heating rate for alumina furnace tubes is 5-10°C/min, with 5°C/min being the preferred rate. This ensures uniform heating and minimizes the risk of thermal shock.
- A slower heating rate of 150-300°C per hour is recommended for the first 1-1.5 hours to reduce thermal shock, especially during the initial warm-up phase.
-
Importance of Controlled Heating:
- Excessive heating rates (above 10°C/min) can lead to insufficient sintering and uneven sintering degrees across the material. This results in high-temperature melting peaks and increased crystallinity, which can compromise the structural integrity of the alumina.
- Controlled heating ensures uniform sintering and prevents internal stresses that could lead to cracking or breakage.
-
Cooling Rate Considerations:
- The cooling rate should be below 10°C/min, with 5°C/min being ideal. Rapid cooling can cause thermal shock, leading to material failure.
- Gradual cooling is essential to maintain the structural integrity of alumina, especially after high-temperature treatments.
-
Thermal Shock Sensitivity:
- Alumina is highly sensitive to thermal shock due to its brittleness. Rapid temperature changes can cause cracks or breakage.
- A slower heating and cooling rate (e.g., 150-300°C per hour for heating and 75-150°C per hour for cooling) is recommended to mitigate this risk.
-
Application-Specific Recommendations:
- For alumina furnace tubes, the heating and cooling rates should align with the furnace's design and operational requirements. Natural cooling after heat treatment should be avoided, as it can cause rapid temperature drops and potential damage.
- In rotary tube furnaces, factors such as inclination angle, rotational speed, tube length, and material flow properties influence the heat treatment process. Adjusting these parameters can help maintain optimal heating and cooling rates.
-
Material Properties and Durability:
- Alumina has excellent thermal shock resistance, high density, and resistance to acid, alkali, and erosion. These properties make it suitable for high-temperature applications (up to 1800°C).
- Proper heating and cooling rates ensure the material's durability and extend its service life.
-
Practical Tips for Equipment Users:
- Always set a controlled cooling rate in the furnace program; avoid stopping the program abruptly at high temperatures.
- Use gradual temperature changes to prevent thermal stress and ensure consistent material performance.
- Monitor the heating and cooling process closely, especially during the initial warm-up and final cooling phases.
By adhering to these guidelines, users can optimize the performance and longevity of alumina components in high-temperature environments, ensuring consistent results and minimizing the risk of material failure.
Summary Table:
Parameter | Recommendation |
---|---|
Heating Rate | 5-10°C/min (preferably 5°C/min) |
Initial Heating Rate | 150-300°C per hour for the first 1-1.5 hours |
Cooling Rate | Below 10°C/min (ideally 5°C/min) |
Thermal Shock Sensitivity | Avoid rapid temperature changes to prevent cracks and breakage |
Key Benefit | Ensures uniform sintering, durability, and longevity in high-temperature environments |
Need help optimizing your alumina heat treatment process? Contact our experts today for tailored solutions!