Hot isostatic pressing (HIP) is a manufacturing process that has evolved significantly since its inception, offering a wide range of benefits in material densification and property enhancement. The history of HIP is rooted in the need to address the limitations of traditional hot pressing methods, leading to the development of a technology that applies uniform pressure and temperature to materials, resulting in improved mechanical properties and reduced defects. This process has become essential in industries requiring high-performance materials, such as aerospace, automotive, and medical devices.
Key Points Explained:
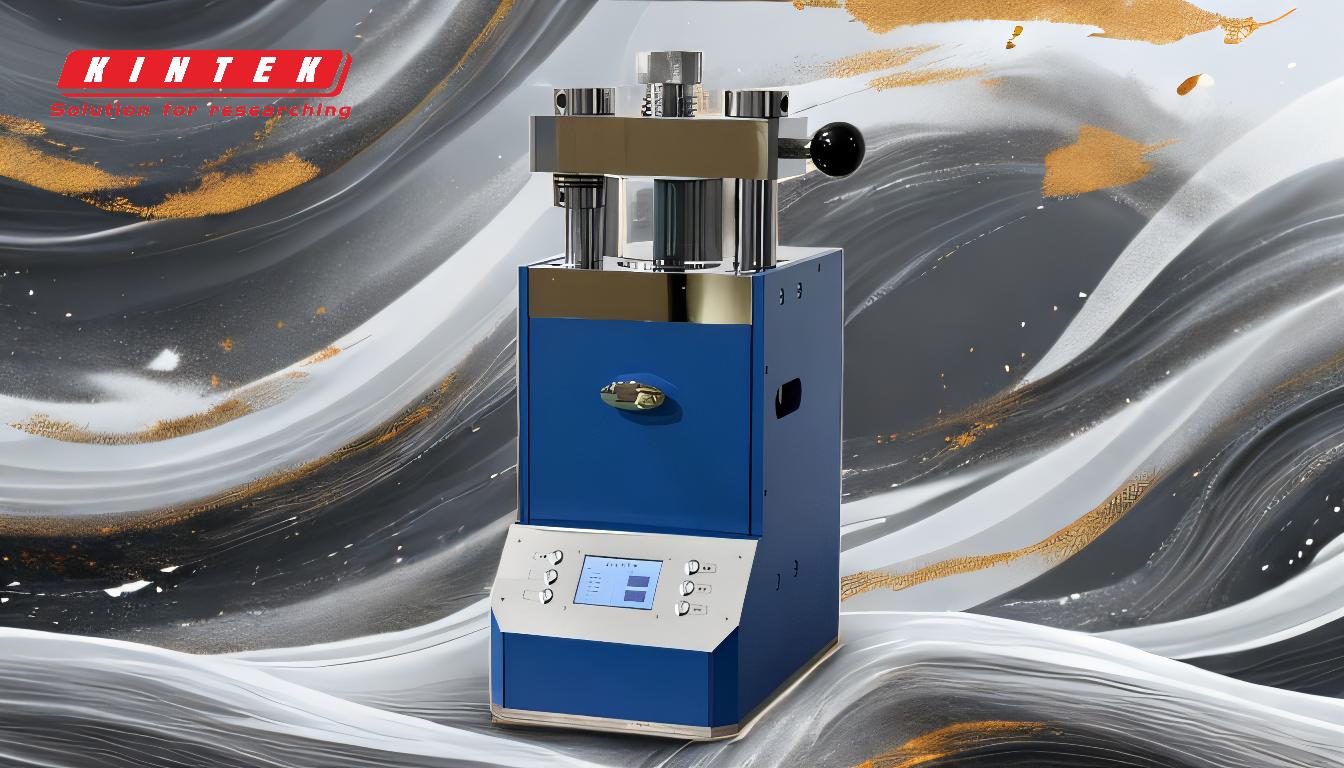
-
Origins and Evolution of Hot Isostatic Pressing:
- The concept of isostatic pressing originated from the need to apply uniform pressure to materials without altering their shape. Early developments focused on creating a process that could consolidate powder particles, heal voids, and improve material density.
- The introduction of the cylindrical chamber in HIP equipment was a significant advancement, ensuring uniform pressure distribution and enabling the processing of various materials and shapes.
-
Key Advantages of HIP Technology:
- Increased Density: HIP significantly increases the density of materials, leading to stronger and more durable products.
- Improved Mechanical Properties: The process enhances properties such as ductility, toughness, and fatigue resistance.
- Defect Repair: HIP can repair internal porosity and other defects, improving the overall quality of the material.
- Material Bonding: The technology allows for the formation of metallurgical bonds between different materials, expanding its application in composite materials.
-
Development of Equilibrium and Isostatic Hot Pressing:
- The evolution of HIP addressed some of the drawbacks of traditional hot pressing, such as uneven pressure distribution and limited material densification.
- The development of equilibrium and isostatic hot pressing techniques has further refined the process, making it more efficient and versatile.
-
Applications of HIP in Various Industries:
- Aerospace: HIP is used to produce high-strength components for aircraft and spacecraft, where material integrity is critical.
- Medical Devices: The process is employed to manufacture implants and prosthetics with superior mechanical properties and biocompatibility.
- Automotive: HIP enhances the performance of engine components and other critical parts, contributing to lighter and more efficient vehicles.
-
Future Trends and Innovations:
- Ongoing research and development in HIP technology focus on improving process efficiency, reducing energy consumption, and expanding the range of materials that can be processed.
- Innovations such as warm isostatic press are being explored to further enhance the capabilities of HIP, offering new possibilities in material science and manufacturing.
In conclusion, the history of hot isostatic pressing reflects a continuous journey of innovation and improvement, driven by the need for high-performance materials in advanced industries. The technology has evolved from its early stages to become a critical process in modern manufacturing, offering unparalleled benefits in material densification and property enhancement. As research and development continue, HIP is poised to play an even more significant role in shaping the future of material science and engineering.
Summary Table:
Key Aspect | Details |
---|---|
Origins | Developed to apply uniform pressure, consolidate powders, and heal defects. |
Key Advancements | Introduction of cylindrical chambers for uniform pressure distribution. |
Advantages | Increased density, improved mechanical properties, defect repair, bonding. |
Applications | Aerospace, medical devices, automotive. |
Future Trends | Improved efficiency, reduced energy use, and expanded material range. |
Learn how hot isostatic pressing can revolutionize your manufacturing process—contact our experts today!