An inert atmosphere for welding is a controlled environment where reactive gases like oxygen are replaced with non-reactive gases to prevent oxidation, contamination, or other unwanted chemical reactions during the welding process. Commonly used inert gases include argon, nitrogen, and helium, each chosen based on their properties and the specific welding application. Argon is particularly favored for its ability to shield the weld pool effectively, while nitrogen is used for its high diffusion rate and cost-effectiveness. Helium is often used for its high thermal conductivity, which is beneficial in certain welding scenarios. The choice of gas depends on the material being welded, the welding technique, and the desired outcome.
Key Points Explained:
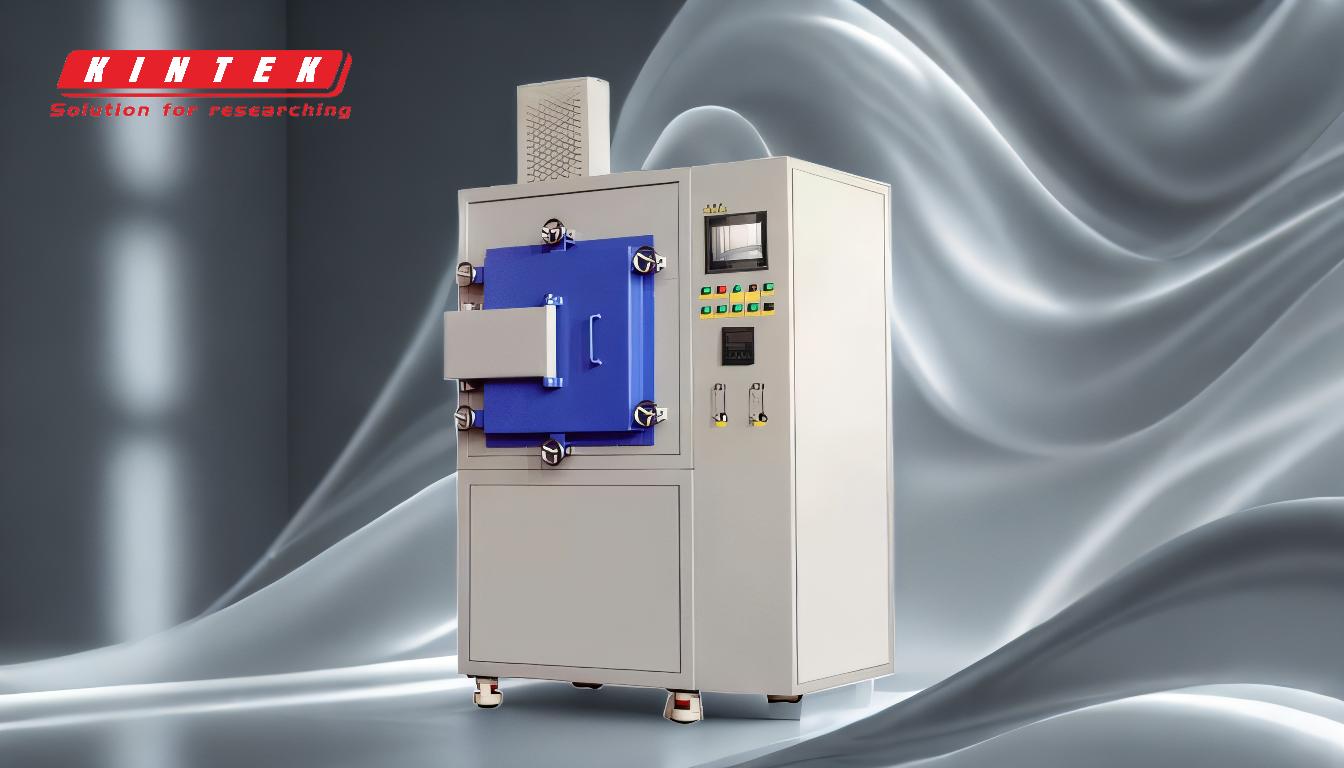
-
Definition of an Inert Atmosphere in Welding:
- An inert atmosphere in welding refers to an environment where reactive gases, particularly oxygen, are replaced with non-reactive gases. This prevents oxidation, contamination, and other chemical reactions that could degrade the quality of the weld.
-
Common Gases Used for Inert Atmospheres:
- Argon (Ar): Argon is one of the most commonly used inert gases in welding due to its excellent shielding properties. It is chemically inert, meaning it does not react with molten metals, making it ideal for protecting the weld pool from contamination.
- Nitrogen (N2): Nitrogen is another widely used inert gas, particularly in processes where cost is a concern. It has a high diffusion rate, which helps in quickly displacing oxygen from the welding environment. However, it is not suitable for all materials, as it can react with certain metals at high temperatures.
- Helium (He): Helium is often used in welding applications that require higher heat input due to its high thermal conductivity. It is particularly useful in welding thick materials or in processes like TIG (Tungsten Inert Gas) welding.
-
Applications of Inert Atmospheres in Welding:
- TIG Welding: In TIG welding, argon is commonly used to shield the tungsten electrode and the weld pool. The inert atmosphere prevents contamination and ensures a clean, high-quality weld.
- MIG Welding: In MIG (Metal Inert Gas) welding, a mixture of argon and carbon dioxide is often used to create an inert atmosphere. The argon provides the primary shielding, while the carbon dioxide helps stabilize the arc.
- Laser Welding: In laser welding, inert gases like argon or nitrogen are used to protect the weld pool from oxidation and other atmospheric contaminants. The choice of gas depends on the material being welded and the specific requirements of the process.
-
Benefits of Using an Inert Atmosphere:
- Prevents Oxidation: By replacing oxygen with inert gases, the risk of oxidation is minimized, leading to stronger and more durable welds.
- Reduces Contamination: Inert atmospheres help prevent contamination from atmospheric gases, dust, and other particles, ensuring a cleaner weld.
- Improves Weld Quality: The use of inert gases can significantly improve the quality of the weld by providing a stable and controlled environment, reducing defects such as porosity and inclusions.
-
Considerations When Choosing an Inert Gas:
- Material Compatibility: The choice of inert gas should be compatible with the material being welded. For example, nitrogen is not suitable for welding stainless steel, as it can cause nitriding, which weakens the material.
- Cost: The cost of the inert gas is also a consideration. Argon is more expensive than nitrogen, so in some applications, nitrogen may be preferred for cost reasons.
- Welding Technique: The welding technique being used will also influence the choice of inert gas. For example, TIG welding typically requires argon, while MIG welding may use a mixture of argon and carbon dioxide.
-
Safety Considerations:
- Ventilation: When using inert gases, proper ventilation is essential to prevent the buildup of gases, which can displace oxygen and pose a risk of asphyxiation.
- Explosion Risks: In some cases, hydrogen may be used as part of the inert atmosphere, particularly in high-temperature applications. However, hydrogen is highly explosive, so special safety precautions, such as explosion-proof equipment, must be in place.
In summary, an inert atmosphere for welding is crucial for achieving high-quality welds by preventing oxidation and contamination. The choice of inert gas—whether argon, nitrogen, or helium—depends on the material, welding technique, and specific application requirements. Proper safety measures must also be taken to ensure a safe working environment when using these gases.
Summary Table:
Key Aspect | Details |
---|---|
Definition | Replaces reactive gases (e.g., oxygen) with non-reactive gases (e.g., argon). |
Common Gases | Argon (best shielding), Nitrogen (cost-effective), Helium (high heat input). |
Applications | TIG, MIG, and Laser Welding. |
Benefits | Prevents oxidation, reduces contamination, improves weld quality. |
Safety Considerations | Proper ventilation and explosion-proof equipment are essential. |
Need expert advice on choosing the right inert gas for your welding process? Contact us today for personalized solutions!