The inside material of a muffle furnace primarily consists of ceramic-based materials designed to withstand high temperatures and resist chemical corrosion. The inner chamber, or heating zone, is typically constructed using materials like ceramic tiles, zirconia boards, or high alumina bricks, depending on the temperature requirements. These materials ensure durability, effective heat transfer, and resistance to deformation under extreme heat. Additionally, the fire-door and box panel linings are often made of stainless steel for corrosion resistance. The choice of materials depends on the furnace's intended use and temperature range, with options for refractory-brick or ceramic-fiber chambers for enhanced durability.
Key Points Explained:
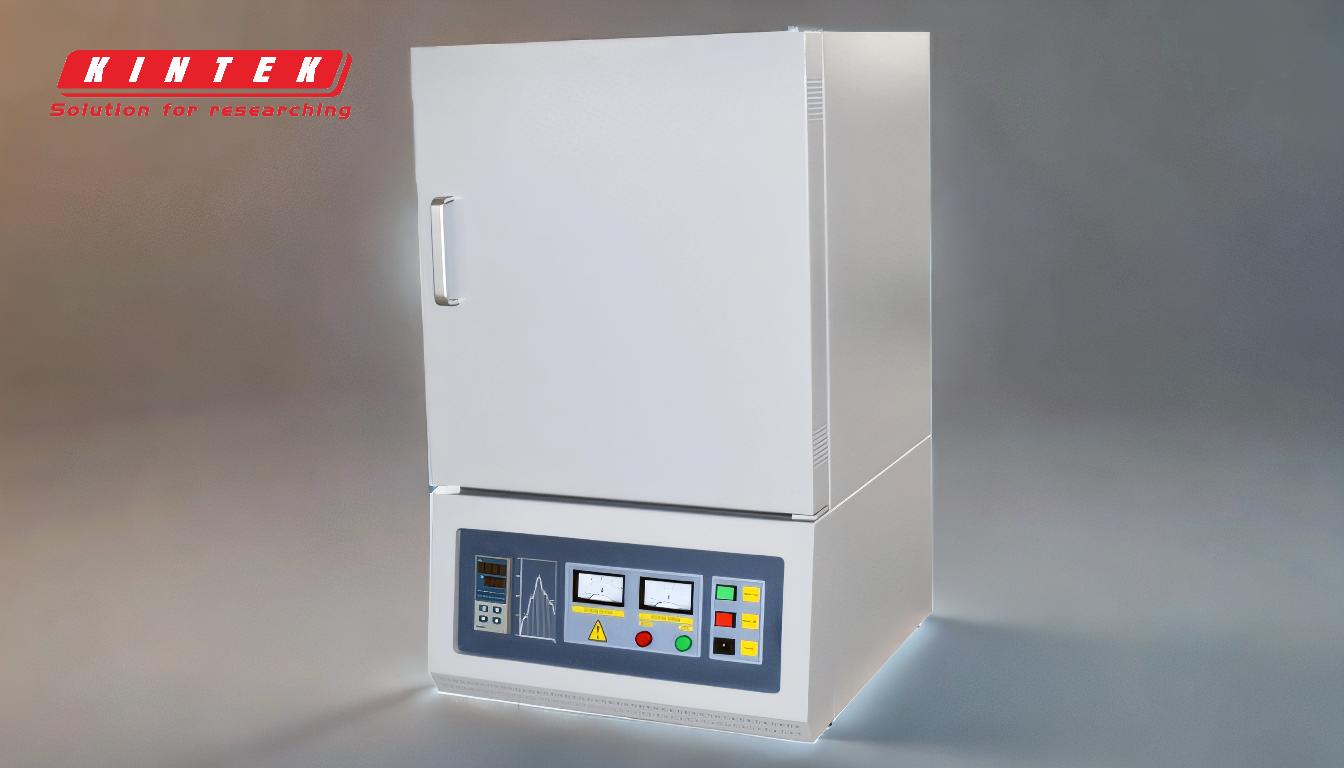
-
Primary Material of the Inner Chamber:
- The inner chamber of a muffle furnace is made of ceramic-based materials, such as:
- Ceramic Tiles: Suitable for temperatures up to 1200°C.
- Zirconia Boards: Capable of withstanding temperatures up to 1600°C.
- High Alumina Bricks: Designed for extreme temperatures up to 1800°C.
- These materials are chosen for their ability to withstand high temperatures without melting or deforming, ensuring long-term durability and efficient heat transfer.
- The inner chamber of a muffle furnace is made of ceramic-based materials, such as:
-
Ceramic Materials and Their Properties:
- Ceramic materials like alumina are commonly used due to their:
- High Thermal Resistance: They can endure temperatures up to 1400°C or higher.
- Chemical Corrosion Resistance: They resist reactions with chemicals, making them suitable for various industrial applications.
- Durability: They maintain structural integrity under repeated heating and cooling cycles.
- Ceramic materials like alumina are commonly used due to their:
-
Optional Chamber Types:
- Depending on the application, the inner chamber can be constructed using:
- Refractory-Brick Chambers: Ideal for larger furnaces and higher temperature ranges.
- Ceramic-Fiber Chambers: Lightweight and efficient for smaller furnaces or lower temperature applications.
- Depending on the application, the inner chamber can be constructed using:
-
Stainless Steel Linings:
- The fire-door and box panel linings are often made of stainless steel, which provides:
- Corrosion Resistance: Ensures longevity in harsh environments.
- Deformation Resistance: Maintains shape and functionality under high temperatures.
- The fire-door and box panel linings are often made of stainless steel, which provides:
-
Outer Body Construction:
- The outer body is typically made of thick mild steel (18/20 gauge) powder-coated for durability. Optional stainless steel (SS 304/316) bodies are available for enhanced corrosion resistance, especially in GMP-compliant environments.
-
Material Selection Based on Temperature:
- The choice of inner chamber material depends on the furnace's maximum operating temperature:
- Up to 1200°C: Ceramic tiles are sufficient.
- Up to 1600°C: Zirconia boards are used.
- Up to 1800°C: High alumina bricks are required.
- The choice of inner chamber material depends on the furnace's maximum operating temperature:
-
Insulation and Heat Retention:
- The furnace is insulated to minimize heat loss during operation, ensuring energy efficiency and consistent temperature control.
-
Customization Options:
- Manufacturers offer customization based on specific requirements, such as:
- Size of the Furnace: Larger furnaces may use firebricks, while smaller ones may use ceramic-fiber chambers.
- Temperature Range: Material selection is tailored to the intended use, ensuring optimal performance.
- Manufacturers offer customization based on specific requirements, such as:
By understanding these key points, a purchaser can make informed decisions when selecting a muffle furnace, ensuring it meets their specific temperature, durability, and application requirements.
Summary Table:
Component | Material | Temperature Range | Key Benefits |
---|---|---|---|
Inner Chamber | Ceramic Tiles | Up to 1200°C | Durability, efficient heat transfer |
Inner Chamber | Zirconia Boards | Up to 1600°C | High thermal resistance, deformation resistance |
Inner Chamber | High Alumina Bricks | Up to 1800°C | Extreme temperature resistance |
Fire-Door & Box Panel Linings | Stainless Steel | N/A | Corrosion resistance, deformation resistance |
Outer Body | Mild Steel (Powder-Coated) | N/A | Durability, corrosion resistance |
Outer Body (Optional) | Stainless Steel (SS 304/316) | N/A | Enhanced corrosion resistance (GMP-compliant) |
Insulation | Ceramic Fiber or Refractory Bricks | N/A | Heat retention, energy efficiency |
Need help selecting the right muffle furnace for your needs? Contact our experts today for tailored solutions!