Ion beam sputtering (IBS), also known as ion beam deposition (IBD), is a highly precise thin film deposition technique used in various industries, including optics, semiconductors, and nanotechnology. It involves using a focused ion beam to sputter material from a target onto a substrate, creating high-quality thin films with excellent thickness control and uniformity. The process occurs in a vacuum chamber filled with inert gas, where the target material is bombarded by energetic ions, causing atoms to be ejected and deposited onto the substrate. IBS is particularly valued for its ability to produce films with minimal defects and high density, making it ideal for applications requiring precise optical and mechanical properties.
Key Points Explained:
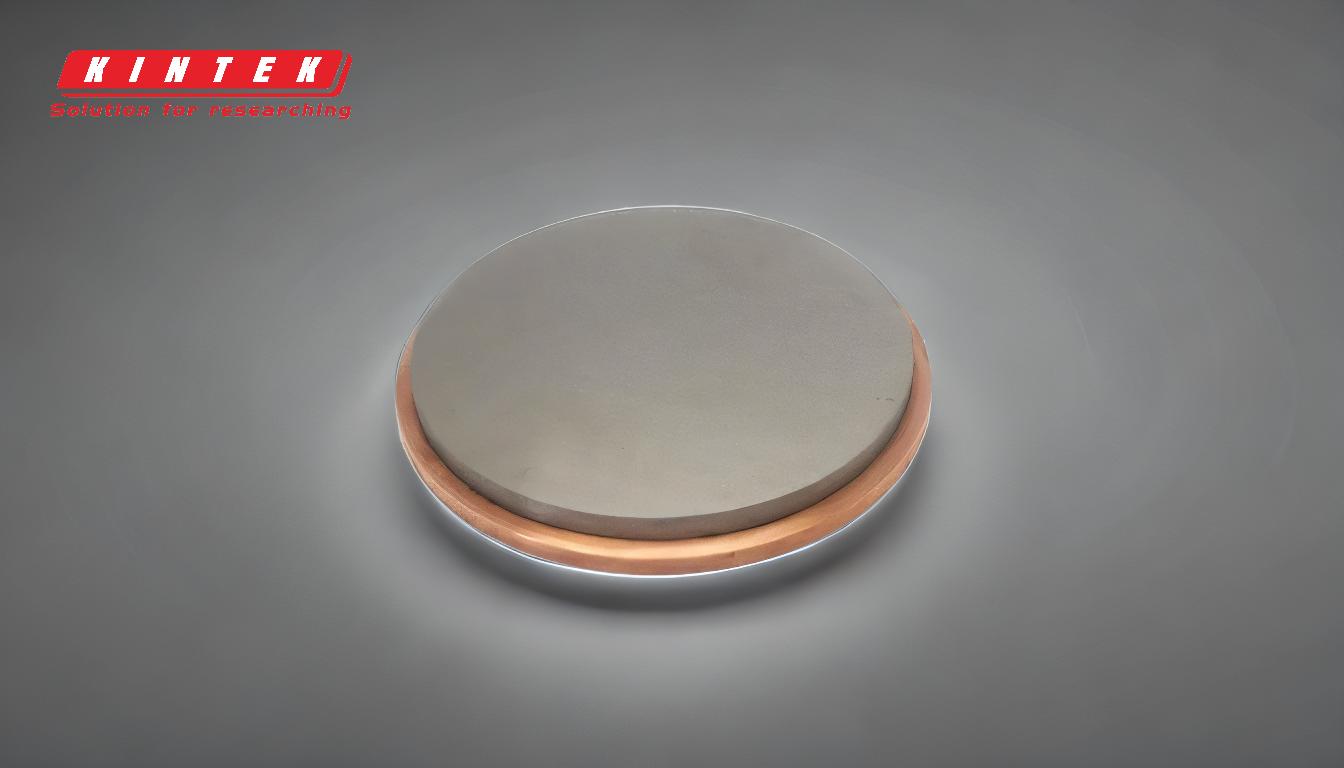
-
Definition and Overview of Ion Beam Sputtering (IBS):
- IBS is a physical vapor deposition (PVD) technique where a focused ion beam is used to sputter material from a target onto a substrate.
- It is also referred to as ion beam deposition (IBD) and is a subset of ion-assisted deposition methods.
- The process is conducted in a vacuum environment to ensure purity and control over the deposition process.
-
Key Components of the IBS Process:
- Ion Source: Generates a monoenergetic ion beam, typically using inert gases like argon. The ions are accelerated toward the target material.
- Target Material: The material to be sputtered, which is often a metal, ceramic, or compound.
- Substrate: The surface onto which the sputtered material is deposited. It can be made of glass, silicon, or other materials depending on the application.
- Vacuum Chamber: Provides a controlled environment free from contaminants, ensuring high-quality film deposition.
-
Mechanism of Ion Beam Sputtering:
- The ion beam is directed at the target material, causing atoms or molecules to be ejected due to momentum transfer.
- These ejected particles travel through the vacuum and deposit onto the substrate, forming a thin film.
- The energy and angle of the ion beam can be precisely controlled, allowing for fine-tuning of film properties such as thickness, density, and adhesion.
-
Advantages of Ion Beam Sputtering:
- High-Quality Films: IBS produces films with excellent uniformity, density, and minimal defects.
- Precision Control: The monoenergetic ion beam allows for precise control over film thickness and composition.
- Versatility: Suitable for depositing a wide range of materials, including metals, oxides, and nitrides.
- Low Substrate Damage: The process minimizes thermal and mechanical stress on the substrate, making it ideal for delicate materials.
-
Applications of Ion Beam Sputtering:
- Optical Coatings: IBS is widely used to create high-performance optical coatings for lenses, mirrors, and filters.
- Semiconductor Manufacturing: It is employed in the deposition of thin films for integrated circuits and other electronic components.
- Nanotechnology: IBS is used to fabricate nanostructures with precise dimensions and properties.
- Magnetic and Superconducting Films: The technique is suitable for depositing materials with specific magnetic or superconducting properties.
-
Comparison with Other Sputtering Methods:
- Ion Beam vs. Magnetron Sputtering: Magnetron sputtering uses a magnetic field to enhance ionization, resulting in higher deposition rates but potentially less control over film properties compared to IBS.
- Ion Beam vs. Reactive Sputtering: Reactive sputtering involves introducing reactive gases (e.g., oxygen or nitrogen) to form compound films, whereas IBS typically uses inert gases and focuses on precise material transfer.
- Ion Beam vs. Diode Sputtering: Diode sputtering relies on a simpler setup but lacks the precision and control offered by IBS.
-
Challenges and Limitations:
- Cost: IBS equipment and operation can be more expensive than other sputtering methods due to the complexity of the ion source and vacuum system.
- Deposition Rate: The deposition rate in IBS is generally lower compared to magnetron or diode sputtering, which may limit its use in high-throughput applications.
- Target Utilization: The focused ion beam may result in uneven erosion of the target material, requiring careful design and rotation of the target to maximize utilization.
-
Future Trends and Innovations:
- Hybrid Techniques: Combining IBS with other deposition methods, such as magnetron sputtering, to leverage the strengths of each approach.
- Advanced Ion Sources: Development of more efficient and versatile ion sources to improve deposition rates and energy control.
- In-Situ Monitoring: Integration of real-time monitoring systems to enhance process control and film quality.
By understanding the principles, advantages, and applications of ion beam sputtering, equipment and consumable purchasers can make informed decisions about its suitability for their specific needs. The method's precision and ability to produce high-quality films make it a valuable tool in advanced manufacturing and research.
Summary Table:
Aspect | Details |
---|---|
Definition | A PVD technique using a focused ion beam to deposit thin films. |
Key Components | Ion source, target material, substrate, and vacuum chamber. |
Advantages | High-quality films, precision control, versatility, low substrate damage. |
Applications | Optical coatings, semiconductors, nanotechnology, magnetic films. |
Comparison | Offers better control than magnetron or diode sputtering. |
Challenges | Higher cost, lower deposition rates, and target utilization issues. |
Future Trends | Hybrid techniques, advanced ion sources, and in-situ monitoring. |
Interested in leveraging ion beam sputtering for your projects? Contact our experts today to learn more!