Spark Plasma Sintering (SPS) is a modern sintering technique that combines the principles of hot pressing with the application of pulsed electric currents. This method enables rapid heating and consolidation of materials, resulting in shorter processing times and the ability to create materials with unique microstructures and properties. The key to its efficiency lies in the direct flow of electric current through the graphite die and the material being processed, which generates localized heating and facilitates densification. Additionally, the "spark plasma effect" plays a critical role in inhibiting particle growth, allowing for the production of fine-grained and high-performance materials.
Key Points Explained:
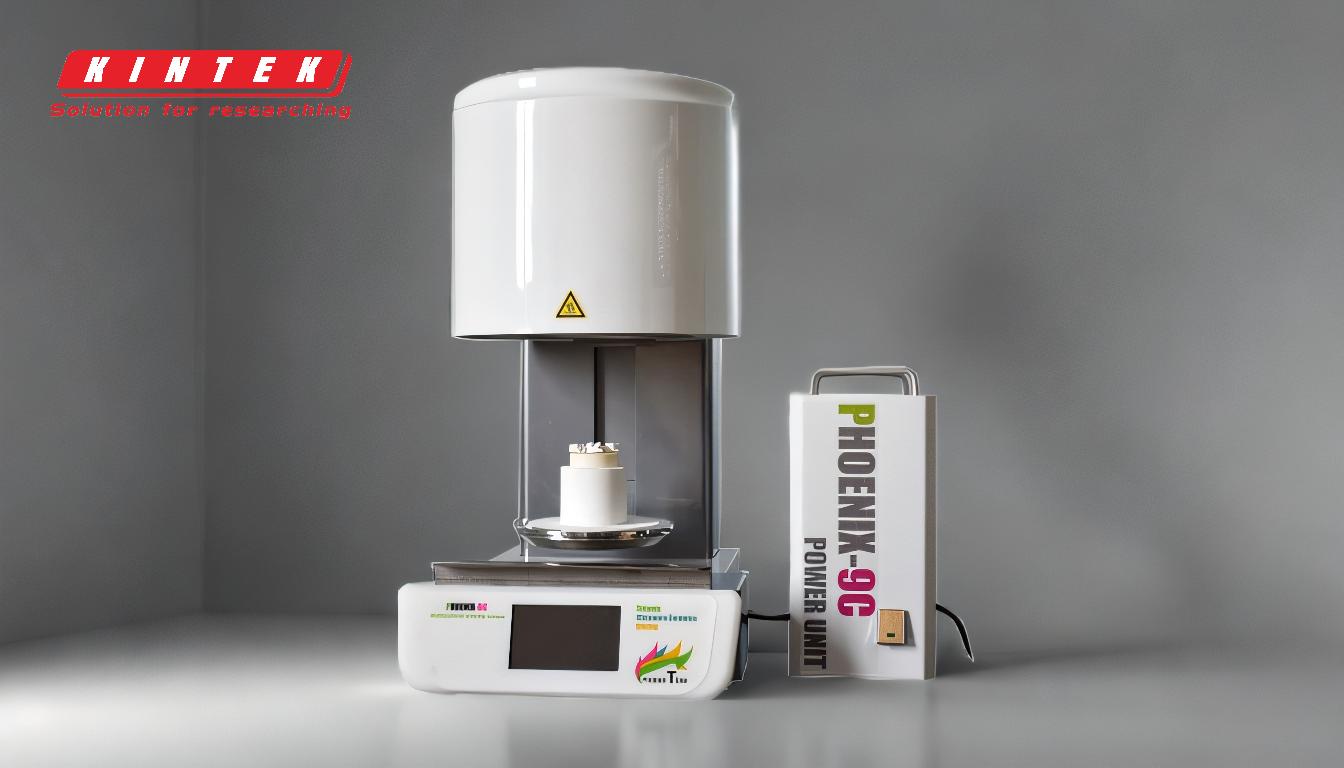
-
Modified Hot Pressing Setup:
- SPS builds on the traditional hot pressing method but introduces significant modifications. In conventional hot pressing, heat is applied externally to the die, which then transfers heat to the material. In SPS, the electric current flows directly through the graphite die and the material, enabling faster and more efficient heating.
- This direct heating mechanism reduces energy loss and allows for precise temperature control, which is crucial for achieving the desired material properties.
-
Pulsed Electric Currents:
- The use of pulsed electric currents is a defining feature of SPS. These currents generate rapid and localized heating, which significantly reduces the time required for sintering compared to conventional methods.
- The pulsed nature of the current also helps in maintaining a uniform temperature distribution within the material, minimizing thermal gradients that could lead to defects.
-
Spark Plasma Effect:
- The "spark plasma effect" is a phenomenon unique to SPS, where the electric current induces the formation of plasma between particles. This plasma facilitates the removal of surface oxides and contaminants, promoting better particle bonding.
- The spark plasma effect also inhibits particle growth during sintering, which is essential for producing materials with fine-grained microstructures. Fine-grained materials often exhibit superior mechanical, thermal, and electrical properties.
-
Rapid Heating and Short Process Cycles:
- One of the most significant advantages of SPS is its ability to achieve very fast heating rates, often reaching temperatures in the range of 1000-2000°C in just a few minutes. This rapid heating minimizes the time the material spends at high temperatures, reducing the risk of undesirable phase transformations or grain growth.
- Short process cycles not only improve efficiency but also make SPS suitable for processing temperature-sensitive materials that would degrade under prolonged exposure to high temperatures.
-
Creation of Unique Material Compositions and Properties:
- SPS enables the sintering of materials that are difficult or impossible to process using conventional methods. This includes materials with high melting points, nanomaterials, and composites.
- The unique heating mechanism and the spark plasma effect allow for the creation of materials with tailored microstructures, such as nanocrystalline or gradient materials, which can exhibit enhanced properties like increased strength, wear resistance, or thermal conductivity.
-
Graphite Die as a Key Component:
- The graphite die used in SPS serves multiple purposes. It acts as a mold for the material being sintered, conducts the electric current, and provides thermal insulation. Graphite is chosen for its high electrical conductivity, thermal stability, and resistance to thermal shock.
- The design of the die is critical for ensuring uniform current distribution and temperature control, which are essential for achieving consistent material properties.
-
Applications and Advantages:
- SPS is widely used in the production of advanced ceramics, metals, composites, and functionally graded materials. Its ability to produce dense, fine-grained materials with minimal defects makes it ideal for applications in aerospace, automotive, electronics, and biomedical industries.
- The process is also environmentally friendly, as it consumes less energy and produces fewer emissions compared to traditional sintering methods.
By combining the principles of hot pressing with innovative electrical and plasma effects, SPS offers a powerful tool for material scientists and engineers to create advanced materials with tailored properties and enhanced performance.
Summary Table:
Key Aspect | Description |
---|---|
Modified Hot Pressing | Direct electric current flow enables faster, more efficient heating. |
Pulsed Electric Currents | Rapid, localized heating reduces sintering time and ensures uniform temperature. |
Spark Plasma Effect | Inhibits particle growth, producing fine-grained, high-performance materials. |
Rapid Heating | Achieves 1000-2000°C in minutes, ideal for temperature-sensitive materials. |
Unique Material Creation | Enables sintering of high-melting-point materials, composites, and nanomaterials. |
Graphite Die | Conducts current, provides insulation, and ensures uniform temperature control. |
Applications | Aerospace, automotive, electronics, and biomedical industries benefit from SPS. |
Advantages | Energy-efficient, eco-friendly, and produces minimal defects. |
Unlock the potential of Spark Plasma Sintering for your material needs—contact our experts today!