Brazing is a widely used joining process that involves melting a filler metal to bond two or more materials without melting the base materials. The choice of filler material is critical to the success of the brazing process, as it determines the strength, durability, and compatibility of the joint. The most common materials used in brazing are silver, copper, nickel, and gold-based fillers. Each of these materials has specific properties that make them suitable for different applications, particularly in industries requiring high strength, corrosion resistance, or heat resistance. Proper preparation of materials, including cleaning to remove contaminants, is also essential to ensure high-quality brazed joints.
Key Points Explained:
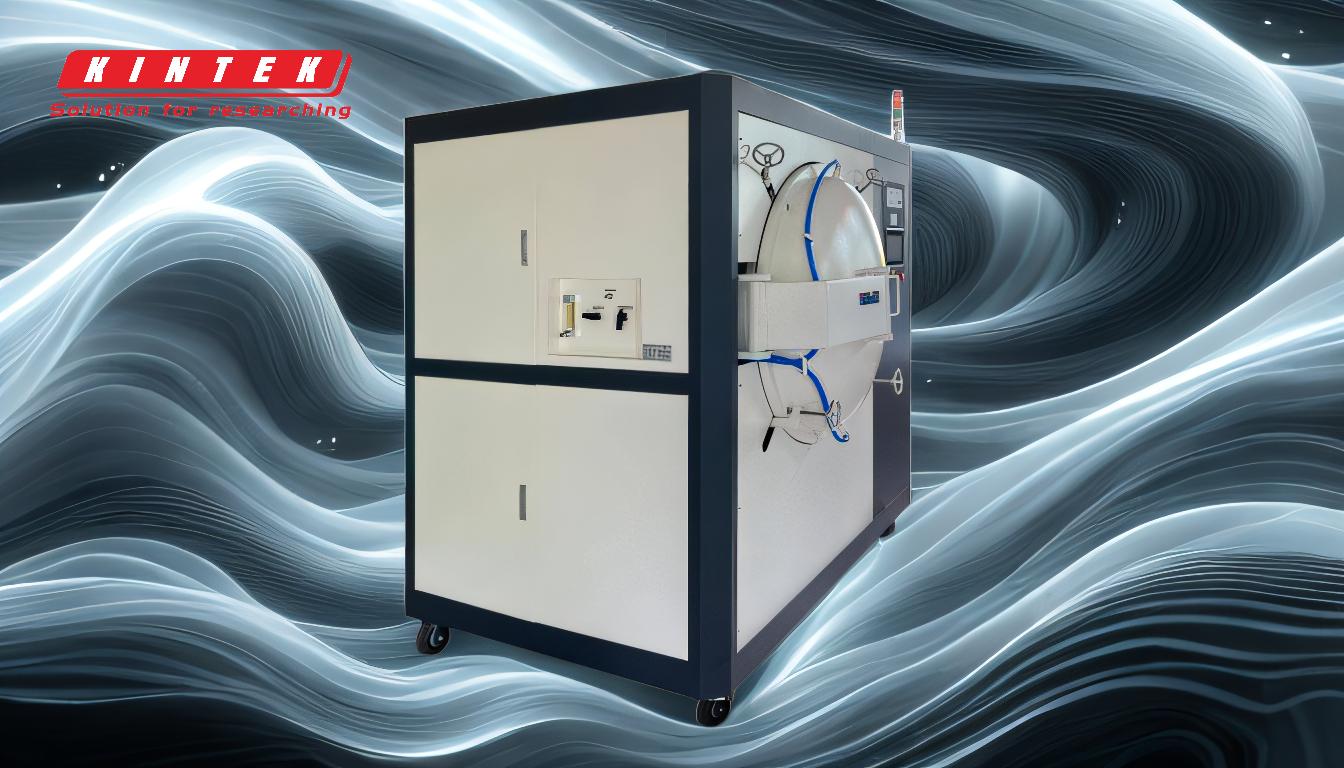
-
Silver-Based Fillers:
- Silver-based fillers are among the most widely used materials in brazing due to their excellent flow characteristics and ability to form strong, ductile joints.
- They are particularly suitable for joining materials like stainless steel, copper, and brass, and are often used in applications requiring high electrical conductivity.
- Silver fillers are also known for their ability to wet a wide range of base materials, making them versatile for various industrial applications.
-
Copper-Based Fillers:
- Copper fillers are commonly used in brazing applications where high thermal conductivity and strength are required.
- They are often used in furnace brazing of steel and other ferrous materials, as well as in applications involving copper and copper alloys.
- Copper-based fillers are cost-effective and provide excellent joint integrity, especially in high-temperature environments.
-
Nickel-Based Fillers:
- Nickel-based fillers are ideal for brazing stainless steels and heat- and corrosion-resistant alloys.
- They are known for their high strength and ability to withstand extreme temperatures, making them suitable for aerospace and power generation applications.
- Nickel fillers also exhibit good resistance to oxidation and corrosion, which is critical in harsh operating environments.
-
Gold-Based Fillers:
- Gold-based fillers are used in specialized applications requiring high reliability and resistance to corrosion, such as in the electronics and medical industries.
- They are particularly effective for brazing stainless steels and other alloys where minimal contamination and high joint integrity are essential.
- While gold fillers are more expensive, their superior performance in critical applications justifies their use.
-
Material Preparation:
- Before brazing, all materials must be thoroughly cleaned to remove surface contaminants such as grease, oil, and oxide layers.
- Proper cleaning ensures that the filler metal flows evenly and forms a strong bond with the base materials, resulting in high-quality brazed joints.
- Techniques such as chemical cleaning, mechanical abrasion, or ultrasonic cleaning are commonly used to prepare surfaces for brazing.
-
Distortion Prevention in Brazing:
- Distortion during brazing can be minimized through techniques such as stress relieving parts before brazing, using rigid fixtures to hold components in place, and designing parts to be heavier or larger to resist deformation.
- Despite these measures, some distortion may still occur, especially in complex or thin-walled components. Careful planning and process control are essential to mitigate these effects.
By understanding the properties and applications of these common brazing materials, as well as the importance of proper material preparation and distortion prevention, manufacturers can achieve high-quality, reliable brazed joints tailored to their specific needs.
Summary Table:
Filler Material | Key Properties | Common Applications |
---|---|---|
Silver-Based Fillers | Excellent flow, strong ductile joints, high electrical conductivity | Stainless steel, copper, brass, industrial applications |
Copper-Based Fillers | High thermal conductivity, strength, cost-effective | Steel, ferrous materials, copper alloys, high-temperature environments |
Nickel-Based Fillers | High strength, withstands extreme temperatures, oxidation and corrosion resistant | Stainless steel, aerospace, power generation, harsh environments |
Gold-Based Fillers | High reliability, corrosion resistance, minimal contamination | Electronics, medical industries, stainless steel, critical applications |
Need help selecting the right brazing material for your application? Contact our experts today for tailored solutions!