The neutral lining of an induction furnace is a critical component designed to protect the furnace structure and enhance its performance. It is made of refractory materials capable of withstanding extreme temperatures and resisting chemical reactions with molten metals. This lining serves as a barrier between the molten metal and the furnace's outer structure, such as the induction coil, ensuring the furnace's longevity and efficiency. It also isolates the molten metal, preventing contamination and maintaining the integrity of the metal being melted. The neutral lining is essential for the safe and effective operation of induction furnaces, making it a key consideration for equipment and consumable purchasers.
Key Points Explained:
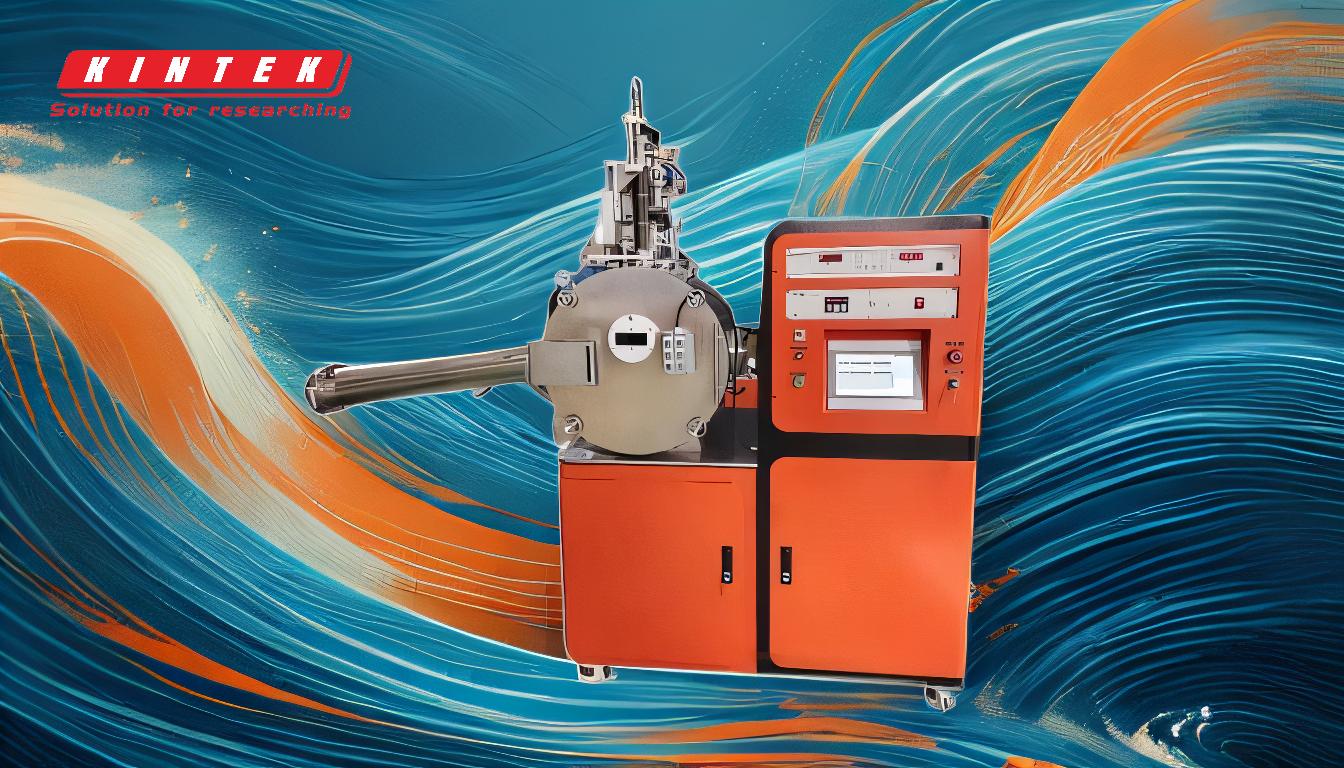
-
Definition and Purpose of the Neutral Lining:
- The neutral lining is a protective layer inside the induction furnace, made from refractory materials.
- Its primary purpose is to contain the molten metal, isolate it from the furnace's outer structure, and protect the furnace body during operation.
- It ensures the furnace operates efficiently and safely by preventing chemical reactions and thermal damage.
-
Materials Used in the Neutral Lining:
- Refractory materials are chosen for their ability to withstand high temperatures and resist chemical reactions with molten metals.
- Common materials include alumina, silica, and magnesia, which are selected based on the type of metal being melted and the operating conditions of the furnace.
-
Role in Protecting the Furnace Structure:
- The lining acts as a barrier between the molten metal and the induction coil, preventing direct contact and potential damage.
- It also protects the furnace body from thermal stress and mechanical wear, extending the furnace's lifespan.
-
Importance in Maintaining Metal Integrity:
- By isolating the molten metal, the neutral lining prevents contamination from external elements, ensuring the purity and quality of the melted metal.
- This is particularly important in applications requiring precise alloy compositions, such as in the aerospace and automotive industries.
-
Impact on Furnace Performance:
- A well-maintained neutral lining ensures efficient heat transfer and uniform melting of the metal charge.
- It minimizes heat loss and reduces energy consumption, contributing to the overall cost-effectiveness of the furnace operation.
-
Considerations for Purchasers:
- When selecting a neutral lining, purchasers should consider the type of metal being melted, the operating temperature, and the frequency of furnace use.
- The choice of refractory material should align with the specific requirements of the application to ensure optimal performance and durability.
-
Maintenance and Replacement:
- Regular inspection and maintenance of the neutral lining are essential to prevent cracks, erosion, and other forms of wear.
- Timely replacement of the lining is necessary to avoid furnace downtime and ensure consistent performance.
In summary, the neutral lining of an induction furnace is a vital component that ensures the safe, efficient, and reliable operation of the furnace. It protects the furnace structure, maintains the integrity of the molten metal, and contributes to the overall performance of the furnace. For equipment and consumable purchasers, understanding the role and importance of the neutral lining is crucial for making informed decisions and optimizing furnace operations.
Summary Table:
Key Aspect | Details |
---|---|
Purpose | Protects furnace structure, isolates molten metal, ensures safe operation. |
Materials | Alumina, silica, magnesia—chosen for high-temperature resistance. |
Role in Protection | Acts as a barrier, prevents thermal stress and mechanical wear. |
Metal Integrity | Prevents contamination, ensures purity and quality of melted metal. |
Performance Impact | Enhances heat transfer, reduces energy consumption, and improves efficiency. |
Purchasing Considerations | Match refractory materials to metal type, temperature, and usage frequency. |
Maintenance | Regular inspection and timely replacement to avoid downtime. |
Ensure your induction furnace operates at peak performance—contact our experts today to learn more about neutral linings!