The operating temperature of a calciner typically ranges from 550°C to 1300°C, depending on the specific application and the material being processed. Calcination is a high-temperature process used to thermally decompose materials, remove volatile components, or induce phase transitions. The temperature range is influenced by factors such as the type of material, the desired chemical reaction, and the equipment design. For instance, some applications may require lower temperatures (550–1150°C), while others, like advanced ceramic processing, may necessitate higher temperatures up to 1300°C. The calciner's design, including its ability to maintain a controlled atmosphere, also plays a critical role in determining the optimal operating temperature.
Key Points Explained:
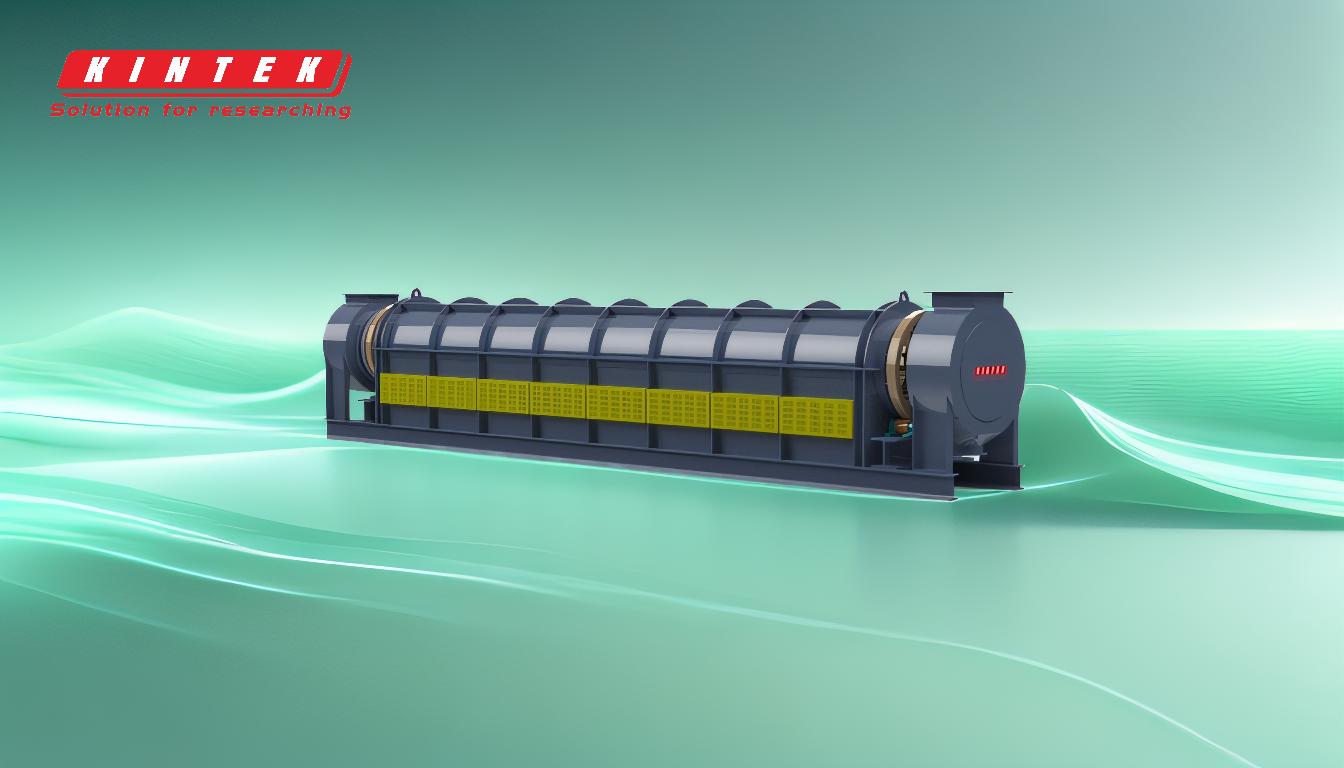
-
Typical Operating Temperature Range:
- The operating temperature of a calciner generally falls between 550°C and 1300°C.
- This range is determined by the specific material being processed and the desired chemical or physical transformation.
- For example, lower temperatures (550–1150°C) are often used for processes like thermal decomposition, while higher temperatures (up to 1300°C) are required for advanced material synthesis.
-
Factors Influencing Temperature:
- Material Properties: Different materials have unique thermal decomposition or reaction temperatures. For instance, limestone calcination typically occurs around 900°C, while other materials may require higher temperatures.
- Process Requirements: The specific application, such as removing volatile components or inducing phase changes, dictates the temperature.
- Equipment Design: The calciner's design, including its heating mechanism and insulation, affects its ability to achieve and maintain high temperatures.
-
Applications and Temperature Variations:
- Lower Temperature Range (550–1150°C): Used for processes like thermal decomposition of carbonates, hydroxides, or organic materials.
- Higher Temperature Range (up to 1300°C): Required for advanced applications such as ceramic sintering or high-purity material synthesis.
- The temperature is often tailored to ensure optimal reaction kinetics and material properties.
-
Controlled Atmosphere:
- Calcination often requires a controlled atmosphere to prevent unwanted reactions or contamination.
- The calciner's ability to maintain a specific atmosphere (e.g., inert, oxidizing, or reducing) is crucial for achieving the desired results.
-
Equipment Design and Efficiency:
- Calcination furnaces are designed to handle high temperatures efficiently, often using indirect heating methods to ensure uniform temperature distribution.
- The use of rotating steel cylinders, as mentioned in the references, helps maintain consistent processing conditions.
-
Practical Considerations for Purchasers:
- When selecting a calciner, consider the required temperature range for your specific application.
- Evaluate the furnace's ability to maintain a controlled atmosphere and its energy efficiency.
- Ensure the equipment is designed for durability and can withstand prolonged high-temperature operation.
By understanding these key points, purchasers can make informed decisions when selecting a calciner that meets their specific processing needs.
Summary Table:
Key Aspect | Details |
---|---|
Typical Temperature Range | 550°C to 1300°C |
Lower Range (550–1150°C) | Used for thermal decomposition of carbonates, hydroxides, or organic materials. |
Higher Range (up to 1300°C) | Required for advanced ceramic sintering or high-purity material synthesis. |
Influencing Factors | Material properties, process requirements, and equipment design. |
Controlled Atmosphere | Essential for preventing unwanted reactions or contamination. |
Equipment Design | Ensures uniform temperature distribution and durability for high-temperature use. |
Need a calciner tailored to your specific temperature requirements? Contact our experts today to find the perfect solution!