Thermal evaporation is a widely used thin-film deposition technique where a material is heated in a vacuum until its vapor pressure exceeds the surrounding pressure, causing it to vaporize and condense on a substrate. The process requires a high vacuum environment, typically between 10^-7 to 10^-5 mbar, to ensure a clean surface and a long mean free path for vaporized molecules. The pressure and temperature conditions are critical for achieving high-quality films with good adhesion and uniformity. The choice of material and substrate heating also play significant roles in determining the final properties of the deposited film.
Key Points Explained:
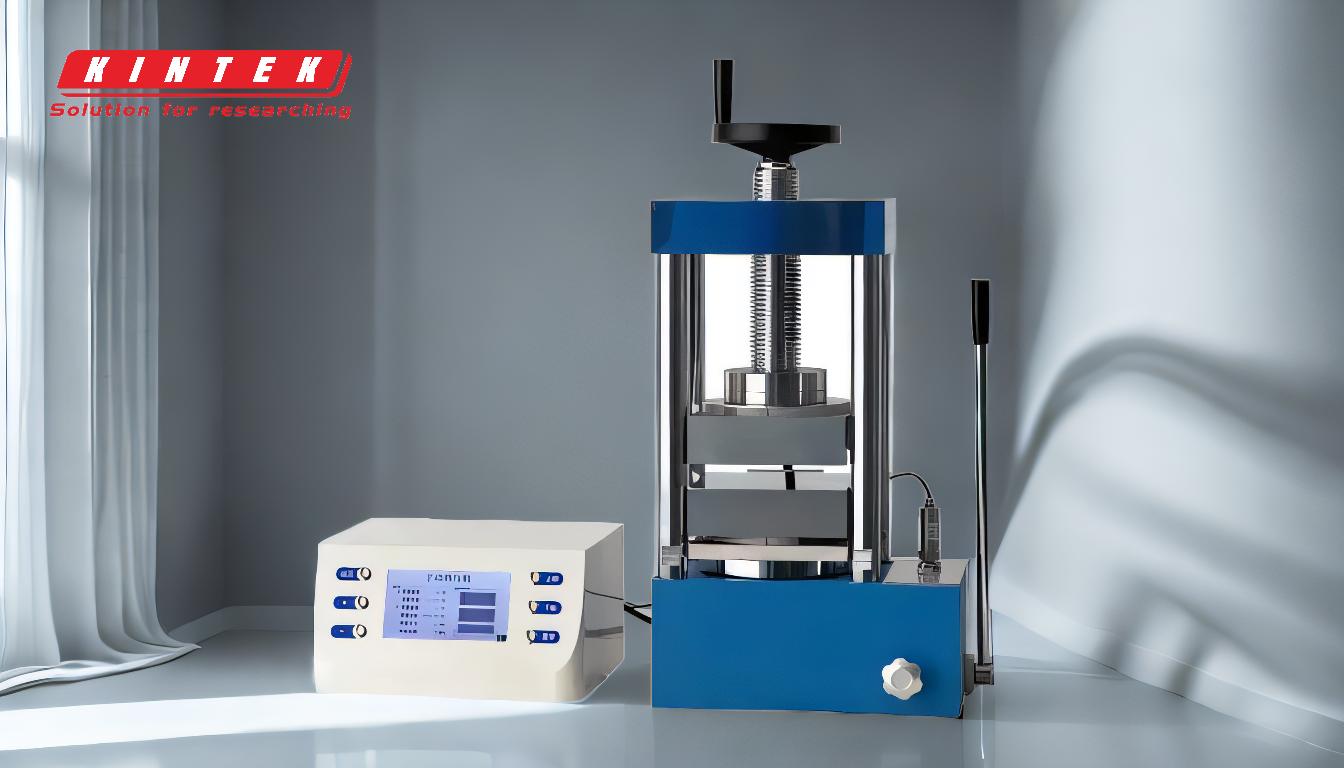
-
Vapor Pressure and Evaporation:
- Each material has a specific vapor pressure at a given temperature. For thermal evaporation, the material is heated until its vapor pressure exceeds the vacuum environment's pressure, causing it to vaporize.
- This vaporization allows the material to travel to the substrate, where it condenses to form a thin film.
-
Vacuum Requirements:
- A high vacuum environment is essential for thermal evaporation, typically ranging from 10^-7 to 10^-5 mbar.
- This vacuum ensures a long mean free path for vaporized molecules, minimizing collisions with residual gas molecules and ensuring they reach the substrate unscattered.
- A clean vacuum environment is also crucial for proper adhesion of the evaporated atoms to the substrate, preventing the formation of unstable layers.
-
Substrate Temperature:
- The temperature of the substrate significantly influences the properties of the deposited film.
- Heating the substrate above 150 °C can improve the adhesion of the film to the substrate by providing enough energy for the evaporated atoms to move freely and form a uniform film.
-
Evaporation Source and Heating:
- The target material is placed in an evaporation source (such as a boat, coil, or basket) and heated using an electric current.
- This method, also known as resistive evaporation, relies on the heat generated by electrical resistance to reach the material's evaporation point.
-
Material Selection:
- The choice of material for thermal evaporation depends on its reaction characteristics and the specific requirements of the deposition process.
- Different materials have different vapor pressures and evaporation temperatures, which must be carefully considered to achieve the desired film properties.
-
Pressure and Quality of the Layer:
- The required base pressure in the coating device varies depending on the desired quality of the deposited layer.
- Higher-quality layers typically require lower base pressures (closer to 10^-7 mbar) to minimize contamination and ensure a clean deposition environment.
By carefully controlling these factors—vapor pressure, vacuum conditions, substrate temperature, and material selection—thermal evaporation can produce high-quality thin films with excellent adhesion and uniformity. This makes it a valuable technique in various applications, including semiconductor manufacturing, optical coatings, and nanotechnology.
Summary Table:
Key Factor | Description |
---|---|
Vapor Pressure | Material is heated until vapor pressure exceeds vacuum pressure for evaporation. |
Vacuum Requirements | High vacuum (10^-7 to 10^-5 mbar) ensures clean surfaces and long mean free path. |
Substrate Temperature | Heating above 150 °C improves film adhesion and uniformity. |
Evaporation Source | Resistive heating (boat, coil, or basket) vaporizes the material. |
Material Selection | Vapor pressure and evaporation temperature vary by material. |
Pressure & Layer Quality | Lower base pressures (closer to 10^-7 mbar) yield higher-quality layers. |
Discover how thermal evaporation can enhance your thin-film applications—contact our experts today!