The pressure in a sputter coater is a critical parameter that directly influences the quality and efficiency of the sputtering process. Typically, a sputter coater operates within a vacuum range of 8 x 10^-2 to 2 x 10^-2 mbar. This low-pressure environment is essential for creating the conditions necessary for sputtering, where atoms are ejected from a solid target material due to bombardment by energetic ions. The vacuum ensures minimal interference from air molecules, allowing for precise control over the deposition process and the production of high-quality thin films. Understanding the pressure requirements and their impact on the sputtering process is crucial for optimizing the performance of a sputter coater.
Key Points Explained:
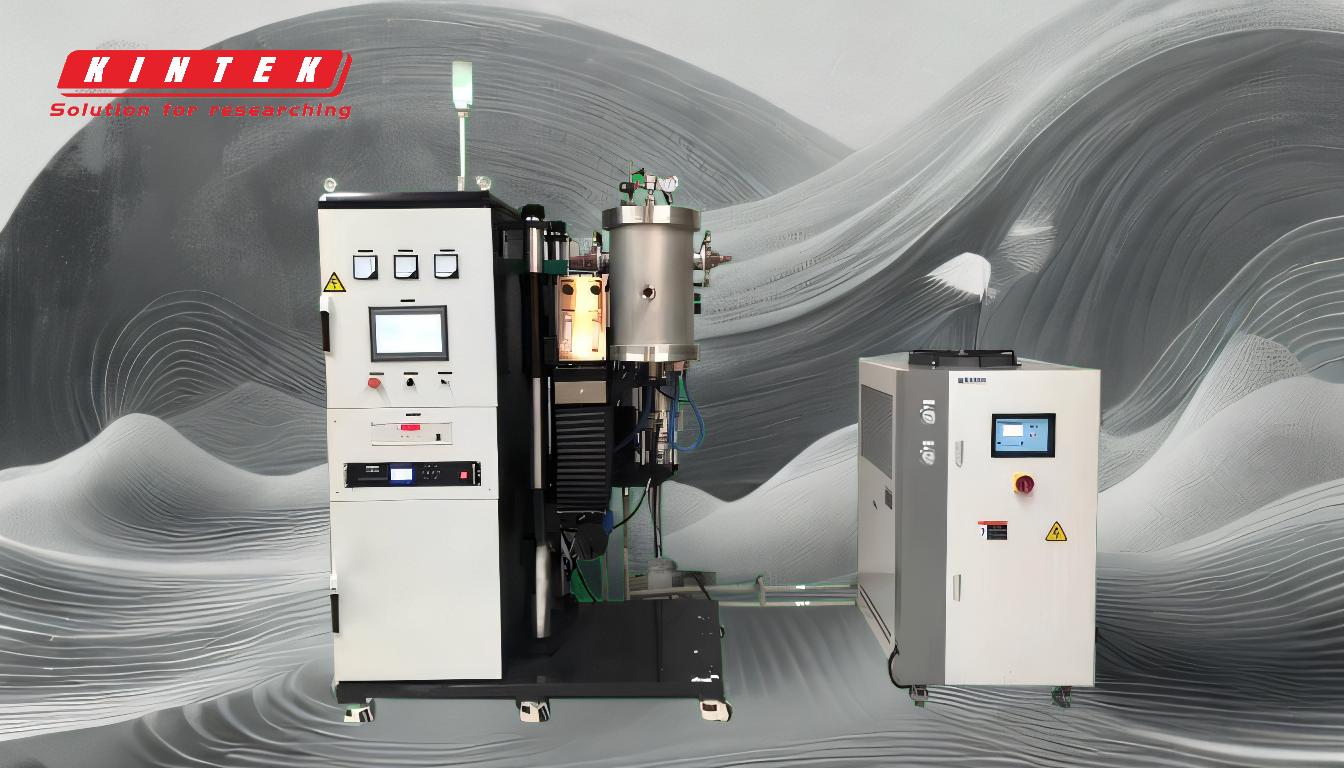
-
Vacuum Pressure Range:
- The typical operating pressure for a sputter coater ranges from 8 x 10^-2 to 2 x 10^-2 mbar. This low-pressure environment is necessary to reduce the presence of air molecules, which could otherwise interfere with the sputtering process. The vacuum ensures that the sputtered particles travel unimpeded from the target to the substrate, resulting in a more controlled and efficient deposition process.
-
Importance of Vacuum in Sputtering:
- A high vacuum is crucial for maintaining the integrity of the sputtering process. It minimizes collisions between sputtered particles and residual gas molecules, which can scatter the particles and reduce the deposition rate. Additionally, the vacuum helps to prevent contamination of the thin film, ensuring that the deposited material is pure and of high quality.
-
Impact on Deposition Rate and Film Quality:
- The pressure within the sputter coater directly affects the deposition rate and the quality of the thin film. At the optimal pressure range, the sputtered particles can travel directly to the substrate, leading to a higher deposition rate and a more uniform film. Deviations from this pressure range can result in slower deposition rates and films with poor adhesion, density, or crystallinity.
-
Control Over Film Thickness and Uniformity:
- Operating within the specified pressure range allows for precise control over the thickness of the deposited film. By adjusting the sputtering time and target input current, it is possible to achieve high-precision film thickness. The uniformity of the film is also enhanced, as the low-pressure environment ensures that the sputtered particles are evenly distributed across the substrate.
-
Advantages of Sputter Coating:
- Sputter coating offers several advantages over other thin film deposition techniques, such as vacuum evaporation. These include stronger adhesion, denser films, and the ability to produce crystalline films at lower temperatures. The high nucleation density in sputter coating allows for the creation of extremely thin continuous films, even as thin as 10 nm or less. Additionally, the long service life of targets and the ability to shape them into various forms contribute to the efficiency and flexibility of the sputtering process.
-
Role of Reactive Gases:
- In some cases, reactive gases like oxygen can be introduced into the sputter coater to produce compound or mixed films. The presence of these gases can alter the properties of the deposited film, such as its electrical conductivity or optical properties. The pressure within the chamber must be carefully controlled when using reactive gases to ensure that the desired film composition is achieved.
-
Temperature Considerations:
- The pressure in the sputter coater also affects the temperature rise during the sputtering process. Maintaining the pressure within the optimal range helps to keep the temperature rise below 10°C, which is important for preventing damage to temperature-sensitive substrates. This low-temperature operation is one of the key advantages of sputter coating, as it allows for the deposition of thin films on a wide range of materials without causing thermal degradation.
In summary, the pressure in a sputter coater is a fundamental parameter that influences the efficiency, quality, and control of the sputtering process. Operating within the specified vacuum range ensures optimal conditions for producing high-quality thin films with precise thickness and uniformity. Understanding and controlling the pressure is essential for achieving the desired film properties and maximizing the performance of the sputter coater.
Summary Table:
Aspect | Details |
---|---|
Pressure Range | 8 x 10^-2 to 2 x 10^-2 mbar |
Importance of Vacuum | Minimizes air molecule interference, ensures particle travel, and prevents contamination. |
Impact on Deposition | Higher deposition rates, uniform films, and better adhesion at optimal pressure. |
Film Thickness Control | Precise control over thickness and uniformity through pressure adjustments. |
Advantages | Strong adhesion, dense films, low-temperature operation, and long target life. |
Reactive Gases | Controlled pressure ensures proper film composition when using reactive gases. |
Temperature Considerations | Pressure control keeps temperature rise below 10°C, protecting sensitive substrates. |
Need help optimizing your sputter coater's performance? Contact our experts today for tailored solutions!