The pressure inside a vacuum chamber is always below atmospheric pressure, as the chamber is designed to create a vacuum by removing air and other gases. The specific pressure range depends on the application, design, and operational requirements of the chamber. For example, in chemical production, the vacuum range is typically between 1 to 10 mbar, while in vacuum furnace systems, it can range from 10^-5 to 10^-6 mbar. The ultimate vacuum level is influenced by factors such as material cleanliness, outgassing, and leakage rates. Proper design, including material selection and structural integrity, is critical to maintaining the desired vacuum levels and ensuring the chamber's performance.
Key Points Explained:
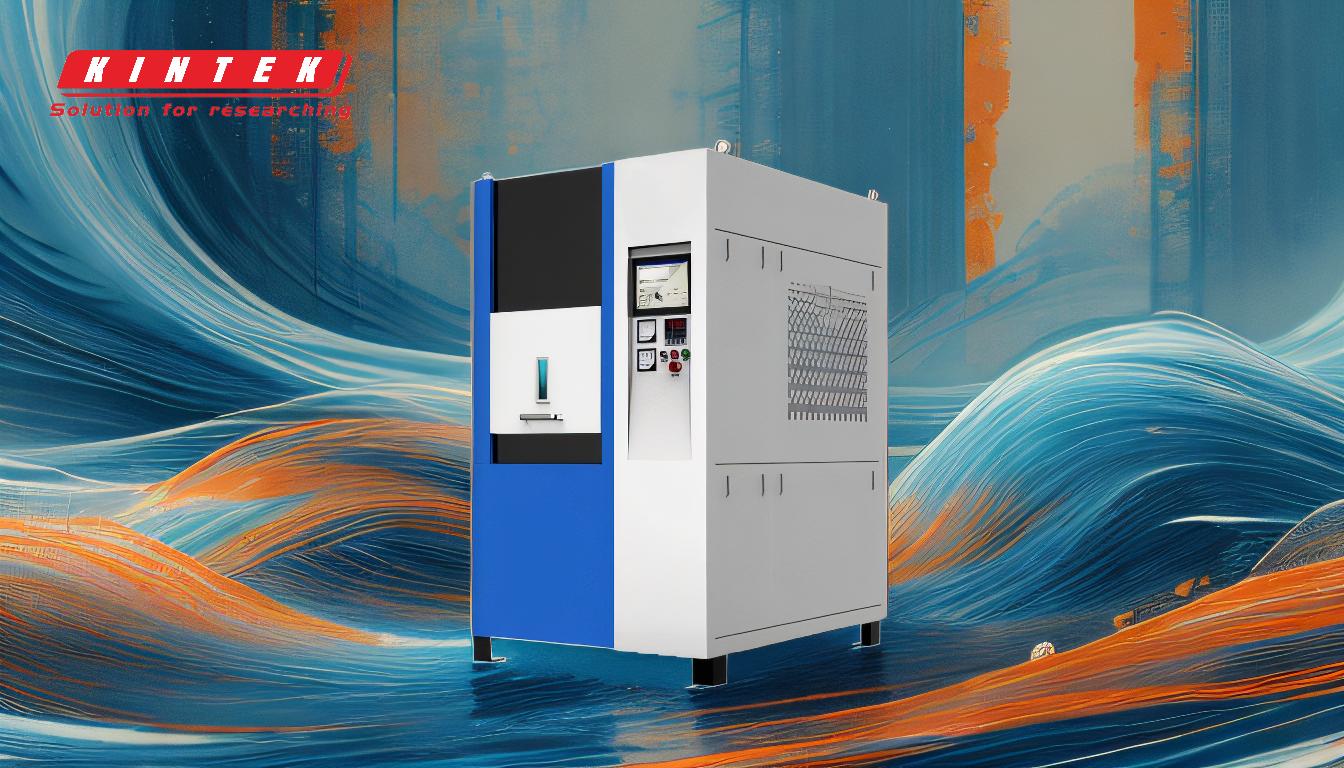
-
Definition of Vacuum Chamber Pressure:
- A vacuum chamber is designed to create a pressure lower than atmospheric pressure (760 mmHg or 101325 Pa). The exact pressure inside the chamber depends on the application and the vacuum system's capabilities.
-
Pressure Ranges for Different Applications:
- Chemical Production: The vacuum range is typically between 1 to 10 mbar.
- Vacuum Furnace Systems: The pressure can range from 10^-5 to 10^-6 mbar, depending on the system's design and operational requirements.
- General Vacuum Chambers: The pressure is often maintained in the range of 101 to 104 Pa, with 104 Pa being the base pressure.
-
Factors Affecting Vacuum Levels:
- Material Cleanliness: Contaminants on chamber surfaces can release gases, affecting the vacuum level.
- Outgassing: Materials introduced into the chamber, such as samples or components, can release gases over time.
- Leakage Rates: The integrity of seals and the chamber's construction play a significant role in maintaining the desired vacuum.
- Ambient Conditions: Humidity and temperature can influence the vacuum level, especially in systems where precise control is required.
-
Design Considerations for Vacuum Chambers:
- Material Selection: The chamber must be made of materials that can withstand drastic pressure changes and maintain structural integrity.
- Shape and Structure: The chamber's shape (e.g., cylindrical, spherical, or rectangular) and structural components must ensure stability and resilience.
- Flanges and Seals: High-precision machining and proper sealing are essential to prevent leaks and maintain vacuum levels.
- Vacuum Pumps: Both roughing and main pumps are used to achieve and maintain the desired vacuum.
-
Importance of Maintaining Vacuum Levels:
- Maintaining the correct vacuum level is critical for the performance of the chamber and the processes it supports. For example, in chemical production, the vacuum level affects the evaporation rate of solvents, while in vacuum furnaces, it impacts the quality of heat treatment processes.
-
Measurement and Control of Vacuum:
- Modern vacuum systems are equipped with sensors and controls to regulate the depth of the vacuum. This ensures that the pressure remains within the required range for the specific application.
In summary, the pressure inside a vacuum chamber is always below atmospheric pressure, and the specific range depends on the application and design. Proper design, material selection, and maintenance are crucial to achieving and maintaining the desired vacuum levels.
Summary Table:
Aspect | Details |
---|---|
Pressure Definition | Below atmospheric pressure (760 mmHg or 101325 Pa). |
Pressure Ranges | - Chemical Production: 1–10 mbar - Vacuum Furnace: 10^-5 to 10^-6 mbar |
Factors Affecting Vacuum | Material cleanliness, outgassing, leakage rates, ambient conditions. |
Design Considerations | Material selection, shape, flanges, seals, and vacuum pumps. |
Importance of Vacuum | Critical for chamber performance and process efficiency. |
Ensure your vacuum chamber performs at its best—contact our experts today for tailored solutions!