The Physical Vapor Deposition (PVD) process, specifically for Indium Tin Oxide (ITO), is a highly sophisticated method used to deposit thin, conductive, and transparent coatings onto substrates. This process is widely used in applications such as touchscreens, solar panels, and flat-panel displays. The ITO PVD process involves several critical steps, including preparation, vaporization, transportation, reaction, and deposition, all carried out in a high-vacuum environment. The process is environmentally friendly, offers excellent material properties, and can be tailored to meet specific application requirements.
Key Points Explained:
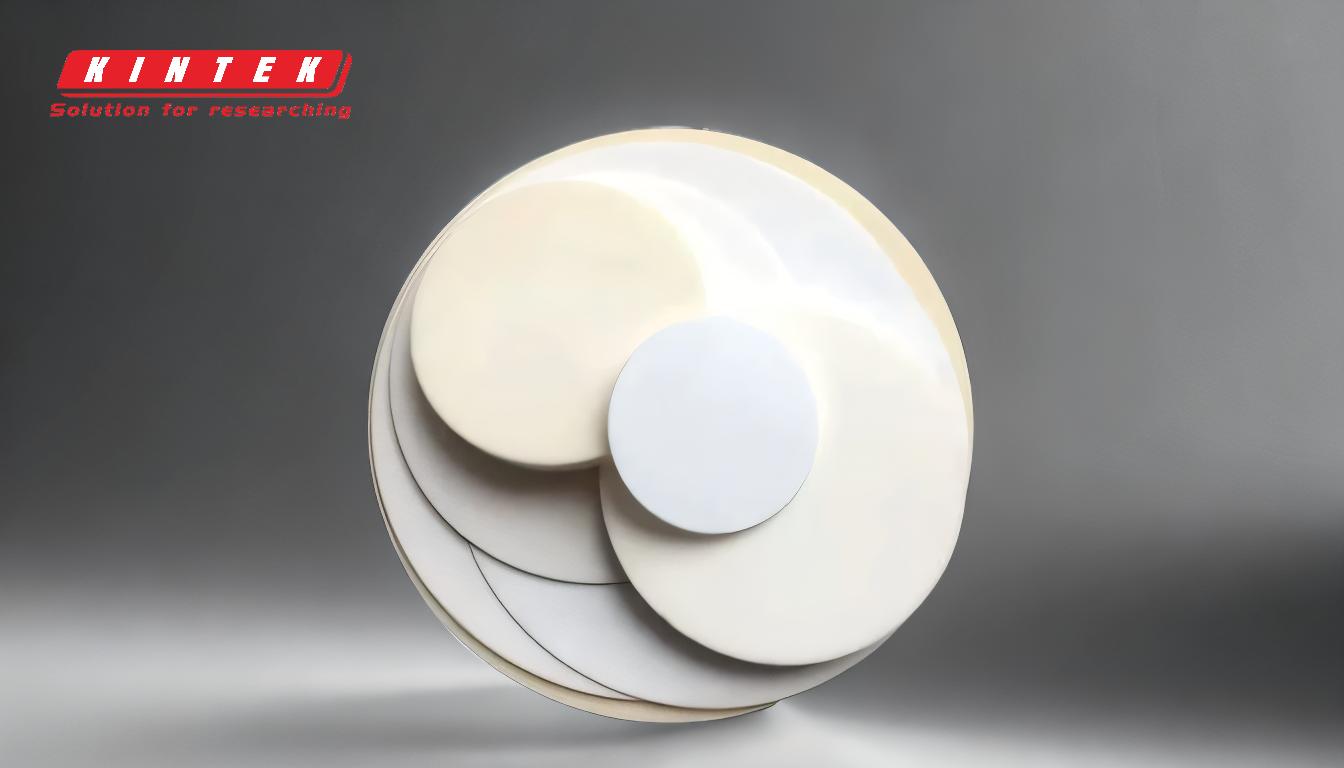
-
Preparation of the Substrate:
- Before the PVD process begins, the substrate must undergo thorough cleaning and pre-treatment to ensure optimal adhesion of the ITO coating. This may involve stripping any existing coatings, cleaning, and drying the substrate.
- Fixturing and visual inspection are also crucial to ensure the substrate is properly aligned and free of defects before entering the vacuum chamber.
-
Evaporation of the Target Material:
- The ITO target material, typically a combination of indium oxide and tin oxide, is vaporized using a high-energy source such as sputtering or arc discharge. This process dislodges atoms from the target material, creating a vapor.
- The vaporization occurs in a high-vacuum chamber to prevent contamination and ensure a clean deposition environment.
-
Transportation of Vaporized Atoms:
- The vaporized atoms are transported from the target material to the substrate. This step is critical as it ensures that the atoms travel uniformly and deposit evenly on the substrate.
- The transportation process is facilitated by the vacuum environment, which minimizes collisions with other particles and ensures a direct path to the substrate.
-
Reaction with Reactive Gases:
- During the transportation phase, the vaporized atoms may react with reactive gases such as oxygen or nitrogen. This reaction modifies the composition of the vaporized material, enhancing the properties of the final coating.
- For ITO coatings, the reaction with oxygen is particularly important to achieve the desired conductive and transparent properties.
-
Deposition onto the Substrate:
- The final step involves the condensation of the vaporized atoms onto the substrate, forming a thin, uniform layer of ITO. This layer is typically only a few nanometers thick but provides excellent conductivity and transparency.
- The deposition process is carefully controlled to ensure the coating meets specific thickness and uniformity requirements.
-
Post-Treatment and Quality Control:
- After the deposition, the coated substrate may undergo post-treatment processes such as annealing to improve the coating's properties.
- Quality control measures, including thickness measurement and visual inspection, are performed to ensure the coating meets the desired specifications.
-
Advantages of ITO PVD:
- The ITO PVD process offers several advantages, including the ability to deposit materials with improved properties compared to the substrate.
- It is an environmentally friendly process, as it does not involve harmful chemicals or produce significant waste.
- The process can be tailored to deposit a wide range of materials, making it versatile for various applications.
In summary, the ITO PVD process is a precise and controlled method for depositing thin, conductive, and transparent coatings onto substrates. It involves several critical steps, from substrate preparation to post-treatment, all carried out in a high-vacuum environment to ensure optimal results. The process is environmentally friendly, offers excellent material properties, and can be customized to meet specific application needs.
Summary Table:
Step | Description |
---|---|
1. Substrate Preparation | Clean and pre-treat the substrate for optimal adhesion. |
2. Evaporation | Vaporize ITO target material using high-energy sources like sputtering. |
3. Transportation | Transport vaporized atoms to the substrate in a high-vacuum environment. |
4. Reaction | React vaporized atoms with gases like oxygen to enhance coating properties. |
5. Deposition | Condense atoms onto the substrate to form a thin, uniform ITO layer. |
6. Post-Treatment | Anneal and inspect the coating to ensure quality and performance. |
7. Advantages | Environmentally friendly, customizable, and improves material properties. |
Ready to enhance your applications with ITO PVD coatings? Contact us today to learn more!