The sintering process of ceramics is a critical manufacturing technique used to transform powdered ceramic materials into dense, strong, and durable objects. It involves several stages, including powder preparation, shaping, heating, and consolidation. The process begins with the mixing of raw materials, followed by compression into a desired shape (green body). The green body is then subjected to high temperatures, which remove binders and volatile components, and cause the ceramic particles to bond and densify. This results in a solid, low-porosity ceramic object with improved mechanical properties. The process is widely used in industries such as pottery, electronics, and aerospace for creating high-performance ceramic components.
Key Points Explained:
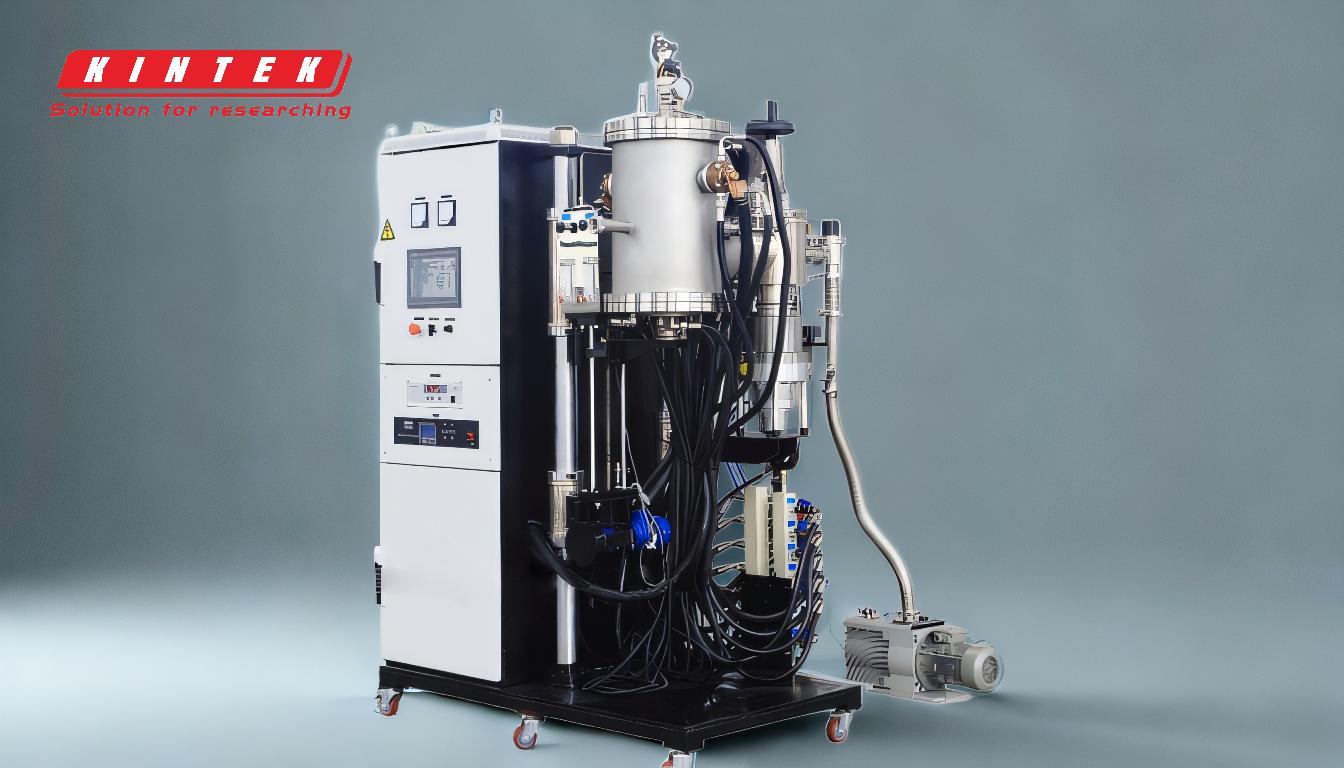
-
Powder Preparation and Mixing:
- The process begins with the preparation of ceramic powder, which involves mixing primary materials, binders, and deflocculants to form a uniform slurry.
- The slurry is then spray-dried to create a free-flowing powder that can be easily shaped.
- Example: In pottery, clay is mixed with water and other additives to form a workable paste.
-
Shaping (Pressing or Forming):
- The prepared powder is compressed into a mold to form a "green body," which is a loosely bonded, pre-sintered shape.
- Techniques such as uniaxial pressing, isostatic pressing, or 3D printing may be used depending on the desired geometry.
- Example: In manufacturing ceramic tiles, the powder is pressed into flat, rectangular shapes.
-
Binder Removal (Debinding):
- The green body is heated at a low temperature to burn off organic binders and other volatile components.
- This step is crucial to prevent defects during the high-temperature sintering process.
- Example: In advanced ceramics, binders are carefully removed to ensure uniform sintering.
-
High-Temperature Sintering:
- The debinded green body is heated to a temperature just below its melting point in a controlled atmosphere.
- During this stage, particles undergo material migration and grain boundary movement, leading to densification and reduced porosity.
- Example: In the production of alumina ceramics, temperatures of 1500–1700°C are used to achieve full densification.
-
Densification and Shrinkage:
- As the ceramic particles bond, the material shrinks and becomes denser, forming a solid, cohesive structure.
- The reduction in porosity enhances the mechanical strength and thermal properties of the ceramic.
- Example: In sintered silicon carbide, the material shrinks by 15–20% during sintering.
-
Cooling and Solidification:
- After sintering, the ceramic is slowly cooled to room temperature to prevent cracking or warping.
- The final product is a fully densified ceramic with a crystalline or glassy microstructure.
- Example: Zirconia ceramics are cooled in a controlled manner to maintain their phase stability.
-
Post-Sintering Processes (Optional):
- Some applications require additional steps such as machining, surface finishing, or metallization.
- Machining with diamond tools or ultrasonic methods is often used to achieve precise dimensions.
- Example: Ceramic components for electronics are metallized to enable electrical connections.
-
Applications of Sintered Ceramics:
- Sintered ceramics are used in a wide range of industries, including pottery, electronics, aerospace, and biomedical devices.
- Their high strength, wear resistance, and thermal stability make them ideal for demanding applications.
- Example: Sintered alumina is used in cutting tools, while zirconia is used in dental implants.
By understanding these key steps, equipment and consumable purchasers can better evaluate the quality and suitability of sintered ceramic products for their specific needs. The process ensures that the final product meets the required mechanical, thermal, and dimensional specifications.
Summary Table:
Stage | Description | Example |
---|---|---|
Powder Preparation | Mixing raw materials, binders, and deflocculants to form a uniform slurry, then spray-drying. | Clay mixed with water and additives to form a workable paste. |
Shaping | Compressing powder into a mold to create a 'green body' using pressing or 3D printing techniques. | Ceramic tiles pressed into flat, rectangular shapes. |
Binder Removal | Heating the green body to burn off binders and volatile components. | Advanced ceramics undergo debinding to ensure uniform sintering. |
High-Temperature Sintering | Heating to near-melting point to bond particles and reduce porosity. | Alumina ceramics sintered at 1500–1700°C for full densification. |
Densification | Material shrinks and bonds, forming a solid, low-porosity structure. | Silicon carbide shrinks by 15–20% during sintering. |
Cooling | Slow cooling to room temperature to prevent cracking or warping. | Zirconia ceramics cooled to maintain phase stability. |
Post-Sintering | Optional steps like machining, surface finishing, or metallization for specific applications. | Ceramic components for electronics are metallized for electrical connections. |
Applications | Used in pottery, electronics, aerospace, and biomedical devices for high-performance components. | Alumina for cutting tools, zirconia for dental implants. |
Discover how sintered ceramics can meet your industry needs—contact our experts today for more information!