Spark Plasma Sintering (SPS) is an advanced sintering technique that combines pulsed direct electric current and uniaxial pressure to produce dense materials with unique properties. The process involves four main stages: vacuum creation, pressure application, resistive heating, and cooling. It operates in a vacuum or controlled atmosphere to prevent oxidation and ensure material purity. SPS is characterized by high heating rates, short processing times, and precise control over temperature, pressure, and heating rate, enabling the creation of materials with tailored microstructures and properties. The process is facilitated by a touchscreen interface for programming and control.
Key Points Explained:
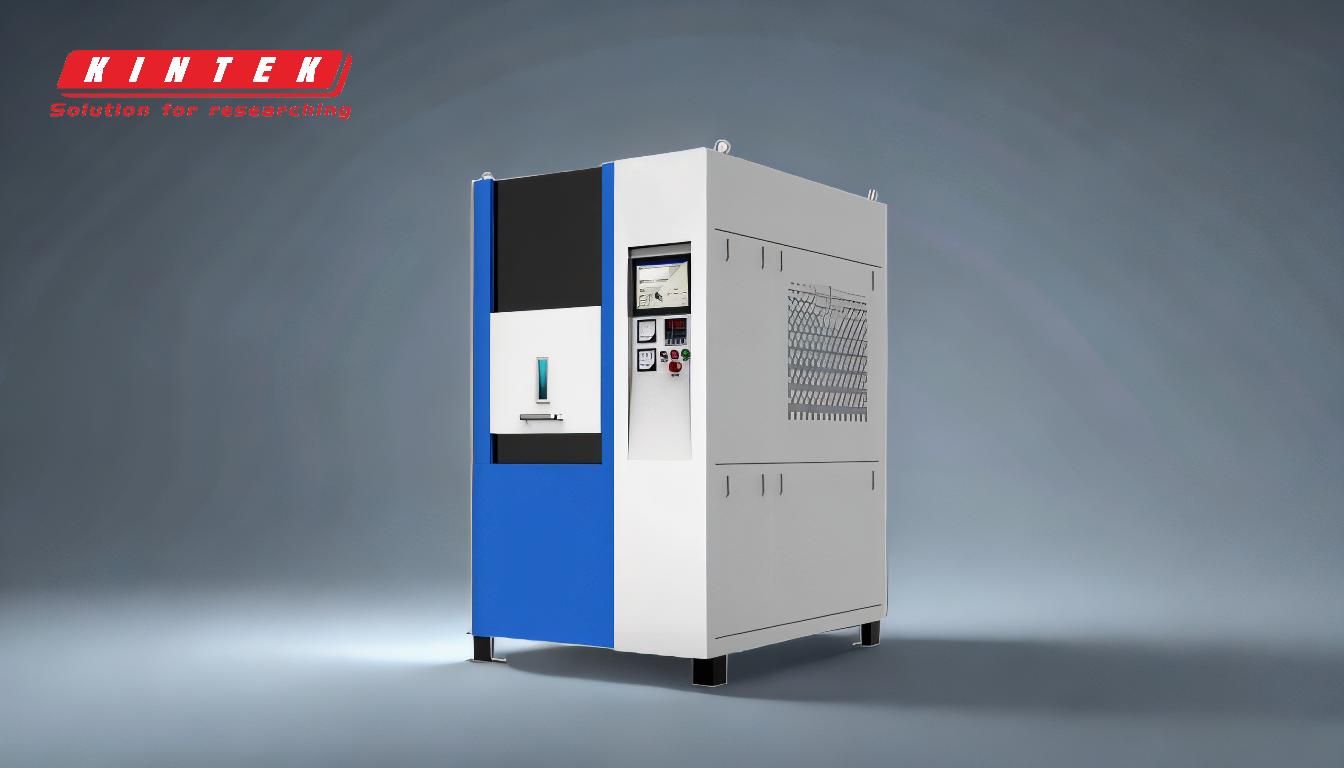
-
Overview of SPS:
- SPS is an advanced sintering technique that uses pulsed direct electric current and uniaxial pressure.
- It is based on a modified hot pressing setup, where an electric current flows directly through the graphite die and the component.
- The process achieves very fast heating times and short process cycles due to pulsed currents and the "spark plasma effect."
-
Key Stages of the SPS Process:
-
Stage 1: Removing Gas and Creating a Vacuum:
- The process begins by removing gas from the chamber to create a vacuum or controlled atmosphere.
- This step prevents oxidation and ensures material purity.
-
Stage 2: Applying Pressure:
- Uniaxial pressure is applied to the powder compact using top and bottom punches.
- The pressure helps in densifying the material during sintering.
-
Stage 3: Resistive Heating:
- Pulsed direct electric current is passed through the graphite die and the powder compact.
- The spark discharge generates localized high temperatures, causing surface evaporation and melting of powder particles.
- This forms necks around the contact areas between particles, leading to densification.
-
Stage 4: Cooling:
- After sintering, the material is cooled under controlled conditions to achieve the desired microstructure and properties.
-
Stage 1: Removing Gas and Creating a Vacuum:
-
Unique Features of SPS:
-
High Heating Rates:
- SPS achieves rapid heating rates, significantly reducing processing times compared to conventional sintering methods.
-
Precise Control:
- The process allows precise control over temperature, pressure, and heating rate, enabling the fabrication of materials with tailored properties.
-
Low Sintering Temperatures:
- SPS operates at lower sintering temperatures compared to traditional methods, minimizing grain growth and preserving material properties.
-
High Heating Rates:
-
Advantages of SPS:
-
Short Processing Times:
- The combination of high heating rates and pulsed currents results in shorter process cycles.
-
Unique Material Properties:
- The "spark plasma effect" inhibits particle growth, allowing the creation of materials with unique compositions and microstructures.
-
Controlled Atmosphere:
- Operating in a vacuum or controlled atmosphere ensures material purity and prevents oxidation.
-
Short Processing Times:
-
Applications of SPS:
- SPS is widely used in the fabrication of advanced ceramics, metals, composites, and functionally graded materials.
- It is particularly beneficial for producing materials with enhanced mechanical, thermal, and electrical properties.
-
Process Control and Programming:
- The SPS process is controlled and programmed using a touchscreen interface.
- This facilitates precise control over the sintering parameters and ensures reproducibility of the process.
By understanding these key points, a purchaser of equipment or consumables can appreciate the unique capabilities of SPS and its potential for producing high-performance materials with tailored properties.
Summary Table:
Key Aspect | Details |
---|---|
Process Overview | Combines pulsed electric current and uniaxial pressure for sintering. |
Key Stages | 1. Vacuum creation 2. Pressure application 3. Resistive heating 4. Cooling. |
Unique Features | High heating rates, precise control, low sintering temperatures. |
Advantages | Short processing times, unique material properties, controlled atmosphere. |
Applications | Advanced ceramics, metals, composites, functionally graded materials. |
Process Control | Touchscreen interface for precise programming and reproducibility. |
Ready to explore how Spark Plasma Sintering can revolutionize your material fabrication? Contact us today for expert guidance!