Fluxing is a critical process in welding and metalworking that serves multiple purposes to ensure the quality and integrity of the joint. The primary functions of flux include preventing the formation of oxides, promoting wetting, cleaning the metal surfaces, and facilitating the proper flow and bonding of the filler metal to the base metal. These actions collectively enhance the strength and durability of the welded joint, making flux an indispensable component in various welding applications.
Key Points Explained:
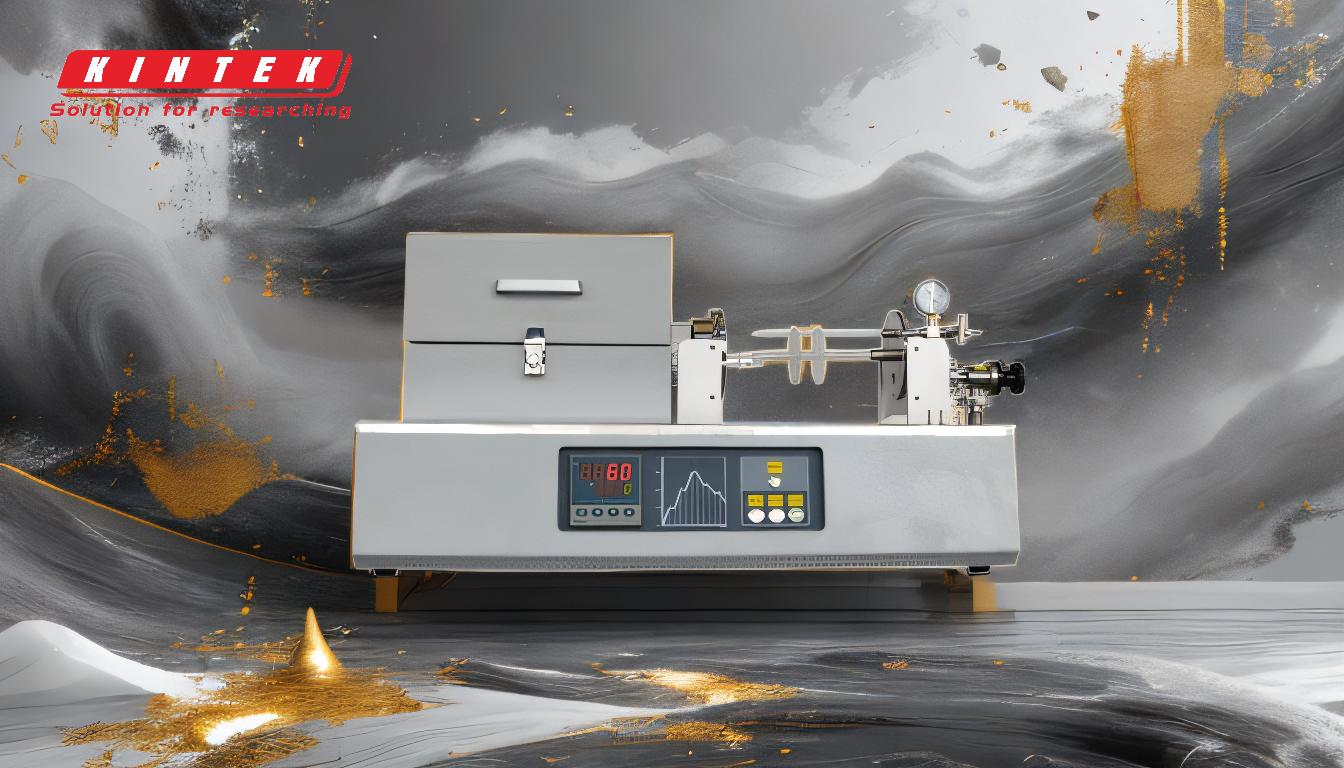
-
Preventing Oxide Formation:
- During welding, high temperatures can cause the metal surfaces to react with oxygen in the air, leading to the formation of oxides. These oxides can weaken the weld and compromise the joint's integrity.
- Flux acts as a protective barrier, shielding the molten metal from atmospheric oxygen. This prevents the formation of oxides and ensures a cleaner, stronger weld.
-
Promoting Wetting:
- Wetting refers to the ability of the molten filler metal to spread evenly over the surface of the base metal. Proper wetting is essential for achieving a strong bond between the filler and base metals.
- Flux lowers the surface tension of the molten filler metal, allowing it to flow more easily and spread uniformly over the base metal. This results in a more consistent and reliable weld.
-
Cleaning the Metal Surfaces:
- Metal surfaces often have contaminants such as oxides, oils, and dirt that can interfere with the welding process. These impurities can lead to poor adhesion and weak welds.
- Flux chemically reacts with these contaminants, breaking them down and removing them from the metal surfaces. This cleaning action ensures that the filler metal can bond directly to the clean base metal, enhancing the weld's strength.
-
Facilitating Filler Metal Flow:
- The flow of the filler metal is crucial for filling the joint and creating a solid weld. Any obstruction or uneven flow can result in defects such as voids or incomplete fusion.
- Flux helps the filler metal flow smoothly over the base metal by reducing viscosity and improving fluidity. This ensures that the weld is fully penetrated and free from defects.
-
Ensuring Strong Bonding:
- The ultimate goal of welding is to create a strong, durable bond between the filler metal and the base metal. Any compromise in this bond can lead to joint failure under stress.
- By preventing oxidation, promoting wetting, and cleaning the surfaces, flux ensures that the filler metal bonds tightly to the base metal. This results in a weld that is both strong and reliable.
In summary, fluxing is a multifaceted process that plays a vital role in welding. It not only prevents the formation of harmful oxides but also promotes wetting, cleans the metal surfaces, and ensures the proper flow and bonding of the filler metal. These functions collectively contribute to the creation of high-quality, durable welds, making flux an essential component in metalworking and welding applications.
Summary Table:
Function | Description |
---|---|
Preventing Oxide Formation | Shields molten metal from oxygen, preventing oxides that weaken welds. |
Promoting Wetting | Lowers surface tension for even filler metal spread, ensuring consistent welds. |
Cleaning Metal Surfaces | Removes contaminants like oxides and oils for better filler metal adhesion. |
Facilitating Filler Metal Flow | Improves fluidity for smooth flow, reducing defects like voids or incomplete fusion. |
Ensuring Strong Bonding | Enhances bonding between filler and base metals for durable, reliable welds. |
Discover how fluxing can improve your welding results—contact our experts today!